Top 10 digital factories: Boeing
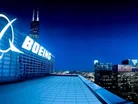
After ranking in our Top 10 digital factories, we look at the industry 4.0 solutions Boeing is harnessing within its facilities.
Dating back to 1916, Boeing has been a part of the American aviation and aerospace industry for more than 100 years. “From building biplanes in a red barn to designing rockets bound for the red planet, our story is unlike any other,” states Boeing.
“Boeing and its heritage companies have charted the course of aerospace history, helping to build and define an industry that has changed the world.”
Today, this message remains true with Boeing harnessing multiple industry 4.0 technologies within its operations, adopting innovation to not only build aircrafts of the future, but to improve its supply chain, sites and services, with employees at its core.
“We need to make sure people are an active part of this evolution — it’s really a revolution. It’s our people’s intelligence and drive that make all this possible,” said Jared McKie, 787 manufacturing manager, Boeing.
Utah
Within its facilities in Utah, Boeing is harnessing multiple innovative technologies to improve the capabilities of engineers and production lines.
Fabrication specialists and manufacturing engineers at Boeing work with composite materials, using a high-tech overhead “blanket” to remove air that can get trapped between the material’s layers. Using a ‘smart susceptor’ blanket engineers can also examine the layers before they are heated and compressed.
Within its final assembly factories in Utah, Boeing is harnessing moving production lines to produce its 737 MAX flight desks, In addition to using 3D-printing technology to minimise the number of parts for the 777X flight-deck.
California
In addition to Utah, Boeing is also using 3D printing (additive manufacturing) for metal and polymer parts for spacecraft, satellites and airplanes, as well as factory tools.
At Boeing's subsidiary Spectrolab, technician’s have adopted mobile computer carts rather than paper manuals when wiring solar panels to spacecraft. Not only are the wireless carts tidier, they help to streamline communications.
South Carolina
In South Carolina, employees of Boeing are testing advanced exoskeleton technology. An external wearable device that can increase the users mechanical leverage, strength or speed, as well as reducing strain and injury risks for employees.
Washington
Materials Management specialists in Washingtonare currently working with “Jennifer” - an electronic assisted transaction system. The system uses a finger scanner, small wrist computer and a headset to assist the user to find parts quicker.
Other innovations used in Washington include, automated tools that drill thousands of holes in composite empennage - tail units - for the 777 and 787 as well as install stringers in 777 and 777X wing structures. While site mechanics use optical laser templates to apply composite tape layers on airplane tails and stabilizers efficiently.
Robotic machines have also been adopted within Boeing’s facilities in washington to clean tools and produce advanced heat shields for commercial airplanes.
Missouri
While many teams across Boeing are harnessing ‘smart factory’ viewing tools that show productivity metrics in a visual representation of the factory floor, Boeing is effectively harnessing this technology within its facilities in Missouri.
To find out more about Boeing’s innovations, click here!
SEE ALSO:
For more information on manufacturing topics - please take a look at the latest edition of Manufacturing Global