EV Manufacturing Faces A Major Skills Gap Too
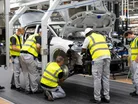
The EV industry in Europe is growing rapidly and plays a critical role in the continent’s transition strategy.
Many member states have ambitious electric mobility targets.
However, the transition is not without its challenges, like a persistent charging infrastructure imbalance and high vehicle costs.
The EV industry is also facing challenges that reflect those of the wider manufacturing industry, like an ongoing skills gap.
The lay of the land
While EV adoption is generally making good progress, there are stark differences in electric vehicle uptake, with Central and Eastern European (CEE) countries lagging behind their counterparts in Northern Europe.
The number of qualified EV professionals needs to catch up to meet growing demand.
"Looking to the UK, the Institute of the Motor Industry predicts that 77,000 EV-qualified technicians will be required by 2030, increasing to 89,000 in 2032.
"But the current uptake is slower than predicted, leading to a potential 16,000 technician shortfall by 2032." highlights Jon Lawes, Managing Director at MHC Mobility.
The future of automotive jobs
A study by PwC cautions that as Europe gradually adopts an exclusively EV fleet, 84% of the current 600,000 internal combustion engine (ICE) powertrain jobs will become outdated.
However, this shift will create over 200,000 new job opportunities in EV powertrains.
The transition poses a significant challenge for both the automotive sector and drivers, requiring a new set of skills and knowledge.
Focused action needed
Like the rest of the manufacturing industry, bridging the EV maintenance skills gap at scale will require targeted training, technology and the alignment of skills with EV technological development.
Jaguar Land Rover (JLR) has been actively focusing on skills development as part of its Reimagine strategy.
It includes the Future Skills Programme, which aims to train 29,000 employees in electrification and digital technology by 2030.
"Vocational training programmes can equip workers with the necessary skills, upskilling and reskilling them for the EV transition," confirms Jon Lawes.
Partnerships between industry and academic institutions are crucial to ensuring training remains relevant and up to date.
Government policy and reform
More government policy reform is needed to provide incentives for individuals to pursue careers in EV maintenance and for businesses to invest in training.
The European Green Deal is enhancing the skill set of automotive industry workers, and the launch of the European Battery Academy ensures access to quality battery training across member states.
The initiative, part of the EU’s Skills Agenda, aims to meet the demand for re-skilling or up-skilling 800,000 workers in the battery industry by 2025.
Looking at the bigger picture
Building Europe’s capacity to service and maintain its growing EV fleet will be a crucial component of the transport ecosystem and help create confidence in the switch to EVs.
Policymakers, educators, and industry leaders must collaborate across the continent, leaving no member states behind.
None of these solutions, vital to Europe’s green ambitions, can be implemented in isolation. Ultimately the EV industry must approach its skills gap in the same way all manufacturing sectors must, with patience, sustained effort and targeted innovation.
******
Make sure you check out the latest edition of Manufacturing Digital and also sign up to our global conference series - Procurement & Supply Chain 2024 & Sustainability LIVE 2024
******
Manufacturing Digital is a BizClik brand.
- Siemens, Sony & NVIDIA Unveil New Industrial AI Tools at CESAI & Automation
- Manufacturing Unwrapped: Inside IKEA, The Wonderful EverydayProduction & Operations
- Manufacturing & Mobility LIVE: The Future of EVs & MobilitySustainability & ESG
- Saab: Automotive Repurposing for Sustainable SuccessSustainability & ESG