Infosys Consulting: 5G driving smart connected factories
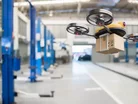
Rafi Billurcu, Partner, Manufacturing at Infosys Consulting, discusses the evolution of smart connected factories with the use of 5G.
The manufacturing industry is at the forefront of digital transformation, driving and inventing various new business models from Industry 4.0, smart manufacturing, and AI, to AR and VR, 3D printing, and connected and autonomous cars.
However, the industry is still far from reaping the full benefits of disruptive technologies and digital. That’s because there’s one vital part of the jigsaw missing: connectivity. The capabilities that new technologies will confer on tomorrow’s factories depend on ultra-reliable, low latency communications between machines, sensors, databases and workers’ mobile devices.
While the 4G revolution mostly benefited consumers, it was not enough of a leap forward in connectivity to enable the services on which tomorrow’s factories will rely. That’s about to change with the advent of 5G. Forget about downloading high definition movies in seconds – instead, manufacturers should know how the next generation of mobile communications will transform their operations, leading to greater efficiencies, enhanced quality, and more innovative products.
Smarter manufacturing
There are few more complex environments on earth than a modern factory. From complicated production lines with thousands of moving parts to the supply chains that bring in raw materials and components and send out the finished products, factories generate masses of data every second of every day.
This information is absolutely key to successful operations: it ensures that manufacturers have comprehensive and up-to-the-minute insights on everything from machinery performance to safety-critical systems to manufacturing quality. But consider how much data a modern manufacturer generates from all the sensors embedded in its machines and you’ll realise how 4G is completely inadequate for the needs of a smart, fully-connected factory.
Machine-to-machine (M2M) and machine-to-human communications are especially crucial as we approach an era where mass customisation replaces mass production. This new model of production depends on combining huge volumes of data from multiple sources so that manufacturers can undertake predictive maintenance, manage their supply chains most efficiently, and respond quickly to outside influences such as changing order patterns.
SEE ALSO:
What unites all these disparate functions is that they will need to minimise, as far as possible, the time between insight and action. In the case of automation – a fundamental building block of smart manufacturing – these communications often need to happen within a fraction of a second. This isn’t just a case of sending instructions to machines: automated systems should be providing a constant stream of intelligence on operations that can improve performance.
Tellingly, though, many of the 1.7 million industrial robots are not connected to the Internet at all, making it impossible for them to share the insight that they could be gathering. The same principle applies to every other connected device within the factory environment, where it is sensors within the production line, safety-critical systems or even workers’ tablet devices. Given the huge amounts of data involved and the imperative of instantaneous data transfer, only 5G can provide the speed and bandwidth necessary.
Laying the foundations
Within a factory, 5G will support better connectivity between machines and help make real-time decisions within a fraction of a second. During the quality inspection process, for example, machines will be more reliable and accurate in checking the quality of the manufactured product, and predictive maintenance can be triggered automatically before a machine failure happens, to reduce unplanned downtime.
What’s more, 5G will play a pivotal role in what’s been termed the “Internet of Skills” – the ability for any human to teach, learn or execute actions remotely. The ability to share knowledge and skills is an overlooked aspect of Industry 4.0, yet it’s one that’s just as important as automation or connected devices. When workers can access the sum total of all information within the business, from real-time insight into machinery performance to educational and training resources.
By making mobile communications instantaneous, 5G will enable factories to become more efficient, safer, and will make it easier for humans to collaboratively work with machines. It will deliver benefits ranging from real-time analysis of traffic data to improve transportation routes in the supply chain, to real-time visibility of inventory and shelf life to suggest which items to order and when – and even automatically trigger orders. It will also be key as manufacturers move from merely making items to delivering a range of value-added services (or “servitisation”), which heavily relies on data analytics and other high-performance systems.
From big data analytics to connected devices, 5G will be the key building block to next-generation factories, providing the ultra-reliable low latency connectivity on which Industry 4.0 depends. Thanks to the speed and reliability of network provided by 5G, manufacturers will be able to move closer to their vision of smart factory, realising the full potential of disruptive technologies and digital.
For more information on manufacturing topics - please take a look at the latest edition of Manufacturing Global.