Airbus saves 15% in material weight due to 3D printing
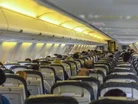
The European aircraft manufacturer, Airbus, has been working with Materialise’s Certified Additive Manufacturing for two, creating plastic parts for aircrafts through 3D printing.
The two firms began working on parts for Airbus’ A350 XWB model, but since the have moved on the new programs and services.
The manufacturer has noted the benefits of 3D printing for small batch production, enabling more customisation whilst being time and cost effective.
Trough additive manufacturing, Airbus has reduced its time-to-market for customised parts from conventional manufacturing using tool-production.
On 11 April, the two companies started producing the first 3D-printed parts for commercial aircrafts that will be visible to passengers – spacer panels for overhead storage compartments.
SEE ALSO:
-
Boeing signs deal with TAL to manufacturer beams for Dreamliners
-
North Wales Advanced Manufacturing and Research Institute receives planning permission
- Read the latest issue of Manufacturing Global here
The parts mark Airbus’ first bionic design certification, following the firm’s bid to optimise part weight.
The 3D-printed panels are 15% lighter than the company’s previous manufactured cabin panels, as well less complex to produce through the alternative method.
“We can handle incredibly tight lead times, but the foundations for that lie in a carefully honed quality management system,” stated Geert Appeltans, Quality Manager at Materialise.
“The spacer panels produced for Airbus are more than 3D prints, they’re the output of an entire quality system.”
“Our goal at Materialise is to be a trusted and reliable supplier in additive manufacturing to Airbus,” stated Edouard de Mahieu, Project Manager at Materialise.
We do this by innovating together in design and production processes with our software and know-how of AM, but also by seamlessly integrating Airbus’s own way of working.”