Honeywell: Manufacturing & logistics warehouse automation
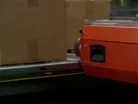
In an announcement made by Honeywell, the company has released its latest solution for intelligent automated handling. The new solution is designed to help warehouses, distribution centres, and manufacturing sites, receive, process, and fill orders faster and more accurately, as well as reduce the storage footprint.
Leveraging AI and machine learning
The next-generation Automated Storage and Retrieval System (AS/RS) leverages AI and machine learning providing warehouse and distribution centres greater capacity to keep up with unprecedented ecommerce growth.
"The rapidly evolving retail market is pushing distribution centres to find and use innovative, flexible and automated approaches to e-commerce order fulfilment. Growing inventories, the rising cost of land and other pressures are pushing operations to make the most efficient use of available space. Honeywell's next-generation AS/RS technology allows our customers to better utilise unoccupied vertical space, potentially eliminating the need for building or renting additional warehouse space,” said Ben Cardwell, president of Honeywell Intelligrated.
Space-saving solutions
Such solutions like AS/RS for space-saving is said to be a top priority for distribution centres looking to operate efficiently. A recent study conducted by Honeywell revealed that six in 10 ecommerce companies plan to invest in automated storage and retrieval systems over the next year.
A scalable solution
Offering scalability, Honeywell’s solution maximises floor space, and help organisations to efficiently manage over 20,000 SKUs using high-speed shuttles with configurable end and intra-aisle vertical lift locations.
Combining this solution with Honeywell’s Momentum Warehouse Execution System with Decision Intelligence, organisations can benefit from the ability to retrieve goods from one or more aisles and deliver them directly to a goods-to-person station for order consolidation; ideal for operations that handle small cases, trays, and totes.
"Distribution operators are now being asked to contribute more to overall business objectives, requiring managers to streamline processes, reduce costs and maximise the return on capital investments made in facilities. This technology delivers nearly a 40% increase in throughput over traditional picking methods, allowing labour to be used for other value-added tasks,” said Cardwell.
- Schneider Electric's Commitment to Sustainable ManufacturingSustainability & ESG
- Lenovo & Saudi Alat Building Green Manufacturing FacilitySustainability & ESG
- Nissan Brings Biodiversity to the Factory through RewildingSustainability & ESG
- Capgemini: Gen AI Cause of Spiking Semiconductor DemandAI & Automation