BMW Group: AI innovation in the automotive industry
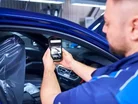
Manufacturing Global sat down with BMW Group’s Head of Artificial Intelligence Innovation, Matthias Schindler, at the Connected Manufacturing Leaders Summit in Berlin.
At BMW Group, artificial intelligence (AI) plays an important role in leveraging insights from smart data analytics. Head of Artificial Intelligence Innovation, Matthias Schindler leads these efforts across BMW’s production system at 31 sites in 15 countries all over the world. “We are focused on object detection to improve quality. We’re aiming to reduce rework, accelerate systems and improve our production processes. In general, we only focus on production, so not the car or product development itself, but all facets of production, including all the technology - starting from press shop, through the body shop and paint shop, to the final assembly, and all the support functions along that production journey.”
Optimising Quality
Schindler explains that improving quality inspection has several strands across the production process. “We want to make it all more robust,” he says. “The automated inspections we have implemented so far allow us to check the configuration of the car is correct as far as the customer order is concerned. We have one billion possibilities to configure with the new BMW 3 Series. So that means the correct rims, seat, flooring and so on. In the past, we had automated inspections which were mainly scale and pixel-based comparisons. Object detection with AI has helped us to optimise this process.”
In these processes, AI evaluates component images in ongoing production and compares them in milliseconds to hundreds of other images of the same sequence. This way, the AI application determines deviations from the standard in real time and, for example, checks whether all required parts have been mounted in the right place.
Schindler points out that the increasing multitude of manual inspection tasks needed a solution to stop the error rate increasing and to allow employees to spend more time on creative work. “We spoke with our foremen and asked how we could create more time to directly support our employees instead of only controlling visual inspection,” says Schindler, explaining the genesis of his team’s approach. The old system relied on a laborious database process which wasn’t effective and was ultimately hampered by the cost of hardware, including industrial standard cameras. “However, these were not needed with respect to AI,” adds Schindler.
Machine Learning in the Press Shop
BMW Group’s home plant in Munich features a press shop which turns over 30,000 blank sheets of metal into vehicle body parts each day. Since 2019, at the start of production each blank is given a laser code so the resulting body part can be identified throughout production. This code is picked up by the iQ Press system, which records material and process parameters – such as the temperature and speed of the presses and the thickness of the metal and oil layer. The parameters are then related to the quality of the parts produced.
Schindler explains that in the press shop they are making use of deep learning and AI to check for micro tears and oil and metal stains. “We’ve categorised six single features using conventional greyscale-based image processing,” explains Schindler. “This has enabled us to have a 100% robot system which picks out only irregularities that require action.”
Predictive Maintenance in the Body Shop
“With the help of retro-fitted sensor kits we have been able to bring our equipment into the 21st century,” says Schindler. Body shop robots are fitted with a combined total of over 600 welding tongs. It’s costly and time consuming if the tongs ever need replacing unexpectedly, as many of the robots are difficult to access so dismantling and replacing their tongs can take hours. Maintenance specialists at the Munich plant have now fitted sensors to all the tongs to measure friction levels three times per shift and report any abnormalities. Potential machine failures are predicted by the constant evaluation of the data produced. “Because we have the sensors and collect their data in a cloud, we can now monitor round-the-clock whether any maintenance work is needed,” explains Martin Hilt, Innovation and Digitalisation Officer at the Munich plant. “So, we can plan any replacements better and potentially schedule them for a production break.”
Sensors in the Paint Shop
Schindler believes using data analytics to focus on quality is vital to avoid costly rework. Vehicle bodies can pick up dust particles as they make their way to the paint line, affecting the quality of the finish. Previously, potential defects had gone undiscovered but now every paint shop system incorporates sensors that measure dust particle levels and allow the quality of paintwork to be predicted. “We’re now collecting data from more than 1,000 single process parameters from the pressure inside the painting process to temperature changes and humidity levels,” reveals Schindler. A further special sensor developed at the Munich plant has been measuring dust levels on body parts at the beginning of the painting process, before and after the emu feather rollers. When dust levels are too high in the future, car bodies will pass through the paint shop untreated and be sent for further cleansing.
AI-based Image Recognition in Assembly
The algorithms used are relatively expensive to develop, but AI-based applications are gradually replacing permanently installed camera portals. Implementation is straightforward. A standard mobile camera is all that is required to take the relevant pictures during production. The AI solution can be set up quickly too. Employees take pictures of the component from different angles and mark potential deviations on the images. This way, they create an image database in order to build a neural network, which can later evaluate the images without human intervention.
Schindler explains that employees do not have to write code; the algorithm does that virtually on its own. At the training stage, a high-performance server calculates the neural network from around 100 images, and the network immediately starts optimising. After a test run and some adjustments, the reliability reaches 100%. The learning process is completed and the neural network can now determine on its own whether or not a component meets the specifications. “The artificial neural networks are the focal point to enable this high robustness of quality inspection and the flexibility of the applications themselves,” confirms Schindler.
BMW Innovation Lab
“We develop many parts of the algorithms we use by ourselves,” explains Schindler. “The BMW Innovation Lab is crucial for our success because they have students starting internships, studying for a Master's thesis or even a Doctoral thesis, who are experts in deep learning and AI. They are capable of writing code in a manner that can be reused. It’s an important collaboration for us.”
BMW is also sharing its network architecture code on GitHub to encourage further collaboration across the automotive industry with other companies also exploring AI. “We want to encourage them to bring on their algorithms, which could be APIs for some other framework, for example. We want to accelerate the open innovation process and share it with the entire world,” says Schindler. “There are many scientific and practical challenges being addressed here with new results every second week. Everything is available on a public basis, more or less for free. This was one of the reasons why we wanted to give something back.”
SEE ALSO:
Training for the Future
Schindler’s background in mechanical engineering, IT consultancy, and writing software for manufacturing, alongside experience with 3D digitalisation in previous production roles, gives him a deep understanding of the needs of all areas of BMW Group’s automotive plants. He believes understanding “both worlds” is key to the company’s continued success and is keen to broaden training for workers who are now seeing the benefits that semi-automated processes and AI can bring. “They must know that AI is not a magic box to solve every problem,” he warns. “We have to have a very dedicated process and make the effort in this introductory phase. One of our main targets for this year is to really educate the managers in a way that they know what they can expect from AI and how it can help them in the future. We want to demystify the AI process - it’s not like a Terminator movie - training will be important for the next 10 years and more. There is no free lunch, you have to invest time to achieve the benefits. And that’s a journey we are happy to be on at BMW Group.”