MIT, Stratasys, and Autodesk Experiment With 4D Printing
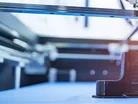
‘Our structures, which have remained static and rigid, will soon be dynamic, adaptable, and tunable for on-demand performance’, says Skylar Tibbits, The Self-Assembly Lab, MIT. In collaboration with Stratasys and Autodesk, the lab is exploring 4D printing or materials that can change their shape over time. If this doesn’t seem practical, think again. Imagine a storm drain that contracts and expands with the flow of water or bone implants that adjust to a child’s growing body.
At the core of this technology are ‘smart materials’, which can expand and contract, change colour, and shift their shape based on changes in light, pressure, or magnetism. This way, they can adjust to environmental conditions without the help of robotics, automation, or electronics. Concludes Skylar: ‘This is a truly radical shift in our understanding of structures’.
What’s The Inspiration?
Nature. 4D materials are revolutionary for humans, but the planet has been manufacturing smart materials for a long time. A pine cone is a natural example. When the air around it is humid, it stays closed, encapsulating its seeds. But when it’s hot and dry—perfect conditions for its seeds to flourish in the soil—it opens and lets the seeds fall to earth. As our earth warms up and our factories, machines, and trucks face more extreme conditions, this type of adaptation could be just what we need.
As FastCompany reports, this type of technology has also been used at the nanoscale level for years. We’ve looked at how proteins fold and replicated it. But Skylar, an architect, designer, and computer scientist, wanted to bring it to the macro level. If we could do this type of work with proteins, he asked, why not with buildings, pipes, and bridges?
What Are The Implications?
‘4D printing enhanced by multi-materials technology may likely revolutionise our ability to control and precisely programme materials from idea-conception to printing shape-changing transformations’, Skylar explains. We’re not done yet, of course. We don’t just want materials to shapeshift however they like; we want them to transform in precise, pre-designed ways. That’s why researchers are still working on the algorithms and printing technology.
But it’s exciting. Parts could be put together by unskilled workers, which means that we could build complicated machinery in rural regions of the world. Infrastructure could more readily adapt to climate change. And, Skylar adds, ‘it’s a truly radical shift in our understanding of structures. [4D printing] allows us to give materials a life’.