Bridging the manufacturing industry’s skills gap
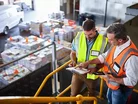
It’s no secret the manufacturing industry is in the midst of a talent drought; an estimated 186,000 new engineers will be needed each year until 2024, yet there’s a shortfall of 20,000 graduates annually. The challenge only looks set to intensify, with the UK government considering slashing the costs of humanity degrees to leave engineering courses as the more expensive option.
To maintain profitability, manufacturers must meet multiple objectives — such as creating new service revenue streams, boosting productivity, and developing better relationships with end users. But doing so is near impossible without the right people fuelling progress. And with manufacturing driving 26% of UK GDP, this puts the entire economy at risk.
The question is: what can be done to fill the growing void?
Bridging the skills gap isn’t just about attracting new entrants. Retaining existing staff is also key to effectively navigating the fourth industrial revolution as it transforms the way manufacturing operates. Consequently, it’s vital for businesses to develop talent strategies that build skills in emerging areas – such as AI and robotics – while holding on to traditional expertise.
With that in mind, let’s explore what’s causing the skills deficit, and how it can be addressed.
Barriers to training
According to a report published by the Department for Education, there is a shortage of specialist teachers in all school subjects that lead to further study in engineering. In addition, the Department for Business, Energy & Industrial Strategy and the Department for Education have found that the high cost of delivering up-to-date engineering training in further and higher education is also contributing to the lack of new talent entering the profession. As a result, talent stores are running low; with 85% of manufacturers stating they have skilled jobs that need to be filled. Meanwhile concerns about what will happen when the current aging workforce reaches retirement age are on the rise.
The importance of education
Universities hold the key to unlocking the skills needed by employers across a range of industries, sectors, and professions, and play a crucial part in increasing the number of applicants entering manufacturing. But the introduction of annual tuition fees of up to £9,000 to study a STEM course has caused applications to fall by 7.7% in England, according to UCAS, pushing more students away from an industry in high demand of new recruits. In addition, recent news cites the proposed decrease of fees in humanity degrees, which will only further alienate STEM qualifications to under graduates.
Despite these challenges, interest in manufacturing as a career can begin even earlier than university. Manufacturers must do more to partner with local schools and participate in careers advice events to drive awareness with young people. And for those school-leavers who don’t wish to contemplate a degree, there is more focus than ever on apprenticeships and the planned introduction of T-Levels – a vocational equivalent to A-Levels – that includes a three-month industry placement.
Modernising manufacturing
There is still a widely held and outdated image of manufacturing as an industry that it is low paying, unstable, and lacking in creativity. Manufacturers must lead the way in countering this misconception by creating a strong brand identity and an attractive place to work, thereby enticing more young talent and retaining existing workers. To achieve this they should communicate the vast opportunities the industry has to offer in terms of roles and innovation, in particular highlighting new doors opened by technological advancements in AI, automation, and the Internet of Things. They must take care to emphasise the fact that such developments create new roles, like user-interface designers or robot coordinators, instead of triggering job losses.
If manufacturing is to become future proof and continue to drive the UK economy, change is essential. It is crucial to increase the flow of incoming talent by connecting with potential industry workers at a younger age and reducing the cost of learning for relevant subjects. But it’s also important for the industry to keep modernising its practices, image, and recruitment approach in line with ever-evolving technology that is reshaping the future of manufacturing, and its workforce.
John Kirven is the Senior Value Proposition Consultant at Canon
- Indosat & Huawei Unveil US$200m AI Centre in IndonesiaAI & Automation
- LEGO Launches Vietnam Factory Manufacturing Training ProgramProduction & Operations
- Skillsoft: The Power of Training in ManufacturingProduction & Operations
- EV Manufacturing Faces A Major Skills Gap TooProduction & Operations