One Point Lesson Plans - an effective learning tool in a manufacturing environment
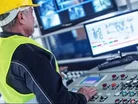
Today’s manufacturing equipment can be complicated in nature with many integrated components all controlled by computerized technology. The responsibility of running and monitoring the equipment and process can be an intimidating task to an equipment operator on the production floor. Manufacturers have learned a simplified design combined with operator engagement is the best recipe to deliver a highly reliable process and quality product. One of the leading tools to accomplish this engagement is the use of the OPL, or One Point Lesson Plan.
The One Point Lesson Plans are the cornerstone of any good technology transfer and training plan. As the term states, a One Point Lesson Plan is intended to transfer knowledge on one specific feature or function of a larger process. The format incorporates pictures to aide in the visualization of the task. As the tool is also used as a training aide, a training date and signature record is included. A Butler Automatic Splicer OPL can be seen in Figure 1. The OPL in figure 1 teaches an operator how to inspect film role core adaptors. Although simple in nature, a quality core adaptor contributes to the precise application of the film splicer when integrated with the larger production process.
As an OPL is intended to be an operator learning and training tool, many critical process parameters and tasks are communicated via this tool. The OPLs typically reside at the machine so operators can refer back to the instruction and reinforce knowledge as required. It is also intended that a trained operator can then utilize the OPLs to train new associates. Eventually operators begin to fully understand the equipment and process and can work to refine the process and improve overall operating efficiency.
By William Brum, P.E., Manager, Aftermarket Parts & Service at Butler Automatic, Inc.