How ERP can make good on the promise of real-time actionable intelligence
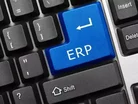
Mobile, social, analytics, cloud, the Internet of Things, nanotechnology, 3D printing and more - manufacturers are facing a barrage of information about how new disruptive technologies will change the face of their industry. But for manufacturers to embrace these technologies, they must have a clear understanding of the technology value-add within the context of today’s business environment – what I like to call 'purposeful innovation'.
Big data and the IoT as technology concepts are exciting, but what do they mean to manufacturers from a practical application perspective? As digitization becomes defacto on the manufacturing floor, there is great potential to improve responsiveness and agility, and adapt more quickly to customers’ changing needs. As more digitally controlled technologies are introduced, we build more connections. As we become more connected, building the IoT, we generate big data. And as the volume of data grows, we need new and faster ways to drive insight and actions, and easier ways to arrive at decisions.
So while these disruptive technologies are expected to improve responsiveness, they create new challenges in managing an increasingly overwhelming volume of data that must be converted into actionable intelligence. Manufacturers can’t afford to allow these technologies to inadvertently slow them down, as this would be contrary to the aforementioned goal.
When it comes to the IoT, it’s not about the data perse, it’s about what you can do with that data. As Industry Analyst Nigel Fenwick at Forrester Research has said: “It's important to note that digital isn't just about gathering new external connections; it's about having the operational agility to act on them.”
Some of the manufacturing purists may argue that IoT isn’t new to them – after all, machines have had sensors for a long time reporting back information to the user – like the ubiquitous laser jet printer that tells you exactly how much ink is left and even where to order replacement cartridges. However, what’s new is we now have the technology capabilities to enable the integration of information across the entire product lifecycle – from design, through engineering, manufacturing, delivery, and service — to deliver immediate and actionable information to the necessary departments and functions with greater speed, accuracy, and efficiency than ever before. Imagine the new printer that prints your production schedule at the beginning of the shift when it detects you have arrived on the shop floor and automatically emails you a PDF of that schedule?
This is about gaining instant access to information “in context” to the task or decision at hand. The value-add is aggregating data quickly to make meaningful decisions today that manufacturers couldn’t make yesterday. What’s 'new' and notable with the IoT is this ability to aggregate data, analyze it and even use it for predictive modelling.
With all this talk about the IoT, manufacturers may wonder – where does ERP fit into all of this new digital frontier? The reality is ERP is more relevant in this equation than ever before – as it’s the key to unlocking the value of IoT. To be able to realize the full value-add of big data/IoT initiatives, manufacturers need the ability to contextualize data and integrate it into downstream process flows. This is what ERP has always done, however today next-generation ERP platforms are more approachable and more powerful than ever – functioning as the fabric that connects people, processes, data and things in an intelligent and strategic manner that allows manufacturers to create value from new data streams.
To do this however, ERP systems must be reimagined to meet the needs of new and emerging technologies in the business of manufacturing. Responsiveness demands simplicity and mobility with tools designed to meet the specific needs of specific users. It demands new levels of collaboration throughout the supply chain, inside and outside the enterprise. It demands choice in the way information is presented, applications are accessed, and solutions are deployed. With an ERP system that delivers all this and more, manufacturers can check off a big box on their IoT readiness checklist and make good on the promise of real-time actionable intelligence.
By Sabby Gill, Executive Vice President, Epicor Software International