Flex: Keeping up With Manufacturing Innovation
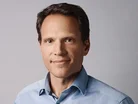
As the industry continues to work through constant change, Flex’s Paul Baldassari, President of Manufacturing and Services, reflects on technology and process changes and what the future looks like for manufacturers.
Supply chain disruptions have forced manufacturers to digitally transform faster than ever before. Can you talk about these changes and how we maintain the speed of innovation?
We’ve talked tirelessly about how connecting and digitising processes makes it easier to keep operations running smoothly. This trend, automation, and other advanced Industry 4.0 technologies will continue for years.
For the manufacturing industry, bolstering collaboration technology will be critical for maintaining the speed of innovation.
Connecting design, engineering, shop floor, and numerous other departments to make quick decisions is key to driving results.
Expect acceleration of digital transformations from network infrastructure to data centres, cloud computing, and more.
The companies that focus on low-latency, interactive collaboration technologies will find employees closer than ever before, despite being miles apart. And that closeness will lead to further innovation and progress.
Enhancements in artificial intelligence (AI) and big data analytics will also be critical.
We’ve made significant investments into digitalisation, including IoT devices and sensors that capture real-time information on machines and processes. As data-capturing infrastructure builds, making sense of that data will become much more critical. Workers in every role and at every level will be able to use these tools to optimise operations, predict maintenance needs, and address potential failures before they happen.
Finally, investment in IT and network security becomes even more important.
Manufacturers need to protect the success they have accomplished to date. So, teams must ensure there are no single points of failure that an external invader could use to shut down operations completely.
Beyond that, when partners know a network is robust, they are more comfortable allowing access to their environments, increasing collaboration and innovation.
What takeaway should manufacturers draw as a result?
The main takeaway for me is the power of connections. Restrictions have limited travel for our teams across the globe.
However, just because they aren’t physically next to me doesn’t mean we can dismiss them.
We learned that everyone needs to be an equal partner out of necessity.
And in a business where we’re producing similar products, or in some cases the same product, in China, Europe, and the United States, being able to learn from one another is a top priority.
The other takeaway is the importance of digital threads.
The ability to digitise the entire product lifecycle and factory floor setup increases efficiency like never before.
With a completely digital thread, teams can perform digital design for automation, simulate the line flow, and ensure a seamless workstream for the entire project — all from afar.
Because of these advances, economic reasons, and geopolitical dealings, we’re also seeing a big push to make manufacturing faster, smaller, and closer.
So, that means faster time to market through increased adoption of Industry 4.0 technology and smaller factories and supply footprints closer to end-users. Regionalisation is top of mind for many organisations.
What are some of the technologies and processes supporting the push for regionalised manufacturing?
Definitely robotics and automation. As the industry faces labour shortages and supply chain constraints, automation provides flexibility to build new factories and processes closer to end-users. It also enables existing staff to focus on higher-level tasks.
Perhaps one of the most significant supporting factors isn't technology, though, but upskilling people.
With automation and digitisation, system thinking becomes incredibly important.
With so many connected machines, employees need to make sure when they change something on one section of the line, it won’t have a negative downstream impact on another area.
Continuously developing the capabilities of operators, line technicians, and automation experts to operate equipment will help streamline the introduction of new technologies and keep operations running smoothly for customers.
What new tactics are you deploying that you previously didn't have on the factory floor?
We have implemented live stream video on screens that connect to factories on the other side of the world and even in some cases implemented Augmented Reality (AR) and Virtual Reality (VR) technology to provide a more immersive experience and simulate working with a product or line even though they’re thousands of miles away.
Setting up a video conference and monitor is a compelling and inexpensive way to link our employees.
In fact, due to regionalisation, we have colleagues in Milpitas, CA working on similar projects as Zhuhai, China.
Many workers at both sites are fluent in Mandarin and utilise the channels to identify how a machine is running and troubleshoot potential problems. In fact, some teams even have standing meetings where they share best practices and lessons learned.
What will manufacturing innovation and technology look like in 2030?
As I said before, I think we’ll see manufacturing get faster, smaller, and closer.
We see continued interest from governments in localising the supply base.
From a technological perspective, things will only continue to progress as the fourth industrial revolution rapidly makes way for future generations.
But a particular solution that has enormous promise is laser processing.
There is a considerable investment underway because you need laser welding for battery pack assembly.
With the push for electric vehicles from automakers, laser welding technology could be a standout technology moving forward.
******
Make sure you check out the latest edition of Manufacturing Digital and also sign up to our global conference series - Procurement & Supply Chain 2024 & Sustainability LIVE 2024
******
Manufacturing Digital is a BizClik brand.