Infor: Confronting The Hiring Crisis of UK Manufacturing
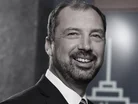
Introduce yourself and your role
I am passionate about innovation, and how today’s array of available digital technologies can grow and ultimately transform organisations of all sizes. So, I don’t think it’s surprising that I have been part of Infor for the last twenty years, now leading the International Solution Consulting team.
The team consists of solution architects and technical consultants, all focused on providing exceptional solutions to customers across EMEA and APAC.
The entire team is driven to create value for customers by architecting world-class cloud services, based on Infor’s portfolio of industry-complete CloudSuites, Strategic Edge solutions, digital platform technologies and innovation offerings.
What is unique about UK manufacturing? What are the biggest strengths of this country’s approach?
The UK has always been an innovator. After all, the industrial revolution happened here. While the nation’s output may not be the same as it once was, the drive to advance and progress remains central to our culture as a nation, and one of our biggest strengths.
That said, I believe it is less around the product itself.
While the industry collectively embraces technology like blockchain and digital twins to make products better, the real focus in on the process - feeding new ideas and capabilities into manufacturing.
UK manufacturers boast world-class philosophies that are adopted around the world, such as product designs like Dyson, manufacturing processes, research and development (R&D).
What is the current state of hiring in the UK manufacturing industry? What outdated perceptions about manufacturing do younger generations have?
The industry is facing a perception issue that is significantly hampering the success of hiring. Outdated views of manufacturing as blue-collar, in hundred-year-old factories, full of heavy machinery, dirty, grubby, with outdated tech are making it harder to capture the interest of future generations.
This stark view has been even further perpetuated by the fact that Gen Z has spent its entire life with technology front and centre and are therefore less likely to settle for what they consider a ‘low-tech’ job.
However, for most manufacturers, this assumption could not be further from the reality of the high-tech robotics and pioneering innovation that many are deploying. So, where is the issue?
Which emerging technologies can help shift these perceptions? How and why?
AI is often the most obvious, cited as the fourth highest priority for UK manufacturing leaders in 2024. Along with machine learning, AI facilitates smart, industry-specific applications that enhance the entire supply chain.
By processing vast amounts of data and take into account an inordinate number of data values, parameters and ‘what-if’ scenarios, it can produce accurate and timely recommendations for almost every aspect of the manufacturing process.
Overall, it’s a key tool for manufacturing leaders that want to increase productivity, as well as become a more attractive place to work.
Blockchain is another technology gaining attention. It enhances transparency, traceability, and security in the supply chain through smart contracts that automate and secure transactions between suppliers, manufacturers, and distributors, thereby reducing delays and disputes.
This technology appeals to those interested in sustainability and ethical supply chain considerations, helping change industry perceptions and attract talent.
Here in the UK, the amount of people entering manufacturing apprenticeships is declining. Why is this the case?
The availability of apprenticeships is very low, with a 34% decline over nine years of people starting them, making this fundamentally a supply and demand challenge. Those who get accepted often thrive, but unfortunately, for many the choice and variety is not there. Ultimately the power to change this sits with government and there is hope that the upcoming elections will bring a reinvigoration to maximise this vital opportunity for young people.
Part of the difficulty with attracting younger generations to manufacturing is the differences in their working priorities.Can emerging technologies provide the manufacturing workforce with greater flexibility?
Flexibility is definitely something that emerging technology can give the manufacturing workforce, but so is capacity, bandwidth, automation and business intelligence. Companies like Infor play a crucial role in helping UK manufacturers realise these advantages, if they haven't already.
While attracting young talent through technology is essential, equally important is examining the business itself, starting with its most valuable asset – its people.
Business leaders must look internally and understand what they want their vision to be. Technology, though powerful, must be applied strategically to support a modern workplace vision effectively. Only then can businesses truly benefit from emerging technologies like blockchain and AI and see an increase in flexibility, productivity and efficiency.
What do you think of the rising trend of reindustrialisation here in the UK? How can manufacturers embrace it successfully?
In my opinion, we have little choice but to embrace it. From a UK perspective, leveraging our extensive history and expertise is crucial, but we should aim higher.
I believe the UK should strive to be a high value manufacturing leader again, including advanced technology, high quality, highly engineered products and complex production techniques.
Rather than competing in low-cost mass production, we should utilise our strengths in product design, process innovation, and manufacturing excellence. So, if industrialisation can help get us there, we need to grab the opportunity with both hands.
If you could give manufacturers in the UK any advice about how to approach the hiring crisis, what would it be?
It would be to move beyond traditional methods and embrace innovation and technology.
Because embracing technology isn't just a one-time fix; it's a journey that involves leveraging cloud-based systems, breaking down data silos to make information accessible, and infusing intelligence into every facet of operations.
Simply put, innovative technology attracts talented individuals.
Ensure your toolkit is equipped to fully address current challenges but also to anticipate future needs. Because changing the hiring game and attracting young vibrant talent doesn’t come from maintaining the status quo.
The time for talking has passed, now is the time we all have to do something about it.
What are Infor’s plans for the next twelve months?
In the next twelve months, we are continuing our dedication to helping our customers win by becoming hyper-productive. Our strategy for this revolves around three core principles. Firstly, we are committed to delivering complete industry-specific solutions.
While we know that some software vendors say they are ‘industry specific’, in most cases it’s nowhere near enough for customer needs.
We’ve reached the next level by integrating the applications our customers use to manage their operations with cutting-edge technologies such as industry-specific AI and industry-specific automation.
Secondly, we help businesses embrace technology through a unified and connected platform for innovation.
We do the hard work of building a solution that has integration, security, data fabrics, AI, automation in the front and back end all baked into it.
This elevates our customers’ user experience, which is the third principle, and allow them to focus on efficiency and productivity.
We recognise that it is up to us to help manufacturers by providing applications that they actually want to use, which means consumer-grade tech, like the systems they have become accustomed to in their daily lives.
We are constantly adding to our vision of a helping to create a hyper-productive reality.
******
Make sure you check out the latest edition of Manufacturing Digital and also sign up to our global conference series - Procurement & Supply Chain 2024 & Sustainability LIVE 2024
******
Manufacturing Digital is a BizClik brand.
- Manufacturing Unwrapped: The Rise of Manufacturing CampaignsProduction & Operations
- Augury: How to Create a Healthy Organisational CultureProduction & Operations
- Why has CCEP Spent Millions on ASRS for its Wakefield site?AI & Automation
- Amcor & Power Roll: Pioneering Solar Photovoltaic FilmSustainability & ESG