How to roll out a successful lean manufacturing strategy
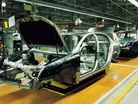
Lean is probably the single most important concept in the manufacturing industry. The principles of lean - minimizing costs, reducing downtime, increasing productivity and eliminating waste – make complete business sense, so its no wonder that manufacturers the world over are keen to improve their lean prowess.
Investment in lean best practice can pay dividends when implemented properly, however it is not uncommon for initiatives to fail owing to poor management and planning.
Manufacturing Global takes a look at how manufacturers can roll out a successful lean strategy:
1. Focus on data
Data and analytics have eliminated the need for guesswork when it comes to rolling out a lean strategy, yet it’s surprising how many companies ignore the facts and focus instead on opinion. Of course the opinion of your people is important, however data shows real results, deficits and accurate information. Armed with this, manufacturing managers can make informed decisions about which areas of the production line need immediate attention, what is working and what needs continued improvement.
2. Encourage group-wide buy-in
From the outset, its important to include everyone in the company’s lean plan and sustain enthusiasm after the initial roll out – after all lean is a journey, not a destination. It is key that management continues to assess, evaluate and promote lean throughout the company, and rewards key players and advocates of the scheme.
3. Give people the tools they need to succeed
When you decide to undertake a lean journey, it is important to build the fence but allow employees to build the house. This can only happen if goals, objectives, expectations, roles, responsibilities and authority are properly assigned and delegated. With this in mind it is also critical that management give those on the ground the freedom they require to make positive changes themselves – a company too heavily government by rules and red tape will stifle innovation and progression. Having an open-door-policy, where employees can make suggestions is also central to success. Companies need to develop a culture of lean, rather than dictate from on high.
4. See mistakes as successes not failures
As we have noted already, lean doesn’t have an end destination; it’s about continuous improvement. As such there is a huge element of trial and improvement. Mistakes are successes as long as you learn from them as a business, rather than repeat them over and over. Help your employees achieve success by pre-identifying some ‘quick wins’ as well as provide opportunities for acceptable failure. With this in place, staff can experience wins and not fear losses or mistakes.
5. Focus on employee training
There is nothing worse than entering a new responsibility without adequate training and development under your belt. Instead, management can allow for basic training at the outset of the lean journey so that all employees understand the goals and ideals behind lean manufacturing. Then, provision of additional, advanced training to key leaders and project participants allows the team to enhance their abilities and to properly evaluate situations beyond just their past experiences.
Identification of either superior trainers within the operation or procurement of an external resource to provide this training is ideal. The training should be widely shared within the organization and not provided to just one individual. The more staff trained in lean best practice, the better the results will be.
- Looking to Japan: Mastering The Art Of LeanProcurement & Supply Chain
- Lean Manufacturing & Data Action with Schneider ElectricLean Manufacturing
- Toyota's Integrated Report 2023: Focus on ManufacturingLean Manufacturing
- The Manufacturing Sustainability Forum: IoT, scopes & moreSustainability & ESG