Cambridge Consultants revolutionises the production of microcapsules
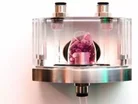
The applied science unit at Cambridge Consultants has created a new way to continuously manufacture microcapsules.
The product design and development firm took a fresh look at the production of microcapsules and re-worked it to create them in real-time, allowing increased flexibility for manufacturers.
Microcapsules, not to be confused with microbeads, are small droplets of material in a protective coating, commonly used in products such as chewing gum, protein powders, and pesticides. They release the right ingredient at the right time, for example bursting when bitten into, or releasing with hot water in the case of freeze-dried food.
Microcapsules are normally manufactured in bulk, meaning the creation of smaller batches are inflexible and uneconomic. Cambridge Consultants has found a way to manipulate the process and make it more efficient.
“This approach allows the continuous monitoring of produced microcapsules and enables real-time control of the process,” said Andrew Strong, Head of Manufacturing Innovation at Cambridge Consultants. “As a result, this can lead to improved controllability, consistency and yield of the finished product – and reduced waste for operators. Similarly, development costs are reduced by removing the need to produce a full batch. This makes it easier for manufacturers to tailor the chemistry to the application – for example, producing biodegradable shells.
“Introducing this flexibility and an element of personalisation into the microcapsule process is a win-win for manufacturers. Essentially, we’ve taken a well-known chemistry method crucial to a huge range of industries and wrapped our own science-led innovation around it to create a more efficient, cost-effective process that delivers over and over again.”