Bain & Company Report: Designing the Factory of the Future
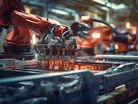
Original equipment manufacturers (OEMs) are facing increasing pressure to capitalise on emerging digital technologies and deliver additional value. In a relentlessly fast-paced, competitive world, manufacturers must strive for operational excellence on both traditional and forward-thinking levels. This is why companies are embracing Industry 4.0 technologies like robotics, additive manufacturing and AI, seeking to experience promised enhanced productivity, efficiency and safety.
The factory of the future is here. And yet…most machinery companies are not capitalising on it fully. Bain & Company, a global consultancy has released its ‘Machinery And Equipment Report 2024’. The report estimates OEMs leave 30% to 50% of productivity value on the table as they bring the factory of the future to life.
This is because OEMs still heavily rely on traditional lean manufacturing approaches, incorporating digital tools, sustainability measures and Industry 4.0 innovation in disconnected organisational silos. The report identifies leading OEMs as having incorporated an integrated approach, where digital technologies address significant pain points and enable upgrades across the company. They define established standards and interfaces across their online infrastructure and operating model, to scale their solutions and create a “factory of the future” roadmap.
The report identified four key steps OEMs should follow as they design their factory of the future approach.
04: Build a forward-thinking production system
OEMs need to build a new production system to help them move towards an integrated factory of the future. It needs to transcend traditional operational excellence and interconnect this approach with digital tools, 4.0 technologies and sustainability.
03: Identify key technological enablers
The IT/OT systems need to support the production system and include the appropriate reference structure, data architecture, databases, and interfaces so that they are cross-functional today and flexible to adapt to future requirements. This technology foundation should also enable interfacing throughout the supply chain with customers and suppliers.
02: Define future strategy
The factory of the future must be integrated into an overarching business strategy. A strategy which accounts for the state of the market, political factors, consumer behaviour and government regulation.
01: Make employees the foundation
Employees should be central to a company’s strategy, and their implementation of sustainability practices and technology should reflect this. The existing workforce needs to be upskilled, and new talent needs to be recruited who possess digital skills.
"It's about that human and automation interaction," said Kathy Wengel, Executive Vice-President of Chief Technical Operations And Risk at Johnson&Johnson in the video above on the future of manufacturing. "Making sure we have the skills that we need for what's coming at us for the future. We can't automate everything all at once, nor do we want too. So it's about making the thoughtful choices where technology really makes a difference."
OEMs must overcome siloed thinking, according to the report, integrating new industry 4.0 technologies into their traditional operational excellence approaches. COOs and chief information officers need to work together to develop a transparent overarching vision, communicating the case for change to the rest of the company. Digital solutions are never one-size-fits-all, and this extends to the manufacturing sector. They must be tailored to be at their most effective.
Every company, regardless of industry, will have a varying factory of the future approach according to their technology maturity level, customer needs and future ambitions. The report urges OEMs to consider the development of their factory of the future from the standpoint of their business needs, goals and future. If they do this, and follow the consultancy’s four critical steps, it’s unlikely they’ll be leaving 30-50% of productivity on the table any longer.
******
Make sure you check out the latest edition of Manufacturing Digital and also sign up to our global conference series - Procurement & Supply Chain 2024 & Sustainability LIVE 2024
******
Manufacturing Digital is a BizClik brand.
- POSCO: Steel Manufacturer Digitally Transforms Through AIProcurement & Supply Chain
- Bain & Co: Mexico Risks Missing Its Nearshoring PotentialProduction & Operations
- Cobots: Harnessing AI & Addressing Labour ShortagesAI & Automation
- Comarch: Digitalisation is Reshaping the Automotive IndustryAI & Automation