NSK Gets Its Bearings From Data-Driven Strategy
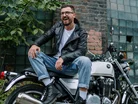
In today’s digital economy, data is a valuable, in-demand currency that can drive informed decision-making and generate phenomenal change.
The manufacturing industry is no exception, as is evident from this description of digital transformation from Parm Sandhu, VP of Enterprise 5G Products and Services, NTT DATA.
"Manufacturers are accelerating digital transformation to harness Industry 4.0 and smart factory technology for operational excellence, automation and digital workers,” he says.
“Private 5G provides a secure, low-latency network for all factory devices, from tablets to sensors. Combined with Edge AI, it delivers real-time critical information on operations, enabling intelligent asset tracking, proactive management and maintenance.”
Every solution Parm describes is dependent upon data. From sensors to AI to digital twins to private 5G, it’s the foundation that makes digital transformation possible.
Manufacturers like John Deere have recognised this, making data an integral part of their strategy to enhance operations and deliver superior customer service.
In its ‘Machinery And Equipment Report 2024’, Bain & Company identified John Deere as an OEM that, through investing billions in data, successfully transitioned from tractor manufacturing to providing solutions for precision architecture.
From sprayers that can distinguish weeds to storing crop data in the cloud to self-driving tractors, John Deere has used data to make farming more consistent, productive and efficient.
This year John Deere has pursued further data innovation by integrating its new Eagle Raptor Software with its M Series Controllers.
"The addition of New Eagle Raptor software to our M Series Controllers gives our OEM customers a comprehensive control system solution that was not offered before,” says Dan Dougherty, Sales and Marketing Leader for Electronic Systems at John Deere.
“Our customers push the limits of mechanical durability and need a rugged and reliable solution on the job site that can provide critical machine control functions.”
Another heavy machinery manufacturer pursuing a data-driven digital transformation strategy is NSK.
NSK: A data-powered machine
NSK, also known as Nippon Seikō Kabushiki-gaisha (Japan Precision Company), is a global leader in automotive components, bearings and linear motion.
The largest bearings producer in Japan, NSK manufactures bearings, industrial components and precision machine solutions. Founded in 1916, NSK is a global operation with 30,000 employees.
The manufacturer has 65 production plants across fourteen countries, 144 overseas operations in 29 countries and manufactures approximately 3 million new bearings daily.
NSK is focused on quality: something that is critical, considering the incredible diversity of industries across the world that depend on NSK to run.
NSK: supplying global industry
NSK’s presence is down to the reliability, quality and advanced engineering of its products, including its specialist ‘super precision’ bearings.
Another area where NSK is super precise is with its data-driven digital transformation strategy, led by Jeremy Myer, NSK’s Manufacturing Strategy Manager.
“My career has been influenced partly by my personal interests and skills in building databases, starting with my Lego and baseball cards as a kid,” Jeremy explains.
“The other was the closing of a plant early on in my career, which forced me to pivot to something different and exposed me to an executive team and way of working built with a continuous improvement mindset.
“I was able to see that there are challenges and opportunities in manufacturing that everyone faces that, when solved, can have impacts across the industry.”
This insight has informed his shaping of NSK’s digital transformation strategy, which has always been ahead of the curve – including pursuing extraordinary innovation in the mid to late 2000s.
Jeremy says NSK’s biggest strategic change has been its growing reliance on connected data, noting that: “Data is a solution to the long tradition of ‘gut feel’ decision making.”
For example, productivity. This is traditionally thought of as a shop floor equation – what gets done, divided by how long it takes.
It sounds simple. But Jeremy argues this single KPI is misleading, an embodiment of the “gut feel” approach.
“Inside of it are many different factors you need visibility on,” he explains. “ So we measure all the things, focusing on collecting and connecting data to analyse as opportunities for efficiency and productivity.”
When you start evaluating productivity through data like this, other pertinent questions arise. The ones Jeremy raises have been incorporated into NSK’s manufacturing strategy.
