MOM: A High-Value Starting Point for Digital Transformation
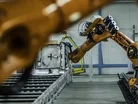
The hunger for transformation among industry players is at an all-time high. But at the same time, organizations want lower risk options to digitalize the shop floor. To reduce the number of isolated, inflexible solutions, manufacturers will want to seek a connected, scalable and sustainable platform approach that enables them to simultaneously maintain high levels of throughput, quality and customer service—while creating opportunities for sustainable innovation. This is where a Manufacturing Operations Management (MOM) solution comes into play. The experts at 3DS DELMIA, part of the Dassault Systèmes Group, take a closer look at MOM and how it can be so impactful for your business.
What Is Manufacturing Operations Management (MOM)?
A strong MOM environment on the shop floor is at the heart of digital transformation as this is where the product, business and operational functions of the enterprise intersect. MOM goes beyond traditional manufacturing execution systems (MES) as it involves automating, executing and managing the performance of all business processes relevant to manufacturing execution. This includes manufacturing production, quality, warehousing, the workforce and maintenance.
From design to build to support, digitalizing the entire manufacturing process with MOM enables manufacturers to gain global supply chain visibility to control and synchronize their operations with respect to these key modules.
Production: to boost operational efficiency, accelerate New Product Introduction (NPI) and reduce the cost of quality and compliance.
Quality: to enhance genealogy, traceability and containment as well as facilitate continuous process improvement.
Warehouse management: to synchronize material flow to production in real-time, improve operations performance and quality and enable a demand-driven enterprise.
Maintenance: to synchronize maintenance across all operations, increase equipment uptime, improve manufacturing productivity and quality, reduce maintenance costs and expand maintenance productivity and effectiveness to offline locations.
Time & labour: to optimize time and attendance tracking and eliminate paper tracking and manual data entry.
Beyond traditional business process accelerators, the optimal MOM solution functions as a comprehensive and core platform for manufacturing excellence. It helps establish a Center of Excellence (CoE) to drive process improvement configuration, distribution and governance, resulting in greater standardization with less effort.
Manufacturing leaders can leverage MOM and operational intelligence to unify data to identify opportunities for improvement and cost reduction. With a common platform approach to all operations, they can scale resources, enable centralized management of the system and standardize processes and best practices across sites. This eliminates custom systems and enables scalable continuous improvement initiatives on a global scale.
MOM is set to continue driving operations for several years. As such, it will naturally have to evolve and adapt as edge technology and IIoT continue to advance. For a more comprehensive and forward-thinking approach to transformation, manufacturers should consider these three aspects:
Cloud and on-premise: There is a growing movement to put applications in a cloud environment instead of on-premise, and for good reason: lower hardware and architecture costs, less need for on-site technical staff and reduced large capital expenditures for new systems. However, most companies are still hesitant to consider cloud solutions for MOM due to issues around internet latency and the risk of communication losses as MOM requires constant connectivity with mission-critical systems or applications. DELMIA can provide high-availability on-premise applications to help alleviate this risk.
Collaborative operations: Another critical consideration would be to invest in optimizing your team operations for more effective collaboration. Digitalization breaks down organizational barriers and allows each team to take the right actions, cascade decisions to stakeholders and collaborate seamlessly regardless of their role. With a solution like DELMIA 3DLean, managers can capture, monitor and track operational meetings on the shop floor by providing visibility across operations, accountability from all team members as well as improved collaboration. The solution brings Lean practices to the shop floor as an integral part of operations by providing a digitalized solution that empowers managers and teams to communicate, organize and solve problems more effectively.
IIoT: The Industrial Internet of Things (IIoT) is maturing and brings with it a major realignment of how and where IT is used throughout manufacturing operations and decision-making. The advent of digital transformation has boosted interest in MOM as a starting point for integrating factories into IIoT platforms. IIoT initiatives encourage manufacturing leaders to examine their current state of automation and MOM deployment to plan for digital transformation. However, IIoT can only deliver maximum benefit when the data collected is contextualized and actionable. In most cases, MES/MOM is the ideal companion to IIoT to both contextualize collected or traced data and to initiate actions in response to issues identified by IIoT. In essence, IIoT and MOM should go hand-in-hand.
Starting with a MOM implementation can prove to be a low-risk, high-value entry point for digital transformation and to modernize the shop floor environment for improved performance, a competitive edge and to better manage disruptions. Leveraging the likes of the 3DEXPERIENCE platform, you can unlock the potential for greater levels of manufacturing efficiency, productivity and profitability, bringing you closer to manufacturing and operational resilience.
- Semiconductor Shake-Ups: TSMC May Soon Make Nvidia AI ChipsAI & Automation
- Digitalisation as a Strategy to Attract and Retain WorkersDigital Factory
- Make UK & Autodesk: UK Manufacturers Lagging Behind on AIAI & Automation
- UPDATED VENUE & DATE – Manufacturing LIVE Chicago 2025Sustainability & ESG