ABB & Cemex: Bespoke Retrofitting to Drive Energy Efficiency
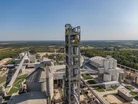
As both energy efficiency and technological advancement grow ever more critical to manufacturing, the partnership between ABB and Cemex is highlighting how the sector can effectively integrate both.
ABB is a leader in manufacturing and automation machinery, while Cemex is a global provider of building materials. Both companies have come together to enhance operations at Cemex’s facility in Poland.
ABB is providing bespoke retrofitting solutions that have not only improved safety and reliability but also dramatically cut down on energy consumption.
The initiative aligns with Cemex's strategy of integrating advanced digital technology to replace outdated analogue systems, in order to future-proofing its operations and enhance asset monitoring capabilities.
Cemex: committed to sustainability
A core aspect of Cemex's business and manufacturing philosophy is sustainable innovation.
This aspect is particularly observable at the Rudniki plant in Poland, one of the country’s primary cement suppliers.
The plant produces a variety of cement types and other materials, relying heavily on the seamless operation of its massive furnace, which requires up to 36 hours to light.
This extended light-up time means that even minor power interruptions can result in significant operational challenges.
Therefore, maintaining uninterrupted power supply is crucial for avoiding costly downtimes and ensuring continuous production.
ABB & Cemex: Longtime partnership
ABB and Cemex have had a strong collaborative relationship for over a decade, with ABB providing consistent and reliable service support.
When the Rudniki plant needed an upgrade to the electrical switchgear that powers its furnace, ABB stepped in with a precisely tailored retrofit solution.
This solution not only replaced obsolete components but also linked the plant to ABB’s advanced digital portfolio.
Key to this upgrade was ABB’s Emax2 circuit breakers, enhanced with Ekip Touch technology.
These breakers are celebrated for their robust protection features and a modular, interchangeable design that significantly minimises costs associated with replacing entire switchgear systems. This not only ensures a seamless transition but also bolsters sustainability.
The control and monitoring systems at the plant were also enhanced to include ABB's state-of-the-art digital analysers, which deliver precision measurements with an accuracy up to 1%.
This vital data is integrated into ABB Ability Energy & Asset Manager, a sophisticated cloud-based platform that allows for real-time monitoring of energy usage, power, and load.
A bespoke solution for Cemex
Following these technological enhancements, operational flexibility at the Cemex plant has seen substantial improvements.
Plant operators now have the ability to isolate and test specific breakers without disrupting the power supply to critical components such as the furnace.
This capability is crucial in preventing unnecessary halts in production.
These upgrades have helped optimise the thermal energy efficiency of the furnace.
This optimisation has had a profound impact on reducing CO2 emissions, highlighting the plant’s vigorous commitment to sustainability.
“This is a perfect example of a comprehensive retrofit, tailored to our customer’s specific needs,” says Kamil Schabiński, Project Manager for ABB Electrification Service.
“ABB products have transformed the plant’s operating conditions and the reliability and safety of its power supply.
“The new circuit breakers can be connected to the cloud at any time, which will further increase their digital functionality and energy management.”
Through ABB’s bespoke retrofitting solutions, Cemex’s facility in Poland not only enjoys enhanced energy efficiency and reduced environmental impact but also sets a benchmark in the manufacturing industry for sustainable practices.
This collaboration between two industry giants continues to pave the way for future advancements in the digital and energy-efficient transformation of manufacturing facilities worldwide.
Explore the latest edition of Manufacturing Digital and be part of the conversation at our global conference series, Manufacturing LIVE.
Discover all our upcoming events and secure your tickets today.
Manufacturing Digital is a BizClik brand.
- Capgemini: Gen AI Cause of Spiking Semiconductor DemandAI & Automation
- Covestro & DB Cargo Drive Sustainable Polymer TransportationSustainability & ESG
- Microsoft, ABB & Chevron: How to Scale Smart FactoriesAI & Automation
- Manufacturing Unwrapped: Sequinova & Biodegradable SequinsProcurement & Supply Chain