Transformation to Industry 4.0 Depends on Seeing Clearly
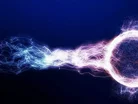
The trigger for transformation can be proactive or reactive. Often it is both. Many companies have a long-term plan for transformation, but they also pivot quickly to new ways of working, driven by immediate opportunities – and threats.
Covid-19 is a case in point. The pandemic immediately threatened global supply chains and in some cases decimated demand. But it also taught many organisations with long-term transformation strategies how to effect change management quickly.
As automotive workers stayed at home on lockdown, car makers started to examine the case for a machine-only production line and the technology required to deliver it.
As airlines struggled with falling demand, many accelerated projects to wrestle control of customer data away from intermediaries in a bid to optimise revenue when demand stabilises.
And in the energy sector, where customer demand and usage patterns are changing rapidly, approaches are being redrawn across the supply chain to squeeze margin from processes already known for their efficiency.
There is a temptation to respond to immediate threats and opportunities by speeding up the deployment of technology. But success in transformation is tied not to the technology but to the design of underlying processes and how they are remodelled. For example, automation might be the solution, but the value comes from determining which processes lend themselves best to automation and how they are broken down into jobs at which machines can consistently excel.
That depends on clear vision. One way to gain a complete picture of the organisation’s processes is to create a digital twin – a virtual model of how processes should happen and how they actually happen. This approach not only explains how the company operationalizes its business model in processes, enabling multiple stakeholders to weigh in on process strategy, but also demonstrates where value is falling through the cracks, enabling test and learn tactics that won’t interrupt production.
The reality is that all businesses have a transformation plan. But sometimes the impetus to change is more immediate than the timeline proposed in a PowerPoint deck. Building virtual process models allows for agility as new issues and opportunities arise, whether that means staffing challenges, supply chain problems or the need to chase a new revenue stream.
The pandemic has interrupted many journeys to Industry 4.0. But successful companies know not to waste a good crisis. Organisations who take a broader, virtual view of the processes that drive their business models are better placed not only for the reactive changes that will keep them in business but also the strategic planning that enables longer-term resilience.
- Schneider Electric's Strategic Human-focused DigitalisationDigital Factory
- Digitalisation as a Strategy to Attract and Retain WorkersDigital Factory
- UPDATED VENUE & DATE – Manufacturing LIVE Chicago 2025Sustainability & ESG
- ABB Cuts Industrial E-Waste in Quest for CircularitySustainability & ESG