Inventory Optimisation Produces Operational and Cost Efficiency
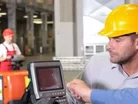
Determining optimal inventory stocking levels should be a strategic, data-driven calculation, however, the unfortunate reality is that many companies do not have accurate data and reporting capabilities to make these calculated decisions.
Too often maintenance professionals are influenced by the fear of stocks outs, while procurement leaders and finance executives strive to minimise on-hand inventory and cost. Two of the most difficult challenges that maintenance and procurement professionals face are maintaining quality data while balancing inventory investment versus production downtime risk.
In a maintenance mindset, the cost of having extra inventory on the shelf is incomparable to the cost that would be incurred if those parts were unavailable during catastrophic equipment failure.
While there are arguments to support this theory, operational excellence requires a strategic balance in which both risk aversion and cost-effective inventory management are satisfied.
It may seem like an overwhelming challenge to tackle at first glance, but there is a solution that can generate immediate cost savings and improved efficiency, while providing many indirect procurement benefits along the way. The answer is Inventory Optimisation.
Based on 24-36 months transactional purchase history and on-hand quantities, inventory data is sorted into OEM and MRO categories.
From there, items are segmented into typical commodity groups, including: Bearing & Power Transmission, Electrical, Instrumentation, Industrial Supplies, Fluid Power, and Pipes, Valves & Fittings.
The next phase of the inventory optimisation process requires inventory to be segmented based on usage.
First, items are categorised as Required-Active, Excess-Active, or Inactive. The Required-Active category represents items, which are frequently used and must be stocked at all times. The Excess-Active category is simply overstock of Required-Active items that must be minimised in an effort to reduce inventory costs.
Finally, the Inactive category is broken down into Critical Spares, Slow-Moving, and Obsolete Materials.
Critical Spares are items, which are essential for the business to operate and stocking out of these parts would significantly impact production, quality, and safety.
The Slow-Moving category represents infrequently used items with long lead times or recommended spare parts which are kept to satisfy risk aversion.
Furthermore, Obsolete Materials are items that are no longer used within the facility and must be disposed of an effort to recover some type of investment dollars.
Since these calculations are data-driven, client input is required to accurately determine inactive categorisation.
Optimsation and rationalisation of the above mentioned categories require a very strategic approach but can return significant cost savings.
Typically we find that Required-Active items range from 25-30 percent, Excess Active items range from 10-20 percent, and Inactive items range from 50-60 percent of all inventories.
Within the inactive category, we consistently find that Critical Spares represent 15-20 percent, Slow-Moving items represent 20-25 percent, and Obsolete items represent 15 percent.
The opportunity for cost savings predominantly comes through the elimination of duplicate items and the rationalisation of Excess-Active and Slow-Moving inventory.
There are a number of disposition strategies that can be used to reduce excess inventory and turn dead stock into cash. Some of those strategies include using down excess inventory through attrition, returning inventory to suppliers for cash or credit towards future purchases, e-commerce (eBay, Amazon, etc.), corporate internal redeployment, and third-party liquidation.
Once inventory has been accurately commoditised and categorised, a comprehensive spend analysis can be performed.
The detailed spend analysis will reveal spend by commodity, spend by supplier, and maverick purchases. Upon review of the results, the procurement department can leverage spend to establish preferred supplier programmes, take advantage of volume rebates, and capture reduced MRO item pricing.
As the inventory optimisation process continues, adjusted MIN/MAX and/or ROP/ROQ levels are recommended based on the analysis of transactional purchase history.
The formula used to calculate accurate MIN/MAX and ROP/ROQ levels must consider many different variables, including: issue quantity, issue frequency, lead time, safety stock, and criticality.
At the same time, a supply chain stock status report can be performed to ensure that all necessary MRO items are stocked at the preferred supplier’s supporting branches. The added reassurance of part availability then allows organisations to further reduce on-hand inventory, while satisfying risk aversion.
The fact is every company has excess inventory, regardless of how robust their enterprise system and purchasing processes may be.
As a result of implementing an Inventory Optimisation and MRO Analysis strategy, companies can uncover millions of dollars in cost savings and improved efficiency, while establishing a solid foundation to effectively manage inventory investment and risk moving forward.