BMW: Creating Economic Circularity through Battery Creation
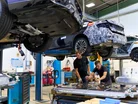
As the electrification of the automotive sector continues, more and more manufacturers seek greater circularity.
One manufacturer making strides in this area is BMW, building a comprehensive closed-loop recycling system for the reuse of raw materials from high-voltage batteries.
This system was created in 2022 thanks to the MW Brilliance Automotive Joint Venture (BBA) in China.
In 2024, BMW has enhanced the sustainability of this system even further by going beyond disposal to battery creation.
On the 1st of November last year the company launched a pan-European partnership with SK tes, a influential provider of innovative technology lifecycle solutions.
With SK tes, BMW has developed a special recycling process that procures cobalt, nickel and lithium from used batteries.
These materials are then sustainably transported and returned into the value chain to create new batteries.
BMW intends to expand this closed-loop system into the US-Mexico-Canada region as early as 2026.
Partnering with SK Tes
Through its long-term partnership with SK Innovation (SK TES), the BMW Group plays a direct role in the practical recycling processes, providing valuable feedback to its development teams.
SK TES’s battery recycling process has garnered numerous global awards for sustainability and innovation, including the Business Intelligence Group’s Sustainability Service of the Year and the UN Global Compact’s Apex Award.
High-voltage batteries from BMW Group’s development, production and markets in Europe that are no longer in use will be sent to SK TES.
This marks the first step toward creating a more effective and sustainable circular economy for batteries.
SK TES then transforms these old batteries into high-quality metals that can be reintegrated into battery production.
The process begins by mechanically shredding the batteries, concentrating the metals, and producing a material called black mass.
Through a highly effective chemical process known as hydrometallurgy, valuable materials such as nickel, lithium, and cobalt are recovered.
These secondary raw materials will be used in the production of the new GEN 6 drive train.
"Partnerships like this increase our efficiency in terms of the circular economy," adds Jörg Lederbauer, Vice President Circular Economy, Spare Parts Supply High Voltage Battery and Electric Powertrain at BMW AG.
"In the closed-loop process, all partners mutually benefit from their experiences."
The latter process sees the batteries mechanically shredded, during which the metals are concentrated to leave a material called black mass.
The valuable materials, namely nickel, lithium and cobalt, are then recovered in a highly effective chemical process called hydrometallurgy.
Among other things, these secondary raw materials will be used for the new GEN 6 drive train.
"Partnerships like this increase our efficiency in terms of the circular economy," adds Jörg Lederbauer, Vice President Circular Economy, Spare Parts Supply High Voltage Battery and Electric Powertrain at BMW AG.
"In the closed-loop process, all partners mutually benefit from their experiences."
Circular economy at the BMW Group
The BMW Group adheres to the principles of Re:Think, Re:Duce, Re:Use, and Re:Cycle, focusing on resource conservation in the context of the circular economy.
From vehicle design and production to recycling and reuse, every aspect is aimed at ensuring that BMW vehicles serve as a source of raw materials for new cars once they reach the end of their useful life.
A prime example of this is the BMW Group’s Recycling and Dismantling Centre.
For over 30 years, the centre has developed and implemented processes, making significant strides in parts and materials recycling.
The company’s strategy revolves around creating closed-loop systems, where materials are reused, refurbished and recycled to minimise waste and reduce environmental impact.
BMW also designs its vehicles with end-of-life recyclability in mind, ensuring that key components, such as batteries and electronics can be effectively recovered and reused.
By embedding circularity into its operations, BMW is playing a pivotal role in steering the automotive industry towards a more sustainable and resource-efficient future.
"The promotion of circular economy is an important strategic topic for the BMW Group," says Nadine Philipp, Vice President Sustainability Supplier Network at BMW AG.
"The development of recyclable products, the increase of secondary materials in our components, and the closing of loops play an equally important role.
"And by the means of circular economy we are also increasing our resilience in the supply chains."
Explore the latest edition of Manufacturing Digital and be part of the conversation at our global conference series, Manufacturing LIVE.
Discover all our upcoming events and secure your tickets today.
Manufacturing Digital is a BizClik brand.
- Aggreko: UK Energy Manufacturers must Shore Up Supply ChainSustainability & ESG
- Capgemini: Gen AI Cause of Spiking Semiconductor DemandAI & Automation
- Covestro & DB Cargo Drive Sustainable Polymer TransportationSustainability & ESG
- Manufacturing Unwrapped: Sequinova & Biodegradable SequinsProcurement & Supply Chain