Why the cycle of feedback and intelligence gathering is critical to servitisation
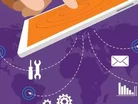
Closing the loop – why the cycle of feedback and intelligence gathering is critical to servitisation
The term 'servitisation' has become one of the most widely discussed among manufacturers over recent years, but for many of these organisations the precise meaning remains unclear. Manufacturing businesses often appreciate the need to move to a more service-based model but they don’t fully comprehend the level of change that this entails.
Servitisation remains a relatively new concept and many companies are in the earliest stages of the journey. Some are under the misguided impression that it is merely about establishing a service contract and putting a service department in place, however siloed and isolated it may be from the rest of the organisation. In fact, the reality is far more complex than that.
The concepts of feedback and closing the loop are critical to the success of the servitisation concept and will continue to be in the future. Manufacturers will need to more effectively track the assets they have sold and that can involve the use of connected devices to help gather intelligent feedback. Equally, in order to drive optimum levels of productivity, they will need to both seamlessly communicate with the whole supply chain and find effective ways to share information with international operations across the entire business.
Moreover, product design will increasingly need to be conducted with service in mind. But to ensure this happens effectively, there also needs to be a better feedback loop to back office operations. Today, even in supposedly sales-led operations, complaints are often handled in isolation in the customer service or sales departments. And yet, this invaluable feedback on what customers like and dislike is never fed back to the quality checkers and product designers and development teams to enable them to adjust their approach.
The kind of connectivity outlined above lies at the very heart of servitisation. It’s effectively the platform upon which it is built. Manufacturers that want to embrace the servitised business model and tap into the benefits it can bring, first need to accept this reality and then start modifying their processes and procedures to accommodate it.
Search for a solution
Having an understanding of the challenge and a determination to tackle it is, however, not sufficient in itself. Manufacturers also need a clear view of the broader context. They need to know what their ultimate goal is - what they are looking to achieve - before they switch to the new model. They need to understand, for example, what markets they want to target, what demand is likely to be and what KPIs are they going to put in place to measure achievement. And they need talented people in post who can read and analyse information coming from the customer and then kick-start the development of new products and services that address this new insight into behaviours and preferences.
Critically too they need to have the right technology in place to join up all the dots and turn servitisation from a vision for their business into a practical reality: to help to effectively close the feedback loop and connect all the separate silos of business intelligence that most businesses have in place today across their enterprise and supply chain infrastructures. That’s where the latest enterprise resource planning (ERP) software can play such a key role.
The great benefit of ERP in this context is its ability to integrate and connect. Not only can it help link different kinds of information – from customers, suppliers and partners, both in real-time and historically to drive decision-making, it can all provide a critical link between all the previously siloed departments within manufacturing, including production, marketing IT and customer service, and use that to deliver operational efficiencies and a better response to customer needs. In other words it can help close the feedback loop and deliver the critical intelligence manufacturers need to make a service-led approach work.
To maximise the benefits of ERP as an enabler for servitisation, manufacturers also need to consider how it can be applied in conjunction with other emerging technologies. The advent of big data technologies has led to a greater emphasis on collecting data and running analytics. Today, the proliferation of connected devices that drives the Internet of Things is growing in significance, serving to extend the potential for organisations to gather information and use it to deliver business benefits.
Information collected from sensors attached to key products could for example subsequently be fed back into ERP systems like Microsoft Dynamics AX. Specific parameters related to product lifecycle management, or service and maintenance, can then be set up, alerting businesses to problems, sometimes before they have happened, and proactively triggering maintenance even before an incident occurs. It’s another great example of a feedback loop in place to drive servitisation success.
Organisations can take this a step further by coupling this kind of information with information from social media or other data sitting in the cloud to achieve both a relationship and technically-focused real-time view of customers, suppliers and stakeholders. This enables the business to make more informed decisions about enhancing innovation and efficiencies, to optimise products for consumption, usage, service and maintenance and to improve the overall customer experience.
When delivered in combination with ERP, this enables, service, production and engineering departments to be brought together on the same platform; effectively closing the loop, delivering servitisation and kick–starting the manufacturing future.
Fabrizio Battaglia is Head of Manufacturing for HSO