Scania Takes Vehicular Remanufacturing Beyond Aftermarket
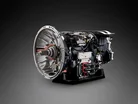
Transitioning towards a circular economy is increasingly becoming a target for forward-thinking industries, aiming to slash carbon emissions, fortify supply chains and foster economic growth.
In an ambitious move, Scania is propelling vehicle manufacturing into the future by incorporating reused components directly into its main assembly line in Sweden, marking a significant milestone for heavy vehicle manufacturers worldwide.
This innovative approach, particularly through its gearbox ‘remanufacturing’ project, has notably reduced material use by half and cut carbon emissions by approximately 45% compared with the production of a brand-new gearbox.
Interestingly, these remanufactured gearboxes undergo the exact stringent quality and function tests as those made from new parts, successfully passing all the rigorous standards Scania demands of its new components.
“What an achievement by the project and everyone involved,” says Fredrik Nilzén, Head of Sustainability at Scania.
“This remanufactured gearbox is a compelling example of how the manufacturing of heavy vehicles can become more sustainable, circular and efficient, while still retaining the highest quality standards.”
The iReGear Project
The iReGear project stands as a collaborative research effort between Scania, KTH Royal Institute of Technology and Scandinavian Transmission Service AB, with Vinnova, Sweden's innovation agency, backing the initiative.
“STS has been remanufacturing gearboxes for more than 50 years," says Ola Stålebo, CEO at Scandinavian Transmission Service AB.
The partnership behind the iReGear project envisages this initiative leading the automotive industry towards a more circular future.
“It’s amazing to be able to challenge the old perception that remanufactured parts only can be used for aftermarket purposes," Ola adds.
“Today, we can proudly reflect on a period of successful collaboration, where we have achieved breakthroughs in sustainable technology.
“This project truly shows that it might not need to stop at just one idea, but it could become a reality in the near future.”
The iReGear project partners hope the scheme will lead the way towards circularity in the automotive industry.
Farazee Asif, Assistant Professor at KTH, agrees, adding: "This research provides the first evidence to support the argument that it is feasible to envision future manufacturing organisations seamlessly integrating manufacturing and remanufacturing operations to develop Circular Manufacturing Systems that consume fewer resources, produce fewer emissions and cost less without compromising on quality and performance.”
Currently, remanufacturing in Europe’s automotive sector is predominantly an aftermarket activity, representing a mere 1.1% of new manufacturing.
Yet, with the global automotive aftermarket projected to grow significantly, reaching an estimated US$568bn by 2032, integrating remanufacturing processes within OEM practices could have a profound impact on reducing emissions from automotive manufacturing.
Scania’s integrated approach to sustainability
Scania’s sustainability efforts are seamlessly integrated into its operations.
Since setting science-based targets in 2020, the company is on track to cut land transport emissions in half by 2025 from its 2016 levels.
“In 2023, the company continued to deliver customer value and made good progress getting our order to delivery flows back on track," adds Christian Levin, President and CEO at Scania and TRATON GROUP.
Moreover, Scania’s commitment to sustainability is evident in its decision to exclusively purchase 100% green steel, batteries, aluminium, and cast iron by 2030.
******
Make sure you check out the latest edition of Manufacturing Digital and also sign up to our global conference series - Procurement & Supply Chain 2024 & Sustainability LIVE 2024
Manufacturing Digital is a BizClik brand