How Manufacturers Embraced Technology in 2024
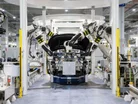
Leading industrial robot manufacturer Universal Robots's survey 'How Manufacturers are Embracing Technology in 2024' highlights the impact of emerging technologies, ongoing concerns and areas of prevailing focus for manufacturers.
Here we breakdown its biggest findings, with insights from Anders Billesø Beck, Vice President for Strategy & Innovation at Universal Robots.
AI goes beyond hype
AI has been one of the biggest manufacturing topics in 2024.
It's been designated everything from a key strategic tool to secure manufacturing's future and a technology set to erode labour in an industry which already faces a prominent hiring gap.
Either way, as Sandvik Coromant recently expressed, it's here to stay. So while embracing its potential, manufacturers also have a responsibility to ensure nobody is left behind.
And embrace it they have.
Earlier this year we reported on Rockwell Automation's 'State of Smart Manufacturing' report, which highlighted the scale of planned manufacturing investment in AI. 85% of respondents in the report had already invested or planned to invest in AI or machine learning. And the majority of those turned those plans into reality, turning AI into a notable business imperative.
Contributors to the report like Microsoft notably agreed.
"At Microsoft, we see a future where intelligent factories powered by people using AI and Generative AI become the norm, not the exception,” says Gary Nafus, current Chief Sales Officer at SailPoint and former Vice President of US Manufacturing at Microsoft.
"Emerging technologies delivered through partnered ecosystems are helping to pave the way for sustainable, autonomous operations that redefine productivity.
"Imagine production lines optimised by data insights, robots collaborating seamlessly and materials sourced responsibly. This isn't just a vision, it's a reality we're building together. Let's unlock the future of manufacturing, one innovation at a time."
The results of the study by Universal Robots indicate this future is already being created. Something which doesn't surprise the organisation.
"This of course isn’t a complete surprise to us at Universal Robots," adds Anders.
"We are experiencing huge interest in physical AI because combining robotics with the power of machine learning and artificial intelligence can deliver incredible gains.
"The recent development in the application of AI based technologies is very visible when looking at our extensive ecosystem of partners developing components, application kits and solutions for our cobots (collaborative robots).
"We recently reached the milestone of having launched 500 products through the UR+ ecosystem and as the ecosystem keeps growing a significant trend is the rapid growth in the number of applications and solutions based on AI technology. And there is much more to come."
Manufacturing has a digital future
Here at Manufacturing Digital - as the name implies - we believe the future of manufacturing is rooted in technological innovation.
According to the survey by Universal Robots, this is very much the case, with more manufacturers feeling confident and motivated to invest in emerging technologies.
"Not very long ago there was widespread hesitancy towards connecting robots and other production technologies, to the internet," Anders explains.
"It has been a question of both why – how do I benefit from being connected? – and then cybersecurity.
"The latter is still extremely important but as capabilities have risen, so has the level of safety.
"And as to the former, the why digitalise question, the answer has become much simpler: Because the possibilities it unfolds are incredible."
Indeed, the growing proliferation of Industry 4.0 has answered that value question for most manufacturers, with industry leaders highlighting impressive gains in productivity, efficiency, insight, organisation and connectivity.
Anders highlights how these technologies are having such a profound impact in the field of industrial robots alone.
"Using a digital twin of your cobot installation, for example, allows you to run endless simulations before you implement your cobot in real life, saving you both time, resources and money," he says.
"And with the Industrial Internet of Things (IIOT) you can for example improve efficiency and reduce downtime through Overall Equipment Effectiveness (OEE) visualisation and predictive maintenance."
Based off benefits such as these, almost half (47%) of survey respondents said they were already using technologies like digital twins, IoT and cloud computing.
Anders predicts this number will rise even further in the next few years.
"Digital manufacturing will enable manufacturers to shift towards high-volume, high-mix production and contribute to more resilient supply chains, competitive data utilisation, and sustainability goals," he says.
"And it will be an investment worth making, as the reward will be higher quality, reduced downtime, better predictability and improved cost optimisation."
Quality remains the most important metric
The survey by Universal Robots highlights something critical: that the biggest focus and most important metric to manufacturers when implementing new technologies is improving quality.
"The survey shows us that manufacturers are embracing technology with a clear focus on meeting rising demand and developing both products and outputs," Anders explains.
"Improving product quality, increasing productivity and improving accuracy are the three main reasons for adopting new technologies like robotics, digitisation and AI.
"Respectively 54, 50 and 49 % of the respondents highlighted these three as reasons to implement new technologies."
Other reasons that manufacturers seek to implement technology is to create superior working conditions for workers and to become more sustainable.
What Universal Robots found is that focusing on using technology to enhance quality also leads to marked improvements in these other areas.
This is a pretty logical conclusion as the pursuit of quality comes down to greater efficiency and more efficient factories are typically greener and safer.
What was surprising however in the survey was the feedback they received about hiring and technology.
"Interestingly in our survey, only 11 and 12 % note the difficulty of attracting the right workers as a driver for investing in new technologies – even though demographic projections are predicting declining workforces in many countries," Anders adds.
"Automation will inevitably play a key part in the attempts by businesses and governments to maintain a high level of productivity and competitiveness when populations and labour forces shrink and attracting the right workers becomes gradually harder. I expect this number to be much higher if we ask the same question again in five or 10 years."
ROI remains top concern
The survey also highlighted that the biggest barrier to adopting Industry 4.0 is concerns over the Return On Investment (ROI).
"Manufacturers naturally want to prioritise investments that assure maximum efficiency and value," Anders explains.
"Here fast integration, reliability, ease of use, precision and flexibility are all important factors (all of this is, by the way, is exactly what you get when investing in cobots).
"While ROI takes the lead as a number one concern when considering technology investments (32%), it doesn’t stand alone, and other concerns are nearly as common.
"These include concerns about usability, a lack of in-house expertise, concerns over safety and potential disruptions to existing operations. All these 'roadblocks' are mentioned by around 20% of the correspondents."
He explains that addressing these concerns comes down to proving ROI through greater innovation and enhancing user confidence through training and accessibility.
"In robotics, we need a two-headed mission: We must keep pushing the frontiers for what tasks automation, digitisation and AI can solve, and at the same time we must create solutions that are even more intuitive and simple while providing the training needed to build confidence in the existing workforce," he says.
"Ultimately, no matter how advanced robotics and AI become, the human element remains paramount."
Make sure you check out the latest edition of Manufacturing Digital and also sign up to our global conference series - Manufacturing & Mobility LIVE
Manufacturing Digital is a BizClik brand