LEGO's Renewable Energy Push Doubles Capacity at Key Factory
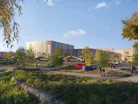
The LEGO Group, a name synonymous with imaginative play for generations, continues to move forward with ambitious plans to reduce its environmental impact.
The latest stride in LEGO’s sustainability journey is the expansion of renewable energy capacity at its Kladno factory, thanks to newly installed solar panels across previously unused rooftop areas and newly constructed buildings.
This is part of LEGO’s broader strategy to reduce the carbon footprint of its manufacturing processes and contribute to global sustainability efforts.
In making these advancements, LEGO joins companies worldwide working to shift their energy reliance from fossil fuels to renewable sources.
LEGO’s expanded solar capacity now more than doubles the previous renewable output at the Kladno facility, which the company says reflects how businesses can successfully reduce carbon emissions through innovative approaches.
Building blocks of sustainability
As corporations globally work to balance environmental responsibility with production, LEGO’s proactive stance highlights what renewable energy can look like in industrial operations.
“Expanding our renewable energy capacity at our factory is a key part of our commitment to minimising the environmental impact of our manufacturing activities and reducing our carbon footprint,” says Michaela T. Horáková, General Manager of the LEGO factory in Kladno.
The newly installed solar panels are set to reduce the factory’s carbon footprint by more than 9% of its total annual electricity use.
This expansion has increased the total renewable energy generated at the factory from 1 MW peak (MWp) to 2.5 MWp, enough to power roughly 400 homes annually. Covering around 11,000 square metres, the solar panels make use of previously underutilised rooftop areas and offer a concrete example of the company’s forward-thinking energy strategy.
Michaela adds: “The newly installed solar panels are projected to reduce the factory’s overall carbon footprint by more than 9% of its total annual electricity consumption in the coming years.”
Global commitment to sustainable manufacturing
LEGO’s sustainability goals extend far beyond its Kladno factory. The company has invested in expanding solar capacity across other global manufacturing sites, including Denmark, Hungary, Mexico, China and other locations.
In 2023, LEGO’s maximum solar capacity across these sites reached 15.6 MWp, marking a 16% increase from 2022.
But LEGO’s commitment to renewable energy doesn’t end with its current factories. Plans for future manufacturing facilities include incorporating sustainable energy sources from the start.
In Vietnam, a new factory with on-site solar capabilities is expected to be operational by 2025 and another in Richmond, Virginia, aims to open by 2027. Both will aim to include both on-site and off-site solar resources with the goal of meeting each factory’s total annual energy needs.
In Billund, Denmark, LEGO plans to build a solar park to meet the energy demands of its facilities and offices throughout the city, which remains a symbolic location as the birthplace of the iconic brand more than 90 years ago.
Innovations in sustainable brick production
LEGO’s renewable energy goals also align with its commitment to making its products more environmentally friendly.
Aiming to replace oil-based plastics with renewable and recycled materials by 2032, the company has tested over 600 material alternatives to meet quality and safety standards.
Innovations include arMABS, a new material made from recycled artificial marble and ePOM, which incorporates renewable energy and CO₂ sourced from bio-waste.
Chief Executive Officer Niels B. Christiansen acknowledges that the company’s dedication to sustainable materials does come with added expenses: “This means a significant increase in the cost of producing a LEGO brick.
"However, with a family owner committed to sustainability, it’s a privilege that we can pay extra for the raw materials without having to charge customers extra.”
Beyond sourcing materials, LEGO is investing heavily in environmental projects, aiming to double its spending in this area by 2025. Central to this mission is ensuring that LEGO bricks last for generations, thereby reducing plastic waste.
The company also promotes initiatives like brick takeback programmes, where fans are encouraged to keep bricks in circulation or repurpose them through LEGO’s recycling initiatives.
“By designing bricks that last for generations, we aim to inspire endless creativity and stop LEGO bricks from becoming waste,” adds Annette Stube, LEGO’s Chief Sustainability Officer.
“And alongside encouraging fans to keep bricks in play, we are continuing to explore more ways to repurpose LEGO bricks through our takeback initiatives.”
Through these efforts, LEGO not only hopes to transform its energy use but also set a model for sustainable production practices across the industry.
As a leader in renewable energy adoption within manufacturing, LEGO continues to demonstrate how industry and environmental responsibility can go hand in hand.
Make sure you check out the latest edition of Manufacturing Digital and also sign up to our global conference series - Manufacturing & Mobility LIVE
Manufacturing Digital is a BizClik brand.
- Panasonic Opens First European Demo Renewable Power FacilitySustainability & ESG
- Hitachi Energy: Investing In US Clean Energy ManufacturingSustainability & ESG
- Kent's Bold Bid to Expand US Manufacturing PresenceProduction & Operations
- Nike & LEGO Group Partner To Manufacture Co-Branded ProductsProduction & Operations