Syncron think-tank reveals 2018 manufacturing industry predictions
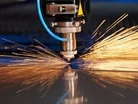
Syncron, a leading provider of cloud-based after-sales service solutions, has published a paper entitled ‘2018 After-sales Service Predictions: Strategies for Empowering Manufacturers to Deliver Game-Changing Value’. The predictions have been compiled with the help of industry thought leaders, who have identified major industry trends for 2018 and beyond, and considered how to implement new business strategies and technologies to improve their service.
“Customers’ rising after-sales service expectations and increased competition for new product sales are driving manufacturers to move beyond the status quo and embark on journeys to transform their after-sales service functions to maximise product uptime,” said Gary Brooks, CMO at Syncron.
“Leading companies are accelerating these service transformations, as parts and service contributes upwards of 15 percent of total revenue (McKinsey & Company) and averages a gross margin of 39 percent (Bain and Co.). To help manufacturers win in 2018 and beyond, we interviewed multiple key industry influencers to gain their perspective on how manufacturers can transform their service businesses to improve the overall financial performance of their companies.”
- RELATED STORIES:
- EEF's research into the UK manufacturing investment increase: An expert comment
- The future disruptors of industry: AR, VR, and cognitive
- Preparing for AI with predictive maintenance
Key predictions for next year include:
1. After-sales service will serve as a significant revenue and profit lever. It will be an increasingly important and strategic focus area for manufacturers worldwide; senior executives recognise the value that exceptional service can bring, in terms of both reputation and financial performance.
2. Service is shifting from a transactional break-fix model to a subscription-based model intended to maximise product uptime. More customers than ever are requiring service level agreements to guarantee product uptime, and it’s increasingly important that downtime is minimised or eliminated.
3. The implementation of emerging technologies and upgraded data management is necessary for future success. The focus on uptime and after-sales service also requires investing in AI, machine learning, IoT, predictive analytics, and other emerging technologies.
4. The organisational structure of the manufacturing workforce is evolving. The key to success in 2018 is remembering the human aspect of applying new technologies and business strategies, in order to retain skilled staff and improve customer experience.
5. Amazon and other disruptors are forcing change. Major ecommerce players are aggressive in the service parts space, and manufacturers need to get ahead of this trend as much as possible, to ensure they remain competitive.
Syncron collected insight from key industry thought leaders, including: Dr. Andreas Baader, Managing Partner, Barkawi; Friedrich Baumann, Executive Advisor to Global Companies; Gary Brooks, CMO, Syncron; Sumair Dutta, Chief Customer Officer, The Service Council; Anders Grudén, CEO, Syncron; Carsten Knudsen, Global Head of Supply Chain Business Improvement, Siemens Gamesa Renewable Energy; Erik Lindholm, Head of Product Strategy, Syncron; Gene Metheny, Partner, Carlisle & Co. and Johan Stakeberg, Head of Global Sales, Syncron.