3D printing promises to live long and prosper
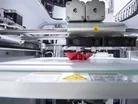
'Taste tomorrow today' read the strapline of what was arguably the hippest of hipster restaurants in London’s Shoreditch this summer. Food Ink popped-up temporarily in July and invited people to enjoy the 'most futuristic dining experience in the known universe' - a bold claim that helped to conjure up images of the Star Trek Enterprise’s replicator, and a world where culinary desires could be reproduced at the touch of a button.
The people behind Food Ink are not the first to seize upon the potential of 3D printed cuisine. Last year Italian food company Barilla and the Netherlands Organisation for Applied Scientific Research (TNO) teamed up to produce 3D printed pasta shells, while US confectioner Hershey’s has been showcasing the technology to print up chocolate treats.
While 3D printed food might not whet everyone’s appetite, the technology is having a significant impact across a number of industries, and not just for perfectly parallel foodstuffs. It is also being used in manufacturing to increase efficiencies across the full product development chain.
Revenues for computer-aided design software are forecast to triple between 2015 and 2020 according to industry analyst IDC, while worldwide spending on 3D printing is expected to surpass $35 Billion in 2020. Furthermore, analyst forecasts such as these are backed up with acquisition activity in the real world, when GE spends $1.4 billion to gain a place at the 3D printing table everyone should sit up and takes notice.
3D printing prototypes
3D printing is clearly more than a gimmick that marketing executives at food companies are using. The gains in both software and on-demand parts printing are being driven by the rapidly expanding use of 3D printing for design prototyping and products that require a high degree of customisation in non-traditional environments.
Before any new product is brought to market, it is essential that accurate, production representative prototypes are available as quickly as possible for trials and testing. Whether you are a luxury automotive manufacturer like Bentley which is using 3D printing to build scale models of new cars or a 15-year old entrepreneur using 3D printing to breathe life into a dream football boot cleaning concept, the process is made quicker, more affordable and more accurate through digitally designed and automated processing.
3D printing in production
Once past the prototype stage we move onto production, and this is where 3D printing really comes into its own. A vast area of exploitation for 3D printing exists in high volume discrete manufacturing where the technology can deliver unprecedented levels of precision and efficiency. Furthermore, in industries such as life sciences, where micro tech development and material durability are crucial to product success, 3D printing provides an improving range of intricacy and material options that produce highly effective medical devices. For this reason, life sciences is the number two growth market for the technology over the next five years (IDC). And it’s not just medical device manufacturing that is benefitting from the technology, it is not beyond the realm of possibilities that 3D printing will soon be used to mass produce replacement body parts, cartilage and even blood cells.
The whole package
The final part of the manufacturing process where we see 3D printing have an impact is packaging. A notable recent example of a firm benefitting from the revolution of 3D printed packaging is Kodak which secured a substantial return from its Micro 3D Printing and Packaging Division (MPPD) in the last quarter. The former giant of photo printing raised $35 million revenue, a $2 million increase from the same period last year, from MPPD. This figure is surely set to keep on rising if IDC’s forecasts hold true.
Additive manufacturing struggles to compete with conventional manufacturing methods when production levels go beyond 40-100 units, but 3D printing is still hugely useful in the development and testing of packaging. When using the technology, manufacturers are able to improve package durability and shape and respond quickly to defects, which is particularly useful for those developing contained products, such as paints and chemicals manufacturers.
An efficient resource
In all, 3D printing is having a significant impact on almost the entire spectrum of manufacturing processes, and as our customers seek to gain greater control of their factors of production, we expect them to consider this technology as a go-to for many of these processes. With its materials inherently measured and moderated, 3D printing can make resource planning easier and more efficient for organisations of all sizes.
With the market predicted to reach $35.4 billion by 2020, we expect businesses to consider implementation throughout the development chain over the next few years, and to integrate 3D printing more and more into their conventional IT processes as accuracy and material options continue to improve.
We may be a way off using the technology to replicate food on a daily basis, but as 3D printing methods evolve, it is sure to be on the menu for production companies across a range of industries in the years to come.
Chris Littley is Senior Pre-Sales Consultant at IFS