Production 4.0: Porsche’s Factory of the Future
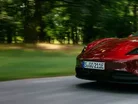
Investing €80mn into its Zuffenhausen plant Porsche is making factories of the future a reality. This plant allows Porsche to install up to 200 engines a day, using 100 technical innovations in its production alone.
“Porsche Production 4.0 is a natural evolution of the existing production system – a continuous improvement with the help of new technologies and methods. Applications from the digital world are networked with the physical world,” states Porsche.
As a result, the automotive manufacturer has identified six fields of action to continuously develop: production system, resource efficiency, work organisation, new technologies, digitalisation and communication.
Focusing on People
Utilising the modern single-line - a typical manufacturing philosophy for Porsche - the concept focuses on human beings.
Each employee carries out as many steps as possible and in principle, each should be able to be deployed throughout the entire plant. Porsche uses robots specifically where absolute repeatability is critical.
In the manufacturer’s ergonomically optimised assembly of the engine plant, all tools and processes were designed to support people in their work. Wireless EC screwdrivers are also used to know the exactly defined torque characteristics.
“But ‘smart’ does not just mean computer-based or robot-controlled. A so-called quality control loop – with employees from all areas relevant to production – ensures that in the event of anomalies, the assembly processes are intervened upon at an early stage, thus avoiding an increased error rate,” added Porsche.
Porsche’s Production 4.0 is not only innovative but sustainable. Carefully uses resources in production, €1mn and 2,254 tons of carbon dioxide were saved in 2016. The goal is an emissions-neutral factory.
Augmented Reality
Experimenting intensively with augmented reality at its quality centre, Porsche is using the technology to obtain even faster and more precise information about individual components.
As a result, work steps or product details can be displayed directly to the talbot and supplemented by computer-generated information.
“Even the smallest deviations from the standard are detected immediately in this way and it becomes clear where vehicle body components fit together perfectly or not yet ideally,” said Porsche.
Optical Digitalisation
Checked quickly and precisely using special optical technology, Each body component made by Porsche is completely digitalised and measured three-dimensionally.
Measuring 16 million points per scan, the entire component geometry can be represented in a high-resolution point cloud.
“In the quality process, deviations of each individual body point from the CAD data can be determined in the shortest possible time. Using the digitised measurement data, the deviations are also precisely visualised in a full-surface 3D representation,” said Porsche.
Extensive Options
Why may things work digital, not everything does. Porsche highlights that physical vehicle models will continue to be necessary in the future for the final test and assessment of vehicles and individual components.
“Cubing is a process in which true-to-original models are used that offer extensive testing and analysis options. All production parts are displayed, assembled, tested and harmonised in their original size,” concluded Porsche.