Manufacturers underestimate the impact of proper lubrication, according to Shell
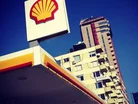
Shell Lubricants has conducted a study which shows manufacturing companies are underestimating the potential cost savings and equipment productivity gains from effective lubrication. Key processes affecting productivity and profitability can be heavily influenced by lubrication, and the manufacturing industry in North America alone could save around $38 million by altering these processes.
Businesses surveyed estimate that 70% of unplanned equipment shut-downs over the last three years were due to incorrect choice or management of lubricants. One in five of these companies estimate incurring costs of over $250,000 as a result of these shut-downs.
- RELATED STORIES:
- It’s time for manufacturers to stop leaving hidden profits on the table
- Think your production line couldn’t get any more productive? Think again
- Why do manufacturers need actionable business strategies?
Yin Jie, Shell Global Sector Manager for General Manufacturing, said: “The impact of lubrication on productivity and maintenance costs is often underestimated.
“At Shell Lubricants, we work together with customers to identify opportunities to help enhance equipment productivity and reduce operating costs by properly looking after the lubrication needs of their machinery. This is not just about selecting the right lubricants, but ensuring they are properly applied and managed. In doing so, we have delivered $139 million in savings to customers worldwide over the last five years.”
The study showed a pervasive lack of understanding about the effectiveness of proper lubrication; more than half (57%) of those asked admitted that they were unclear about how lubrication management can influence unplanned down-time, and 46% didn’t expect lubrication management o influence maintenance costs.
Jie added: “It was surprising to see that only 46% of companies believe product performance should be an important consideration when purchasing lubricants. A high-quality lubricant that keeps equipment clean of deposits and effectively protects against wear can help extend equipment life and reduce frequency of breakdowns. This could help manufacturing companies significantly decrease spend on spare parts and maintenance.”