Best practice for big data management: Value through visualisation
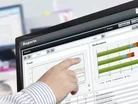
Big data is one of the most talked-about technology trends of the past decade. However, the catalyst for big data occurred in the 1960s. A 1967 paper by B.A Marron discussed the growing amount of data that the world was producing – referred to as the ‘information explosion’. In the paper, Marron imagined the potential of an automatic processor that could collect and store valuable pieces of information for its users – technology that we now experience in almost every part of our lives.
Here, Lee Sullivan, Regional Manager at industrial software expert, COPA-DATA UK, explains the value of big data in the manufacturing industry and the best practice for industrial data acquisition and visualisation.
Data defined
With an increasing amount of data being generated every day, businesses are keen to reap the rewards of its insights. Much of the hype surrounding big data is driven by the potential to gain actionable knowledge that can improve factory productivity, reduce production costs or minimise waste. However, before businesses can reap the rewards of this information, they need to decide on the best method to collect data.
Data acquisition
Most modern manufacturers are familiar with the role of supervisory control and data acquisition (SCADA) software in a manufacturing facility. However, not all manufacturers understand how SCADA systems can assist in managing big data. Unlike traditional SCADA, modern applications are adopting technologies to prepare manufacturers for the era of Industry 4.0. By incorporating Internet of Things (IoT) technologies, such as cloud storage and predictive analytics, modern SCADA software can manage much more complicated datasets than traditional systems.
What’s more, we are now seeing an increase in independent SCADA software solutions – platforms that are not designed or created specifically for use with one type of hardware. The benefits of intelligent SCADA software cannot be experienced simply by collecting production data, but applying that data by implementing real changes to the factory floor, according to this new-found insight.
Game-changing results
Acquiring data is a start, but big data is bound to lose its value if the information is left to gather dust.
Using an intelligent software platform, companies can deliver and visualise data in real time, meaning that business decisions can be made quickly. For example, SCADA can deliver real-time insight into the functionality of equipment in a manufacturing facility. When a machine is showing signs of breakage or failure, the sensors of that machine can automatically inform the operator. This allows the operator to take proactive action to avoid these equipment failures, reducing downtime and unexpected stoppages.
However, it is not just real-time data that can provide valuable knowledge. A comprehensive SCADA system will also consider historical data when reporting production data. By integrating the results of real-time production and historical information, some SCADA applications will provide predictive analytics – an insight into the future of production. This feature has undeniable value for all manufacturers, but for machine builders, it can provide an entirely new service to sell in the form of preventative maintenance.
The value of data is not in the data itself, but the way in which business leaders analyse and utilise this data to help achieve their business goals. The ever-growing expanse of information gathered from a smart factory simply cannot be managed manually. However, if manufacturers are going to reap the rewards of big data, they must invest in platforms that can provide an intelligent insight at machine level. In preparation for Industry 4.0, modern SCADA systems should not be limited to data acquisition. Today, intelligent SCADA platforms must be capable of communicating the results of data acquisition visually, in a clear and concise manner.
The speed at which we produce data has been noted as a global challenge by academics and industry leaders since the 1960s. Today, we have the technology to manage data in a way that not only stores vital information, but provides businesses with intelligent decision-making tools. The data deluge doesn’t appear to be slowing down and as a result, it’s essential for manufacturers to invest in data acquisition and visualisation.