Infor: The Evolving Role of Digital Twins in Automotive
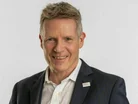
Dr Henning Dransfeld, Senior Director of Industry Strategy & Solutions at Infor believes automotive manufacturing is at a crossroads.
He says that despite decades of innovation, many manufacturers face mounting challenges, from rising costs to fragmented systems and cybersecurity risks.
At the same time, customer expectations are growing, and competition is intensifying.
He points to digital twins as a lifeline amid these pressures, highlighting its transformation from R&D exploration to factory implementation.
Manufacturing Digital spoke to him to learn more.
What are the origins of digital twins?
UK digital twin market is set to make a record a 30% annual growth rate during 2022-27.
As virtual counterparts of physical products and processes, this technology promises to transform production efficiency, cost savings, customer engagement and decision-making.
Yet, as their use expands into production lines and customer insight modelling, the risks have grown too, from data silos to vulnerabilities in cybersecurity.
Initially, digital twins were used for product development, particularly in the automotive industry’s R&D phase.
Ford first used hardware-in-the loop in the 1980s to test electronic control systems, such as those in powertrains and ABS.
Other manufacturers followed suite and in 2010, Bugatti incorporated HIL for precise calibration of control systems.
Today, digital twins have gone far beyond R&D, now integrating across the entire supply chain, providing real-time insights that improve everything from design processes to customer engagement.
With the integration of IoT, AI, and cloud computing, digital twins have become critical tools for manufacturers looking to predict and optimise operations at scale.
What are the challenges of digital twins and how can we mitigate them?
While this technology has revolutionised how manufacturers optimise their operations, it is not without challenges.
The vast amounts of sensitive data generated —from R&D insights to production metrics and customer engagement details— make these systems prime targets for hacks by increasingly organised and hostile forces.
Indeed, a study by MakeUK found that 42% of the country’s manufacturers experienced cybercrime last year, with a quarter reporting significant financial losses as a result of these attacks.
This is further exacerbated by home grown IT infrastructures that often provide open doors through old hardware and applications fulfilling a function that may not be serviced and not even be on the books anymore.
These fragmented systems and siloed data slow down decision-making and hamper the power of a technology that is rooted in real-time data.
Manufacturers can mitigate these risks and address vulnerabilities by adopting cloud-based platforms.
These feature robust security measures like encryption, threat detection, and continuous monitoring, ensuring sensitive data is stored and managed securely.
How can digital twins be harnessed to deliver value for automotive manufacturers?
The value of digital twins extends far beyond operational efficiency.
As manufacturers move towards subscription-based models, understanding exactly how stakeholders in their ecosystem use products is crucial for delivering value.
Armed with these insights, companies can deliver predictive maintenance, tailored upgrades, and subscription services.
This transforms a one-time purchase into an ongoing relationship, creating continuous value for customers.
Embracing digital twins helps get manufacturers to the pinnacle of innovation and resilience.
These tools do more than streamline operations—they form the backbone of a flexible, future-proof strategy.
By embedding digital twins into decision-making, manufacturers not only enhance efficiency but also cultivate long-term customer loyalty, securing their position in a fast-changing market.
At scale, digital twins enable manufacturers to innovate faster and operate more efficiently.
However, as their use increases, so does the need for robust cybersecurity.
To stay competitive, manufacturers must adopt advanced security measures—such as encrypted cloud platforms—to safeguard operations while driving continuous innovation and efficiency.
Explore the latest edition of Manufacturing Digital and be part of the conversation at our global conference series, Manufacturing LIVE.
Discover all our upcoming events and secure your tickets today.
Manufacturing Digital is a BizClik brand.