Sandvik Coromant: Automating Manufacturing Successfully
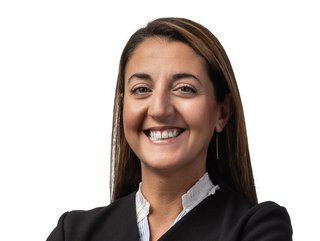
Supply chain manufacturing, as it embraces digital transformation, faces an unmissable concern – a shortage of skills in the workforce.
This poses a huge challenge to consistent quality and production, but can be overcome, according to Sandvik Coromant, through automation.
Staggeringly, the Swedish giant has been using automation in some shape or form since the 1940s, when it introduced numerical controls to manage the machinery related to its punched cards. Since then the manufacturer has consistently implemented the newest automation tools, from Computer Aided Design in the 1970s to cyber-physical systems in the early 2000s.
Sandvik Coromant explains in its whitepaper 'From blueprint to touchless machining' how automation can offer enhanced precision, improve safety and fill labour gaps. It also highlights how automation creates opportunities for staff to be upskilled to handle complex, creative tasks, boosting cognitive skills and confidence.
What's more, it offers a critical overview of six areas of manufacturing where automation can provide value, highlighting the capacity new technology has to benefit manufacturing operations holistically.
06: Design
Computer-aided design (CAD) is a standard among manufacturers for conceptualising and creating 3D product design drafts. It can be used with generative design, which creates design variations within set parameters, to optimise design and eliminate functional challenges.
Once designed, simulation and validation tools can be used to determine quality, feasibility and durability. Like VR and AR prototyping, it situates the design in a simulated real-world environment to evaluate scale, user interaction and overall aesthetics.
Where relevant to the design, tools are used to simulate environments and situations – involving thermal dynamics, aerodynamic simulations and stress – that would be dangerous and costly to create in real life. This allows manufacturers to rigorously test a design’s safety and effectiveness without any real-world risks and costs.
05: Process Planning
Digital twins, or virtual recreations of real-world objects, can be utilised in process planning. They help manufacturers predict disruptions and visualise solutions as they have the power to simulate the entire manufacturing process. Processes can be optimised through AI, helping manufacturers allocate resources and maintain their systems. They can also be simulated to evaluate project costs before they’re enacted by machines in real life.
Internet of Things (IoT) integration also allows data to be collected in real-time from the factory floor, giving manufacturers the data they need to make improvements to products, waste management and machine performance.
04: Operations planning
CAD software can be used to convert drawings and models to machine-ready instructions, known as NC code. This allows manufacturers to enhance the efficiency of their machines, reduce waste and seamlessly transition from design to production.
There are also production scheduling systems which use algorithms to optimise job sequencing and capacity planning tools, which help manufacturers avoid overproduction or underutilisation. Both these automation tools reduce idle time.
Demand forecasting gives manufacturers the data to make informed production decisions, using AI and past data to predict future demand. Resource allocation systems create superior uses of materials and manpower by analysing the real-time needs and data of manufacturers.
03: Production logistics
RFID and barcode systems can be used to track products during the production process and across the supply chain, reducing errors and processing time. Supply chain management software allows for data-focused integration of distributors, suppliers and manufacturers, allowing companies a top-down perspective during decision-making.
Automation means accessing inventory management systems that track, manage and predict inventory levels through software and sensors. Through better management, manufacturers can optimise their storage space, minimising excesses and reducing stockouts. Robotic systems like Automated Guided Vehicles (AGVs) can also be used to transport materials around the factory, reducing labour costs and handling errors.
02: Machining
Robotics takes the risk and unreliability out of dangerous and precise aspects of the manufacturing process. They can be utilised for 24/7 assembly, welding and loading and unloading vehicles, maintaining high levels of productivity.
There’s also CNC machining which uses computerised controls to manipulate machine tools, resulting in a more precise ability to produce and repeat complex patterns. Automation also provides adaptive control systems which can adjust operations in real-time as they monitor machining conditions, improving surface finish and extending the life of tools.
01: Verification
By using automated feedback systems, manufacturers can integrate verification results back into their systems for continuous learning and improvement, resulting in enhanced future operations. 3D scanning and Coordinate Measure Machines (CMM) measure the geometric characteristics of an object, allowing for the detection of anomalies.
There are also automated sensors and software which can be utilised to reduce wastage and monitor product quality during production. These tools result in reduced human error, assured product quality and quicker inspection times.
Sandvik Coromant’s analysis of areas where manufacturers can successfully use automation is partly informed by it's own success. The whitepaper reveals that at the company’s Gimo Plant, batch sizes have shrunk from 202 pieces in 2004 to 25 in 2019, despite designs growing more complex. CAD and CAM have given the company a sustainable and efficient strategy to achieve such intricate design, highlighting automation's increased significance and multifaceted role in contemporary manufacturing.
"We leverage technological advancements through integration of CAD/CAM solutions within our operational and production frameworks, facilitating automated processes.” explains Taline Forsberg, Vice President of Digital Products and Services.
“This approach enables us to effectively adapt to dynamic market conditions while upholding our commitment to maintaining a conducive and relevant work environment for our employees."
Since finding success with Gimo’s hundreds of fully-automated cells, Sandvik Coromant has increased output by 55%. In 2008 the company was producing 8,800 pieces per human operator each year; by 2018, this figure had skyrocketed to 14,000.
By automating supply chain operations, manufacturers can achieve superior productivity, efficiency and oversight. Integrated automated systems that analyse and monitor ongoing operations provide invaluable data for key decision-making, helping manufacturers improve their processes today and tomorrow.
******
Make sure you check out the latest edition of Manufacturing Digital and also sign up to our global conference series - Procurement & Supply Chain 2024 & Sustainability LIVE 2024
******
Manufacturing Digital is a BizClik brand.
- WEF, Kearney Report: Manufacturing’s Rhetoric vs RealitiesProduction & Operations
- Immensa and Intaj Suhar partner to boost Omani manufacturingProcurement & Supply Chain
- Daikin Applied's Dedication to Sustainable ManufacturingProduction & Operations
- Top 10: Chief Manufacturing OfficersProduction & Operations