How Supply Chain Innovation can Stop Unplanned Downtime
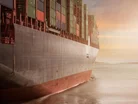
COVID-19 catalysed widespread adoption of sophisticated supply chain tools.
McKinsey & Company's Supply Chain Pulse Survey reveals that 79% of respondents now claim to have achieved end-to-end visibility.
However, numerous enterprises are lagging behind in this digital transformation.
Supply chain 4.0 for manufacturers
Supply Chain 4.0 encompasses the integration of state-of-the-art technologies such as automation, artificial intelligence, data analytics, and the Internet of Things (IoT) to revolutionise supply chain management.
By leveraging these advanced tools, manufacturers can reap the benefits of real-time visibility and data-driven decision-making processes.
“Industry 4.0 technologies are allowing us to shift from reactive to predictive strategies, helping manufacturers avoid unexpected disruptions.” says Tom Cash, Director of Foxmere.
Accenture's Deep Transformation with Smart Supply Chain Digitisation report provides a compelling example.
The study showcases a global retailer that increased its profits by 28% within three years of digitising its supply chain.
This clearly demonstrates the profound benefits of Supply Chain 4.0, driving greater efficiency, reduced costs and improved performance across industries.
Evolution of Supply Chains
Supply chains have undergone significant transformation over the past three decades.
Previously, logistics focused solely on transporting goods between points. Now, it encompasses a broader range of activities, including procurement, manufacturing, distribution and returns.
Modern supply chain management seamlessly connects customers with suppliers through the flow of information, goods and services.
"We've witnessed the emergence of roles like Chief Supply Chain Officer (CSCO), which didn't even exist decades ago," says Tom. "These roles reflect the importance of supply chains in business strategy."
The transition from manual to digital systems has revolutionised how businesses address disruptions, particularly unplanned downtime. Equipment failures or poor planning can lead to costly downtime, with industrial manufacturers losing up to US$50bn annually. In the automotive sector alone, production stoppages cost companies US$22,000 per minute.
“Unplanned downtime is a huge financial drain on manufacturers,” Tom says “but with the right tools, it can be mitigated.”
Preventing unplanned downtime
One of the biggest challenges for manufacturers is preventing unplanned downtime, which can result from equipment failures, supply chain disruptions, or inadequate maintenance strategies. Tom emphasises the importance of shifting to predictive maintenance, a crucial component of Supply Chain 4.0.
“Many plants are still relying on reactive, run-to-fail maintenance processes,” Tom explains. “But thanks to AI and IoT, we can now collect data in real-time from machines and predict when failures might occur.”
Sensors and connected machinery feed data into machine learning algorithms, which analyse patterns to predict potential breakdowns.
This enables businesses to perform maintenance before machine failures, reducing costly production halts.In the automotive sector, industrial sensors monitor robot performance.
If a robotic arm shows signs of wear, the system automatically triggers a repair order before production is disrupted. This proactive approach ensures operational continuity, saving time and money.Warehouse Management Systems (WMS) are another crucial technology, providing real-time inventory tracking across facilities.
When stock levels fall below critical thresholds, the system generates automatic replenishment orders. McKinsey & Company's research on the automotive industry demonstrates that manufacturers can:
- Reduce lost sales by 75%
- Lower transport and warehousing costs by up to 30%
- Decrease administrative costs by up to 80%
- Cut inventories by as much as 75%
Looking ahead: The future of supply chains
The outlook for Supply Chain 4.0 is increasingly promising, bringing big benefits to manufacturing.
Artificial intelligence is anticipated to play a pivotal role in enabling fully autonomous operations, enhancing demand forecasting, procurement and logistics.
In the near future, self-driving vehicles and drones may optimise delivery routes, significantly reducing transportation times and further boosting efficiency.
“AI is just the start,” says Tom. “The potential for technologies like blockchain to enhance transparency and accountability across the supply chain is enormous.
“Wherever you are in your Supply Chain 4.0 journey, having a reliable parts supplier is crucial. Companies like Foxmere ensure that critical components, like sensors, are always available and that maintenance processes are optimised to minimise the risk of downtime.”
Supply Chain 4.0 is no longer a distant vision – it has arrived and is transforming the way manufacturers function. By adopting these technologies, businesses can remain competitive and resilient in an ever-evolving market.
Make sure you check out the latest edition of Manufacturing Digital and also sign up to our global conference series - Manufacturing & Mobility LIVE
Manufacturing Digital is a BizClik brand
- How NVIDIA's Mega Omniverse Blueprint Transforms FactoriesTechnology
- KION & Accenture: Warehouse Optimisation through NVIDIA AIAI & Automation
- New Year, New Manufacturing: Fashion in 2025Production & Operations
- Manufacturing Unwrapped: An Interview with Brooke WeddleProduction & Operations