Orange Business: Enhancing Safety through AI Augmented CCTV
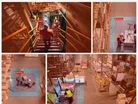
Smart factory solutions are not just about optimising the speed and efficiency of industrial processes. They’re also about addressing the needs of the workforce, enhancing productivity, communication and increasing safety.
All of these improvements can be made through targeted uses of technology and data, as optimised by the smart factory solutions of Orange Business.
Orange Business is a leading digital transformation partner, a global integrator of services and products for multinational corporations and the business services arm of Orange S.A
Last month, Manufacturing Digital had the opportunity to experience demos of some of its smart factory solutions.
We’ve since decided to delve deeper into one that showcases the way smart technologies provide a transformative degree of visibility across factory operations.
This greater visibility- enabled by tools like data and AI- enhances productivity, communication and increases safety.
Everyone benefits when employees across manufacturing operations, from frontline workers to supervisors are better connected and informed.
Orange has partnered with Surveily, a company that transforms existing security cameras into 24/7 monitoring systems through the power of AI.
Partnering with Miele and Nvidia in addition to Orange Business, Surveily is a notable leader in this space.
Together with Orange Business, both companies are increasing action, awareness and proactiveness around safety in manufacturing operations.
Safety: A major manufacturing concern
Manufacturing is an industry with extensive safety risks. LFS ranked manufacturing the second most dangerous industry this year, with fatal injuries 1.5 times higher than industry averages.
Workers operate large, heavy machinery, move through environments full of moving vehicles like forklifts and interact with corrosive and high-temperature materials.
A small error can easily lead to life-changing injuries.
With this in mind, safety is of paramount concern. But there’s a hurdle with safety that makes it harder to approach for organisations compared to assessing accidents or injuries.
How do you quantify safety?
This may seem like an obvious question at first. Surely we can quantify how safe an organisation is through its policies and accident rate?
Well, not fully.
Neither of these things tell you the whole truth about a company’s safety, nor do they capture attitudes on the factory floor. Here’s why.
1. A company’s rate of accidents can be misleading:
Sure, a workplace that has zero accidents per year compared to one that has hundreds likelier has a stronger culture of safety.
But this information doesn’t account for near misses or daily security violations that are flying under the radar.
2. Silence doesn’t mean ‘smooth operations’:
Equating silence to smooth operations is especially egregious when it comes to the manufacturing sector. In an industry where downtime is devastating, productivity is king, so workers from the factory floor to the executive suite have a vested interest in ensuring continuous operations.
The downside of this is that safety frequently becomes a lesser priority.
3. What’s counted as ‘safe’ varies from person to person:
As safety becomes a lesser priority, workers- who know they aren’t being continuously watched via CCTV- aren’t stopping their day to flick through safety policies. Therefore, there’s a tendency to go with gut instinct, what they would define as safe.
This can vary immensely from person to person. One man’s unacceptable risk is another’s innocuous “It’ll be fine.”
Therefore while you may have a unified standard safety policy across factory operations, the way safety plays out in reality is not always reflective of this.
With this in mind, how can manufacturers accurately quantify and understand the safety of their organisation?
The answer is data.
Orange Business in collaboration with Surveily is delivering on safety through data and AI.
The organisation connects existing CCTV cameras to an edge server, provided by partners including Dell or Cisco, which then using AI, processes and analyses safety risks in real-time.
Orange Business has around 50 use cases with Surveily which cover forklift speeding, handrail detection, PPE equipment during demonstrations, parking violations, footpath detection and overall compliance with safety guidance.
AI: A superior method of upholding safety
AI as a tool to detect safety risks and violations has several key benefits compared to human-operated CCTV.
The technology can detect safety risks across many screens simultaneously.
The average factory has at least ten to fifteen CCTV cameras, which no human operator can observe simultaneously.
AI doesn’t require breaks or rest, nor does it get tired.
Factories typically have long working hours, and this technology unlike a human can remain consistently alert and on-task.
