Hot crimping delivers cost-effective, efficient joining of enameled copper wiring
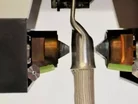
Following on from the news that Amada Miyachi Europe has announced a new welding system, Robert Vermeulen explains the process in greater detail.
Manufacturing electromotors for a wide range of applications, including automotive, offshore power generation, generators, pumps, and more, require that insulated copper wire be joined together and welded to terminals. There are a variety of processes in place to achieve this goal, but none are as efficient, effective, or low-cost as hot crimping. Though hot crimping has been used for many years, it has seen a surge in popularity in recent years, both due to its benefits over other joining methods and due to the trend of electrification in the automotive market. Modern hot crimping technology efficiently produces high-quality joins that are effectively sealed from the environment, and are therefore more durable than those produced by other joining methods.
Costly, time consuming joining methods slow production
In most circumstances, copper wires can be welded directly to the desired terminal with laser or resistance welding; however, when the wire is electrically isolated with an enamel coating, the isolation prevents the making of a connection. That coating must be removed before the wire can be welded to the terminal, regardless of the welding method. Multiple wires that must be joined to a terminal together present an even more difficult situation, in that they must be stripped and crimped together before being welded.
Several different methods exist for removing the isolation on this copper wiring and the subsequent joining: namely, the enameled coating is stripped with a laser or a mechanical brush, and then the wire is welded to the terminal with resistance or laser welding technology, or is cold crimped into a cable shoe which is then attached to the terminal. Both laser and mechanical removal of the wire’s enamel coating involve a great deal of work during the manufacturing process, are time consuming, and are expensive.
In addition, space constraints on the manufacturing process can make it difficult to fit laser or mechanical wire stripping devices onto wire coils. The welding methods can require more space than is available as well, making it difficult to create a reliable join. Finally, cold crimping can lead to joins that are somewhat unreliable, particularly in sealing the wires from the environment.
Hot crimping reduces costs and delivers quality joins
Hot crimping provides electromotor manufacturers with an alternative solution to joining techniques that require the enamel coating on copper wiring be removed with lasers or mechanical means. In hot crimping, the enamel removal and crimping take place in immediate succession and within the same process, making the overall join faster and more cost-effective.
The basic process of hot crimping consists of placing a conductive metal sleeve, hook, fork, or other shaped object around the copper wire or wires that are to be joined. The sleeve or other metal object is then placed between the two electrodes of a resistance welding system. A large amount of current is passed through the sleeve, causing it to heat to approximately 500˚C. This temperature is adequate to burn away the enamel and allow it to gas out of the metal sleeve. Once the enamel coating has burned away, even more heat is applied to the sleeve via electrical current, which causes the metal sleeve to collapse and tightly compress the stripped copper wires. Once the compressed ring cools down, there is a strong mechanical and electrical connection between the individual wires and to the metal ring. The metal ring, which is often part of a cable shoe, can then easily be joined or directly connected to a terminal.
Hot crimping creates an excellent mechanical and electrical connection, particularly when more than one wire is being joined together, due to the compression of the heat-collapsed metal on the wires. This connection effectively seals the join from the environment, unlike in cold crimping, which can be critical in corrosive environments. Additionally, the hot crimping process is far more efficient in terms of cost, time, and effort than other wire stripping and joining processes.
Modern use and cutting-edge hot crimping technology
Though the hot crimping process has been used for many years, it has seen a recent surge in use due to the increased electrification in vehicle design. It is used, for example, in the production of heated seats for cars. Given that a great deal of mechanical stress is out on the heating elements in this application, the danger of them breaking is high. The heating elements in heated seat design are often a high number of very thin, isolated copper wires. Hot crimping makes it easier to join the wires to one another and to the terminals with a strong mechanical connection that will withstand the stress placed on them during use.
Hot crimping has also seen increased use due to a rise in demand for offshore power generation equipment. In these applications, it is critically important that wires in and leading to the motor be sealed from the environment, because the salt air is extremely corrosive and, if it can permeate the connection, will damage it over time. Unlike with cold crimping, which cannot achieve the same mechanical force, the compression of the metal sleeve in hot crimping is strong enough to exclude corrosive gas like salt air.
There is a wide range of hot crimping technology available today from leading resistance welding technology manufacturers, such as Amada Miyachi. The hot crimping technology must be designed to provide the proper amount of energy for the application at hand. For instance, equipment designed to hot crimp wiring for offshore power generation, which can reach up to 200-300 mm2 in diameter, requires a great deal of power in order to generate the high forces needed to compress such large wires. That same equipment, however, would prove destructive to the wiring used in automotive heated seats, as it would be strong and hot enough to melt the wires themselves or to mechanically damage them.
Amada Miyachi Europe offers a full range of resistance welding technology to be used in hot crimping, ranging from the highly delicate, fine control required to hot crimp wires as small as 40 µm to the high power and high force (up to 20.000 amps and 10.000 N) required for very large wires. Additionally, the company offers cutting-edge process control that allows manufacturers to both program their precise desired end result (in terms of power, heat, or distance of collapse) and to check the end result to be sure that it conforms to those standards. These capabilities to monitor the hot crimping process and provide feedback to quality engineers is critical in a number of applications, but especially in automotive manufacturing where traceability is particularly important.
With this kind of cutting-edge hot crimping technology, electromotor manufacturers can reduce costs, time, and space required by laser or mechanical wire stripping devices. At the same time, manufacturers can precisely control and verify their end results, ensuring high-quality joins that provide good electrical and mechanical connections, and are effectively sealed from them environment. Hot crimping technology is on the rise, and will likely continue to gain in popularity as electrification in automotive manufacturing and offshore power generation continue to increase in prevalence.
By Robert Vermeulen is Product & System Sales Manager, Resistance Welding at Amada Miyachi Europe