Superplastic Forming Method To Boost UK Aerospace Industry
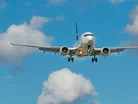
A new hybrid manufacturing method is boosting manufacturing efficiency and capability for key aerospace components in the UK. Global manufacturers of aircraft may in the future put this method to use in daily production, transforming their approach.
SDE Technology is a lightweight engineering business based in Shropshire, that is leading the initiative to develop a new superplastic forming process. This innovative process will enable the company to expand into the aerospace market.
“Our team has a combined 200 years of experience in material science, modelling, and superplastic forming, which makes us well-placed to support the development of new techniques that could make a big impact on the entire aerospace industry.” Said Evgenia Yakushina, forming team lead at the Advanced Forming Research Centre.
“This work has the potential to unlock opportunities for manufacturers to offer improved, quicker methods of producing key parts for aircraft. So far, the research has demonstrated huge potential with important parallels between the new hybrid method and the traditional approach already evident.”
Superplastic forming is a near-net shape manufacturing method for creating thin-sheet metallic components. This method is used to create complex-shaped titanium parts, like those used by the aerospace sector.
SDE’s superplastic forming process is a hybrid technique, estimated to shorten the forming cycle time by half and cut costs by as much as a quarter. As SDE Technology enters the aerospace market through this technology, the UK supply chain’s capacity to manufacture high-value titanium parts will be strengthened.
“This project has huge potential for not only us as a business but also the whole aerospace sector.” Richard Homden, CEO of SDE Technology.
“It is fantastic to be working collaboratively to explore new manufacturing techniques. Hot forming was not previously our area of expertise, but with the technical support and knowledge base from the AFRC, we can see it becoming a core element of our business plans moving forward.
We’re especially excited by the opportunity to become part of the supply chain for aircraft and provide Boeing with UK-manufactured components.”
The AFRC team has previously explored the hybrid technique, but this collaboration scales the method for the industrial needs associated with the aerospace sector. SDE Technology aims to prove through an 18-month research project, funded by the Aerospace Technology Institute programme through NATEP, that complex-shaped titanium components can be manufactured to the same tolerances, quality and specification compared to traditional superplastic forming.
Additional funding has been secured to evaluate the method's carbon footprint, which could be cut significantly through its shortened forming and heating times, using lower temperatures of around 800°C.
These high temperatures also remove the oxide layer typically formed on titanium components during superplastic forming, which is known as the alpha case. Alpha case normally requires powerful acids to remove, meaning this method enhances the efficiency of the overall process by removing this complex step.
The project is supported by the Advanced Forming Research Centre (AFRC) within the National Manufacturing Institute Scotland (NMIS) Group and is operated by the University of Strathclyde. The project forms a key part of the National Aerospace Technology Exploitation Programme, making up part of the High-Value Manufacturing Catapult (HVMC).
Boeing and Timet UK are industry collaborators, supporting the project with technical and business activities.
"Boeing is committed to working with partners across the globe on projects that advance innovation in the aerospace industry.” said David Milliken, technical lead for forming and forging at Boeing.
"This is a very exciting project with the chance to further advance manufacturing processes in the UK and we look forward to contributing to this collaboration.”
"This is an exciting technology; we welcome the opportunity to be part of a collaborative research programme aimed at solving specific customer problems.” added Nick Humphreys, senior R&D engineer at Timet UK.
**************
Make sure you check out the latest edition of Manufacturing Digital and also sign up to our global conference series - Procurement & Supply Chain 2024 & Sustainability LIVE 2024
******
Manufacturing Digital is a BizClik brand.
- Bend-Forming: A Big Breakthrough for Aerospace ManufacturingDigital Factory
- Boeing, NASA and Pratt & Whitney Drive Sustainable AerospaceSustainability & ESG
- Why has CCEP Spent Millions on ASRS for its Wakefield site?AI & Automation
- Amcor & Power Roll: Pioneering Solar Photovoltaic FilmSustainability & ESG