Lenovo ISG: Edge Computing And The Manufacturing Sector
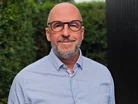
Please introduce yourself and your role.
I’m Anthony Sayers and I’m a Lenovo’s Edge Internet of Things (IoT) and Edge AI (Artificial Intelligence) specialist for EMEA Edge Computing at Lenovo ISG.
My role involves supporting board-level decision making and advising customers on approaches to their technology challenges in various sectors including manufacturing.
A key part of this is helping organisations in the manufacturing space to understand the opportunity offered by the IoT and Edge AI when it comes to building their own vision for innovation.
How would you define edge computing? What are its biggest benefits and challenges in
the manufacturing sphere?
Edge computing is defined by moving the compute to where the data is generated: in manufacturing, that means computing power within the plant itself for example, connected to Program Logic controllers (PLC), sensors or cameras overseeing the production line or robots on the factory floor.
In turn, edge computing enables IOT and AI to not only enable real-time decision-making on site, but also introduce capabilities connected to ‘Predictive Maintenance’ and even ‘Prescriptive Maintenance’.
For many manufacturers’ deciding and planning a digital transformation strategy for integrating operational technologies (OT) (factory IT) with IT (as defined by Industry 4.0) starts with breaking down well established silos whether it is an OT process, data silos and a divided workforce concerned with protecting jobs.
We are seeing industry professionals realise that to operate their business more competitively they must fully integrate the business.
It is vital therefore, to plan and implement an architecture framework to enable end to end digital transformation from the manufacturing floor to the IT datacentre.
Edge IoT and AI are a foundational solution framework that will help manufacturers to integrate, consolidate and digitalise their manufacturing operation.
Integration is enabled by for example: retrofitting sensors to production lines or integrating cameras into manufacturing process or connecting to manufacturing processes like closed loop lines to access data to begin data analysis.
For example, global technology startup, Rapyuta Robotics, uses Lenovo ThinkEdge servers combined with Rapyuta cloud AI to control and maintain autonomous mobile robots on the warehouse floor, so logistics companies can operate faster, more easily and more efficiently.
Controlling more than 500 robots in use at more than 50 distribution warehouses, the edge servers are used for real-time robot control and route optimization. In turn, companies can focus on their business process instead of managing hardware or software.
Manufacturers can introduce machine learning (ML) and create AI models to truly transform the business, whether it is for process automation to provide anomaly detection, predictive maintenance, quality control or safeguard workers from injury.
Factory operations that are using AI are able to predict failure need to know that they are going to have a failure in X number of hours and the corresponding preventative actions to avoid it, or to do a controlled line maintenance to reduce overall downtime. Predicting failure enables improves operation efficiency whilst creating key cost savings or extending the life of equipment.
Processing data at the edge ensures more security, reduces latency, enables real time decision making, reduces increasing centralised cloud data costs and decreases dependency on central cloud storage.
Many organisations are challenged with increasing market competition and market demand expectation outside of understanding the technological and business benefits.
Adopting and implementing these technologies creates additional capital pressure for companies to ensure rapid return on investment. Companies with the right vision and strategy stand to make this most ROI as they enable digital business transformation with long-term profitable growth.
Is manufacturing as a service the future of manufacturing?
Smart ‘manufacturing-as-a-service' has an important part to play in the future of the sector.
The concept of ‘smart factory’ underpinned by technological advancements, IoT and AI now enables industry to find new business and production models to approach manufacturing: one important new approach is manufacturing-as-a-service.
This approach sees businesses pay for manufacturing via the same ‘as a service’ model that organisations use to obtain software today. Lean, connected factories powered by IOT sensors and edge computing are central to this.
Manufacturing-as-a-service has the potential to revolutionise the whole manufacturing sector, creating a far lower barrier to entry, as well as reducing set-up times, addressing data security issues, and fostering new, collaborative ways to work.
Manufacturing-as-a-service will mean that companies may not need to invest in factory hardware when taking a product from the drawing board to shops around the world, which has the potential to change the way the whole sector operates.
Dark factories-what do you think about their application and feasibility?
Whilst we are seeing dark warehouse operations such as food basket picking, manufacturing will remain as a hybrid operation based on human processes and assisted automated functions that will enable predictive and prescriptive solutions through AI.
The workforce will reap the benefits of smart factory capabilities allowing it to focus on less mundane jobs, be safer and spend more attention on critical jobs and tasks where AI cannot perform.
Automation frees companies to utilise their human resources in roles that are far more beneficial. As factories
become more connected, we will see increasing adoption of digital twins which will enable managers and engineers to make the right decisions, simulating scenarios and outcomes whilst not directly impacting production.
They will be able to explore options such as the impact of raising production by a certain percentage, understand the corresponding impact on
manufacturing capability and resource, and generate agile production to adapt to market demands.
What do you see over the next 12 months?
Outside the increased adoption of Edge AI, Digital Twins, Augmented Reality, and Virtual Reality, the impact of Gen AI and Large Language Models (LLM) is going to have a profound impact on industry. We will also see the adoption of Small Language Models (SLM) to provide capabilities in domain specific sectors and environments.
We are also seeing key initiatives related to energy, environment, and sustainability. At Lenovo the EMEA factory based in Hungary recently added new solar panels to power its Innovation Centre with 100% solar power.
This brings the total number of panels at the plant to 5,072 which provide 3 megawatts of solar energy capacity, with a plan to reach 4MW at the plant.
Lenovo is reducing Scope 2 emissions worldwide with a plan to expand solar energy use: 17MW is currently operational, and Lenovo is investigating further opportunities in China, Mexico and Brazil.
Going forward, we expect that some manufacturers will become so sustainable, and will collect so much carbon credit, that those green credits become a new revenue stream. At Lenovo, we are set up to address edge use case solutions to full OT and IT digital transformation.
The ‘One Lenovo Pocket to Cloud’ capability coupled with Lenovo Financial Services, TruScale, and our partners, provide digital transformation as a unified integrated operation.
******
Make sure you check out the latest edition of Manufacturing Digital and also sign up to our global conference series - Procurement & Supply Chain 2024 & Sustainability LIVE 2024
******
Manufacturing Digital is a BizClik brand.