Schneider Electric: Training Key to Modernising Operations
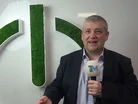
In today’s fast-evolving world, organisations must quickly adapt to new technologies that will support their changing energy demands, while also addressing chronic skills shortages.
David Pownall, VP Services at Schneider Electric UK & Ireland, explores how the provision of robust practical and digital training helps to foster a culture of continuous learning that will add resilience, upskill engineers, attract and retain the best talent.
Organisations are expected to innovate and maintain their competitiveness, while also having to digitally transform and modernise operations efficiently and effectively.
However, as companies integrate connected digital solutions to support their electrical installations, they have to be mindful of the need to balance traditional skills with the new competencies required.
"Technology alone will help to modernise the infrastructure and operations," David says, "but it's the investment in training that will drive a digital transformation while preserving the expertise needed to manage existing equipment.
"At the very least, organisations need to equip engineers with the basic skills needed to operate the suite of digital tools being installed to optimise and improve the resilience of critical infrastructure."
Meanwhile, existing equipment is still the pillar of many manufacturing sites in spite of what David calls "the rush" to adopt to digital solutions.
"Only a few years ago the IET estimated that some electrical installations, wiring and components date as far back as the 1950s," he continues.
"So, engineers need to be able to manage, repair and maintain both existing and modern equipment to ensure operations run seamlessly."
Professional training gives engineers a new spark
Comprehensive training bridges the gap between digital and on-site operations, empowering engineers to excel.
With solid foundations in place, teams can collaborate seamlessly with third-party experts, tackling complex tasks like predictive and condition-based maintenance.
The result? Harmonised teams, improved performance and engineers equipped to succeed both onsite and remotely.
David adds that "besides simply upskilling engineers, putting a greater emphasis on professional development through dedicated training programmes sends a positive message to the engineering and maintenance teams.
"It demonstrates their value, empowers them to leverage their in-depth knowledge of the infrastructure and applications they manage, fosters innovation opportunities and equips them with the technological insights needed to unlock new possibilities.
"Without them it would be very difficult to navigate the complexities of the electrical infrastructures that power today’s businesses."
Businesses take the academic approach
Schneider Electric’s flexible training programme equips engineers with specialised skills in areas such as AI, automation and safety.
Offering virtual and in-person learning, it supports modern engineers’ needs. With courses available online or at specialist academies across the UK and Ireland, teams can foster continuous learning and achieve operational excellence.
"Many engineers benefit from the hands-on training the academies provide, especially the Safety Academy that offers everything from a basic introduction to High Voltage and Low Voltage systems, through to comprehensive training and accreditation for nominated authorised persons," David says.
"In-person training allows participants to interact directly with equipment, tools or real-life scenarios, making it easier to apply theoretical knowledge in practice.
"This is particularly important for technical or complex skills. In addition, access to training and professional development can help to improve staff welfare and retention, with 94% of employees stating that they would happily remain in post if that was available."
Honing traditional and digital skills
"Businesses need to be mindful that while it is essential to modernise, there will always be a requirement to manage and maintain existing equipment," he asserts.
"So, it’s vital that we go back to basics and bridge the skills gap.
"With the right training," David continues, "experienced engineers can master digital technology, while giving younger engineers the scope to understand the mechanics of existing equipment. From apprentices to senior professionals – this is the key to marrying both practices."
It equips engineers with the essentials to navigate change, embrace digital technologies and tap into third-party expertise.
By unifying teams and boosting productivity, this approach empowers engineers with the tools to grow professionally, adapt confidently and thrive in an evolving industry.
Explore the latest edition of Manufacturing Digital and be part of the conversation at our global conference series, Manufacturing LIVE.
Discover all our upcoming events and secure your tickets today.
Manufacturing Digital is a BizClik brand.