Artec 3D & HI: Printing Prosthetics for Rwandan Refugees
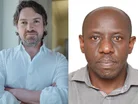
Introduce yourself and your role
Robert: I’m Robert Clement Hakorimana, Technical Project Manager (UQADR) at Handicap International (Humanity & Inclusion - Rwanda).
Art: I’m Art Yukhin, CEO and President of leading professional 3D scanner manufacturer Artec 3D.
What has Artec 3D been doing with NGO Handicap International in Rwanda?
Art: Artec 3D is working with Handicap International to help manufacture custom assistive devices for beneficiaries in refugee camps and their host communities in Rwanda.
After shipping a batch of Artec Leo 3D scanners to Handicap International (Humanity and Inclusion), and their partners, Artec 3D sent experts to train them on how best to digitally capture the measurements required for 3D-printing tailored prostheses, orthoses, and supports.
Measuring patients with 3D scanning makes the process faster, less invasive, and more readily available to those living in remote areas. Iteratively 3D printing the devices will also allow them to steadily be sized up, so young patients don’t outgrow their devices.
After five-days’ training at the HVP Gatagara facility in Nyanza, Handicap International staff and partners who participated in the training, have found they can confidently capture the data needed with pace and precision. They have also passed a troubleshooting test, giving them the confidence to move into end-usage.
Why have you focused these efforts on Rwanda specifically? Where else can you see the technology having a valuable impact?
Robert: 3D Technology is an innovation which is being introduced in the rehabilitation of persons with disability (PWDs), especially in the domain of Prosthetics and Orthotics in different countries where Handicap International intervenes, like Uganda and Rwanda.
Rwanda has retained attention due to its political will and orientation towards digital solutions in different areas of life. As we continue to register good results, I’m sure we can expand the technology into other countries where we are intervening (as HI).
Introduce me to the wireless Artec Leo scanner. How does it work? What are its features and benefits?
Art: Artec Leo is the world’s first wireless, AI-powered 3D scanner. With a built-in display and powerful processor, the ultra-versatile, all-in-one device makes the process of taking measurements quick and painless for both operators and patients.
Leo’s high degree of precision and accuracy helps ensure that medical devices fit as snugly as possible, so they’re comfortable for patients in the long-term.
Likewise, Artec Studio software support makes sure that data captured with this handheld 3D scanner can be processed with ease. It’s as simple as pointing and clicking to scan, then using advanced, automated tools to generate a 3D mesh ready for modelling.
What inspired you both to enter this line of work?
Art: Whether it be in implant design or treating injured Ukrainians, Artec 3D has continually sought out applications of its products that advance humanitarian causes. The company is delighted to see Artec 3D scanning being used to broaden healthcare access in Rwanda – an incredibly worthwhile cause.
Following the success of this initial project with Handicap International, Artec 3D hopes its technologies can be used to achieve similar humanitarian feats in other regions.
Would you say that the digitised nature of 3D printing- the fact it doesn’t require traditional, labour intensive supply chain operations- has made delivering humanitarian help easier?
Robert: If I may anticipate the results, according to my understanding and experience, I can say a big YES. But we need to confirm this with evidence once our production operations are underway and we have started fitting our beneficiaries and collecting feedback from them.
What has this experience highlighted to you about 3D printing and its applications in the sphere of medical manufacturing?
Robert: It has facilitated our beneficiary centred approach and eased the Community Based Inclusive Development (formerly CBR) model. Moreover, we expect it to speed up the process and reduce the time consumed to deliver services to our beneficiaries.
Moreover, it is expected to reduce the expenses we used to have on infrastructure and equipment, as it doesn’t require a big space and has reduced the number of machines needed for AT device production.
Technology and humanitarianism don’t always go hand in hand. What must manufacturers take into account when utilising technology to confront humanitarian challenges? How can we ensure emerging technologies are used in compassionate ways?
Robert: Even though there might be an injection of some “no-return budget,” the model should change from charity to contribution, where beneficiaries are sharing/contributing to the cost of the services they are benefiting from for sustainability.
Moreover, the manufacturer should take into consideration that their products are needed even by people with less to spend. They can also leave room for humanitarian situations, where they donate some of their products free of charge.
Can you tell me more about your plan to create children’s prosthetics that can be 3D printed to grow with them? And of any other future projects Artec 3D is considering?
Art: The problem with creating prosthetics for children is that they usually outgrow them. With 3D scanning and 3D printing, you can constantly iterate on designs, resizing and introducing new features to make medical devices comfortable to wear as young patients grow.
When children with knee joint or foot prosthetics grow into teenagers, this is essential.
We continue to lend our support to the team in Rwanda and identify fresh opportunities for our technologies in clinics and hospitals – areas where they’re already flourishing.
******
Make sure you check out the latest edition of Manufacturing Digital and also sign up to our global conference series - Procurement & Supply Chain 2024 & Sustainability LIVE 2024
******
Manufacturing Digital is a BizClik brand.