Joining up IT investments can help manufacturing leaders unlock the productivity puzzle
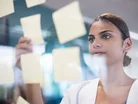
If economist Paul Krugman is right, and productivity is “almost everything”, then Britain is facing a serious problem: The latest productivity figures showed that a decade of underperformance has left the UK trailing its rivals. And the manufacturing industry is among those in the limelight for failing to capitalise on technological advances.
Many companies have been left mystified, as significant investments in technology have failed to deliver the expected productivity gains: the underlying cause could be that a layer of connectivity is missing, along with the understanding of how a truly digital business can operate. With a combination of targeted digital investment and cultural change, Britain's manufacturers can lead the country in turning the corner on productivity.
Productivity figures show a gap of 16% between the UK and the other G7 nations. Compared to their counterparts in the US, France and Germany, UK workers fare even worse, producing roughly 20 percent less for every hour worked. However, Britain isn't the only country blighted by falling productivity since the financial crisis. Firms across the world are struggling to raise enough funds for investment and many manufacturers are also being hampered by a skills gap.
But perhaps the biggest issue is what economists have dubbed the 'productivity puzzle' – as technology advances, each new turning point in productivity has failed to materialise. If this underperformance from technology can be addressed, a manufacturer can boost its production and improve margins by taking advantage of IT that is already in place, but remains chronically underutilised.
Bank of England Chief Economist, Andrew Haldane, recently weighed in to the productivity debate with the observation that many UK businesses are complacent and have an inflated view of their own performance. A view held by some as a nation 'David Brents' - the useless manager in the sitcom The Office – will seem harsh to many in the manufacturing sector, who will point to rich examples of championing innovative ideas, products and firms.
Yet there may be some truth in Haldane's assertion that bad management alone accounts for a quarter of Britain's productivity gap. However, much of the problem with management may not be due to poor skills, rather a lack of suitable infrastructure and communication channels. A major source of wasted time and inefficient decision-making is the fact that leaders and managers often simply don't have the latest information to hand. The same problem also runs the other way, with individual departments rendered ineffective because they are not aware of changes within the business, the supply chain and, crucially, the customer base.
The digitally interconnected world provides the means for manufacturers to rapidly react to changing demands and build highly-efficient supply and production systems. However, for these lines to be effective, managers must be able to react quickly to production level issues, rooting out bottlenecks and addressing problems that have an impact on production. At the same time, designers need to be constantly aware of changing sales trends, and be able to implement changes rapidly, to reflect improved methods or product changes that reflect a shift in demand.
Cultural change alone cannot achieve this: an advanced digital strategy is needed to allow the levels of information sharing that even a relatively small manufacturer will require. Fortunately, most companies have already invested in IT systems, albeit on a piecemeal basis, designed to meet specific challenges at departmental levels. The next stage is to create a integrated enterprise-wide strategy and digital infrastructure so that outdated ways of working can finally be left behind across entire organisations.
This need not be a costly or disruptive investment: enterprise information platforms can be implemented within short timescales and without hampering operations, thereby creating an enterprise level information hub. This can then be tailored by management and key users, without the need for specialist IT skills. Importantly, the hub must be capable of handling all the data formats being used across an organisation: from the factory-floor and production line, to its customer-facing websites or supply chain communications.
By implementing a suitably flexible system, the resource can be adapted in a ground-up approach, as new ideas emerge as solutions to problems, and further technologies are incorporated into the manufacturing or design processes.
Such a system will not only improve the utility of production-level technologies, by providing up-to-date insight, but will allow management to identify the 'pain points' holding back production: the areas where human actions are hampering the flow of data and smooth running of technology. Spotting such challenges will be critically important in the second phase of implementing the new system.
At this point, managers need to look out for IT silos – shadow systems created within a department that are not linked in to the wider system and typically indicate an area of poor productivity. The widespread use of paper documentation is an even bigger give-away: in a sector where technology and data flows are crucial to competitiveness, staff who are still jotting down ideas, or even worse keeping them in their own head, are sadly counter-productive.
Instead, the entire workforce needs to be linked by an enterprise-wide information strategy that can tie new IT applications seamlessly with existing line-of-business systems. Making all information securely accessible to those who need it, while seamlessly linking all formats, will act a catalyst for the technology infrastructure already in place. This enterprise information platform will become the foundation on which further systems can be added, as technology and the business operations progress. By enabling change without costly disruption, this layer of IT not only boosts productivity but also provides the flexibility required to future-proof the business.
Paul Krugman's quote that “productivity isn’t everything, but in the long run it is almost everything” is self-evident at a business level: what manufacturing leader isn't striving to improve its organisation's efficiency? However, in order for people across an organisation to envision what is possible with innovative technology, communication and inter-operability needs to be vastly improved. This may be the final piece of the jigsaw to unlock the productivity puzzle.
Tim Rushent is account manager, industry and commerce, with www.hyland.com