It makes 24/7 security monitoring a reality.
AI also stringently adheres to programmed safety standards and can be immediately updated to reflect new laws or regulations.
Safety is a biased concept for all workers, including CCTV operators. It isn’t for AI.
The small safety violations that a person could dismiss, overlook or ignore won’t be missed by the technology.
AI can more accurately assess and cross-compare the speed of moving vehicles on screen.
This can make a profound difference to how quickly forklift speeding is detected, avoiding potential accidents.
In addition to this, AI stores what it has observed into meaningful data that executives can reflect upon and harness to enhance organisational safety.
The AI’s monitoring provides real-time alerts and updates to address current and evolving safety concerns.
With more cameras, come greater cables and installation bringing 5G into the equation.
Naturally, manufacturers don’t want all the video images collected by the cameras to be sent to the cloud for analysis, so a central reporting system is provided.
This provides the sheer amount of computing power needed on-site to support this AI monitoring.
This tool gives manufacturers the power to compare safety across their factories, identifying areas with significant security risks and understanding their causes.
Subsequent changes can be made to production lines, tailoring safety precautions to each specific factory rather than duplicating their initial set-up across operations.
Companies can identify and build training around the biggest risks in their company, evaluate if training is effective and understand holistically what safety problems they face.
This technology is an easy add-on to existing security infrastructure, that makes safety more proactive rather than reactive.
It’s already opening eyes to areas of safety previously overlooked.
Opening eyes to the reality of safety risks
In our recent coverage of the Vector Solutions safety report, we highlighted how 100% of workers surveyed identified the importance of safety training to enhance workplace security.
These same workers criticised their training as being reactive instead of proactive, only being informed of new safety measures when changes to the law were made.
This technology can help change that, by addressing nearly missed accidents, something which is frequently overlooked.
Risks like unauthorised doors being open, the lifting of heavy objects and environmental conditions are detected and raised.
Safety is thought of in terms of preparation and response- with little attention paid to daily, ongoing prevention.
Orange Business has highlighted the necessity of ongoing prevention by using Surveily's technology to address forklift incidents.
According to Conger industries, about 75 to 100 workers are killed annually in forklift accidents, with a rough average of 87 deaths per year.
According to research factories typically experience 4,000 near misses with forklifts before facing an actual accident. A tiny portion of these 4,000 near misses actually register as being just that.
Orange Business and Surveily's solution helps manufacturers proactively detect forklift risks, understand how they relate to organisational changes ( like an increase in orders/inventory) and enhance safety mindfulness within staff.
Orange Business implemented this technology into a factory where the safety department was reporting around 900 incidents per month.
After implementing the system, this number rose to 11,000.
The CEO of the associated manufacturer couldn't believe it. So, they looked at the system and associated data where every single one of those 11,000 incidents were documented with proof.
Going through all 11,000 incidents to assess them would’ve taken significant time, impacting productivity and focus.
Using AI, this analysis could be provided instantaneously.
Orange Business assists with all aspects of the integration, including adding the software with the cameras.
The company often finds itself adds additional cameras with enhanced connectivity, as manufacturers that implement this system go on to desire greater coverage with their cameras.
While this technology features AI, Orange Business discusses it in terms of safety to clearly define the business case.
This technology is the means, rather than the goal.
Orange Business continuously works with Surveily to add additional use cases, recently helping a brewery detect potential spills, a risk that can easily lead to what’s known as ‘man down’ in the manufacturing industry.
Enhancing people’s well-being and responding to man-down
One of the biggest risks in a manufacturing environment is a ‘man-down’ situation, where a worker starts experiencing a critical health emergency.
The rate of these incidents has risen worldwide in recent years, in conjunction with the average age of the manufacturing workforce.
There are many opportunities for ‘man down’ incidents in manufacturing, as workers operate heavy machinery, pick up and put down heavy objects and interact with fast-moving production lines.
The industry poses lengthy health risks which include exposure to harmful substances and chemicals, noise-induced hearing loss, and ergonomic hazards leading to musculoskeletal disorders.
