Intel saves $9b by introducing IoT tech to its backend manufacturing facility
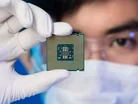
Intel and Mitsubishi Electric are combining next generation factory automation systems with Internet of Things (IoT) technologies in a pilot programme at Intel's backend manufacturing facility in Malaysia.
The pilot programme is intended to demonstrate the benefits of IoT in a factory setting, with a focus on enhancing productivity. According to the company, IoT technology has already saved Intel an astonishing $9 million.
Using the C Controller from Mitsubishi's iQ-Platform, Intel gathered and aggregated data for the analytics server. Data was then processed using Revolution R Enterprise software. The solution is said to have improved equipment component uptime, increased yield and productivity by minimising misclassification of good units as bad, enabled predictive maintenance and reduced component failures.
“The data mining and analytics pilots in Malaysia have demonstrated great value and benefits for Intel manufacturing using IoT products and technology,” said Robin Martin, general manager of Intel's Assembly and Test Group.
Masayuki Yamamoto, Mitsubishi Electric's group senior vice president, Factory Automation Systems, added: “We believe other manufacturers can benefit from this solution, which combines big data analysis, optimised data capture and processing to deliver improved performance and optimised maintenance.”