“In the effort to improve efficiency and productivity by capturing, connecting and analysing data, could you make that measurement process even more efficient and productive?” he says, pointing to AI as a technology that could help in this arena, automating analysis and collecting to save time and resources.
“As an engineer, I'm constantly thinking about the process and effort that goes into anything we do.”
The benefits of capturing manufacturing data go beyond just enhancing productivity. Data has a vital role to play in operating and managing machines, enabling predictive maintenance, performance analytics and the futureproofing of vital systems.
NSK recognises this, which is why since 2006/7 the company has mandated that any new equipment and machines installed have to be data-driven and capable of data capture.
“Instead of being reliant on verbal shift handoffs, notebook-driven transcription, or a dozen disconnected spreadsheets, we started a journey to more thorough, connected data and more relational processes for greater visibility,” Jeremy says.
“Now, we can draw better conclusions on connected data that captures what the machine is telling you and the observational human elements, joining these two things together for better KPIs and smarter decision making.”
This machine monitoring grows even more vital when we consider that NSK, like most manufacturers, has a mixture of legacy equipment and newer machines across facilities. Data has helped them strategically assess when to keep, retire and update machines, keeping cost impact and potential downtime low.
“Any replacement consideration starts by answering a basic set of questions - is the machine still working? Is it operating with acceptable limits for performance/failure tolerance?” Jeremy notes.
“If so, we leave it in place, and many older machines are still monitored using paper processes and basic observations of performance with how often it’s in each state as a performance metric, as key points in the replacement decision-making process.”
Innovation here does not mean instantly updating every machine to the newest, swankiest model: for most manufacturers, this is not feasible with associated downtime, nor is it always necessary. NSK uses data to intelligently assess where modifying machines can drive real value and where they need to prioritise productivity and cost instead.
“We balance the current performance metrics and KPIs against opportunities where modern analytics can play a role in improvement,” says Jeremy.
“So it's not a complete overhaul of every process, but more like paying attention to the most painful ones that a database-driven approach can improve/make more efficient.”
A data-based approach has also elevated NSK’s strategy in a critical area – safety.
Manufacturing is statistically one of the highest-risk sectors, with a five-year average fatal injury rate of 0.68% per 100,000 workers – 1.7 times greater than the broader industry rate. One of the biggest risks to workers is contact with large industrial machinery, which is pretty unavoidable for a manufacturer like NSK.
“One of NSK's big priorities is how we measure and report on safety, using a dashboard to bring together key inputs and metrics to measure/report,” explains Jeremy.
“This has evolved from the "old way" of using site-specific surveys input into an excel spreadsheet, oftentimes too late for any real corrective or preventive measures to have an impact.”
NSK has a ‘Take A Minute for Safety’ practice, where thousands of workers are asked to document once a month what they observe in each of NSK’s sites. This used to be completed via paper, but now NSK has kiosks on each shop floor where employees can input observations through an app.
Through this, observations are quickly turned into trackable actions. Employees engage with a customised risk assessment form that can be dashboarded for site-to-site comparison, without any incomplete, old or disconnected files. This enables NSK to keep its sites and people safe while better tracking maintenance, site visits, training and capturing permits.
Data here is a vital ecosystem that strengthens the broader whole, improving the visibility of workers' and customers' needs and NSK’s capacity to address them.
“You're not the only one in this transformation,” Jeremy says.
“Look in your network, talk to your peers, seek out new ideas... you can learn anything from anyone, large or small, inside or outside your industry, seeing not only what to do but also what not to do.”
Data is all about learning the truth. It highlights quantifiable reality, helping people across industries overcome biases and assumptions and better understand where and how they need to improve.
In short, data helps manufacturers build a vision for tomorrow.
To read the full story in the magazine please click HERE.
**************
Make sure you check out the latest edition of Mining Digital and also sign up to our global conference series - Manufacturing LIVE 2024
**************
Mining Digital is a BizClik brand