Factories are closed-off spaces, and workers sometimes traverse them alone, creating prime conditions for deadly ‘man down’ outcomes.
If a lone worker suddenly experiences cardiac arrest, who is there to react?
There is the operator of a nearby security camera nearby, but who is to say that they're watching?
And when they do notice, will they be fast enough to get help to the worker in time?
These concerns are gone with AI-enhanced surveillance, which can create real-time safety alerts.
Orange Business also sees potential for this technology to be used for ergonomics in future use cases, analysing the risks of long-term strain and health conditions in the workforce as they perform repetitive manual tasks like bending over to pick up equipment.
Creating an incentive for safety
This technology also gives workers something else- an incentive to become safer.
You may read this and think that’s crazy.
Surely the incentive to become safer is, I don’t know, the desire to not be injured or killed?
The reality is, as environments and risks become habitual to us, we are all less likely to take the risk we could be injured or killed seriously.
And as previously discussed, there’s a big financial and operational incentive for workers to stay as productive as possible.
You can compare it to driving a car.
You are in an extremely vulnerable position, engaged in a high-risk activity that accounts for millions of deaths per year.
But I bet that isn’t what you’re thinking about on your daily commute.
You’re thinking about getting to work in good time, so used to the route your hands fly through the motions without a second thought.
The subtle near misses we experience as drivers- from getting too close to another car as we merge into another lane or needing to quickly brake- barely register.
You shrug it off and refocus on getting to work.
The same is true of workers on the factory floor. Operating large, deadly machines is habitual and through this people grow lax about their safety.
Unsafe decisions, like speeding in a forklift or taking shortcuts with machines, is employed to secure quicker results.
Whether it's in a car or on the factory floor, we’re all guilty of thinking we’ll be the exception.
The AI-enhanced CCTV tool gives employees an incentive to continually prioritise safety. Here are the three main reasons why:
- It communicates that company leaders take safety seriously, and are willing to invest in it as a priority on par with enhancing productivity.
- The reporting, data and associated insights highlight the areas where security is lax and the employees who are and aren't following procedure.
- The continuous observation enabled by the AI is likely to make employees conform to safety procedures due to the Hawthorne effect.
To expand on this final point, the Hawthorne effect describes the transformation of people’s behaviour when they know they’re being watched.
All sorts of behaviours which have opportunities for instantaneous modification are impacted, like hygiene practices and dietary habits.
There’s been a wealth of research and experimentation around this topic, embodied in the iconic and dystopian image of the panopticon prison, imagined by English Jurist Jeremy Bentham in 1791.
In the Panopticon prisoners would be observed by a single corrections officer, never knowing if they were being watched.
Its foundation is built on the idea that observation- even just the illusion of observation- conditions profound changes in human behaviour.
While I don’t imagine any manufacturer would want to impose real-time observation on their employees in such a shadowy manner, the principle here rings true.
By making clear safety is the ultimate priority, you can reshape employee behaviour- which is always the biggest challenge when it comes to safety.
Ultimately, at the core of this solution is visibility. Here AI and data unsettle a common and dangerous assumption made by leaders across industries: that silence means everything is running well.
When it comes to safety this can unfortunately mean the opposite.
Orange Business believes this technology will become standard in security cameras in the coming three to five years.
We can definitely see a future where that could be the case.
******
Make sure you check out the latest edition of Manufacturing Digital and also sign up to our global conference series - Procurement & Supply Chain 2024 & Sustainability LIVE 2024
******
Manufacturing Digital is a BizClik brand.
- Siemens, Sony & NVIDIA Unveil New Industrial AI Tools at CESAI & Automation
- Manufacturing Unwrapped: Orange Business's AI CCTVAI & Automation
- Sam Waes on Smart Industry Transformation and ManufacturingSmart Manufacturing
- How Google & Bentley's Digital Twins Enhance InfrastructureDigital Factory