Article
AI & Automation
#Oscars2015: How the Oscar's iconic statuettes are made
By Glen White
May 16, 2020
undefined mins
Share
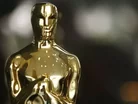
The Art Deco style Oscars statuettes are central to the annual Academy Awards in Los Angeles. The gold figurines are the epitome of perfection, glamour...
The Art Deco style Oscar’s statuettes are central to the annual Academy Awards in Los Angeles. The gold figurines are the epitome of perfection, glamour and glitz but do you know how they are made?
Manufacturing Global goes behind the scenes of the 10-day manufacturing process and finds out.
- The gold statuettes’ road to California starts 2,000 miles away in a Chicago workshop.
- In Chicago, the figures, which stand at 13.5 inches tall and weigh a hefty 8.5lbs, are painstakingly manufactured by the skilled craftsmen of R S Owens, who have made the Academy's highest award since 1983.
- The value of the raw materials is around $900, however, once awarded the worth of the statues can catapult - despite an official ban by the academy to sell them on.
- Although they shine golden, and are clad in a hefty coat of 24-carat gold, at their core an Oscar is made of a variant of pewter - a special alloy called britannium made especially for Oscar figures.
- Each statuette is made individually, and there is only one mold, which is used for every single Oscar.
- The liquid metal, at a scorching 570°F, is poured into a mold in the shape of a European knight, holding a downward-pointing longsword in both hands.
- The statues are then sanded down, polished and coated with other metals.
- The statues are painstakingly sanded by hand to match their iconic 1928 design. The slightest blemish leads to the figure being scrapped and started over.
- The figure shows a stylized knight wielding a longsword while standing atop a five-spoked reel of film.
- After being cast, the figures are sanded down then polished until the britannium alloy glimmers - even though it will not be the final coat on display.
- The Oscar is then treated to remove any grease of specs of other material, and engraved with a serial number. Around fifty of the awards have been made each year. So far 2,947 have been awarded, with at least 25 more added this Sunday.
- Next, the statue is dipped and electro-plated - a chemical technique that creates an even coating - in a metal bath. First the models are coated in copper, then nickel, then silver - and finally in 24-carat gold.
- Between each stage the figure is polished again to deepen its luster ahead of the equally glitzy presentation ceremony.
- The figures are finally attached to a black nickel base - but are left unlabeled until after the ceremony to preserve the secrecy of the winners.
- For the last step, the Oscar is covered in a lacquer to protect it from knocks and scratches. Finally, they are packaged in Styrofoam and flown under guard to Los Angeles for the final ceremony.
- Eventually each newly cast Oscar will be affixed with a plaque bearing the name and category of its recipient. At first the statues were taken back by the Academy while the plaques were engraved - but now eager stars can have their statues built up at the ceremony itself.
- If at any stage in the days-long process an Oscar does not come out perfectly, the figure is destroyed and a new one started to replace it.
- Once the statue is finished, it is guaranteed for life, and actors can send damaged figures back to have them replaced or brought back to their original brilliance.
Share
- An Overview of Kamala & Trump's Plans for US ManufacturingProduction & Operations
- The US Could Soon Lead In Silicon Carbide ManufacturingTechnology
- HSBC: Behind UK Manufacturers Optimism on US ManufacturingProduction & Operations
- US Battery Manufacturing Boost Helps Industry & CommunityProduction & Operations
RelatedContent