Nikon AM: The Quest To Scale Additive Manufacturing
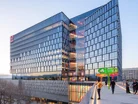
In October, Manufacturing Digital shared its top ten predictions for 2026.
High up on that list was the growing adoption and innovation of additive manufacturing. Why? Because it is the manufacturing method of the future, enabling rapid prototyping, superior customisability, sustainability, greater supply chain flexibility, safety, cost and inventory savings.
According to market research, additive manufacturing is set to hit a global market size of US$83.56bn by 2030. This is being driven by its strategic and creative value, harnessed by manufacturers across many industry verticals.
Earlier this year Manufacturing Digital reported on Adobe’s PDF Print Engine. A tool for 3D digital textile printing, the engine has enabled textile manufacturers to unleash new degrees of creativity, customisation and precision.
They can now reproduce vectors, fonts, gradients, motifs and more without fear of pixelation, while honing in on colour accuracy, producing garment prototypes without the associated waste.
“This is a longstanding principle in pre-press, going back to the desktop publishing revolution of the 1980s.” Mike Scrutton, Director of Print Technology and Strategy at Adobe, says.
“The net is that when text, images and graphics are rendered by Adobe PDF Print Engine, the resulting bitmap – which instructs the inkjet heads where to deposit the droplets – takes full advantage of the colour gamut of the press and also its other capabilities.”
“Digital textile printing is growing fast and designers are eager to take advantage of the technology to reproduce rich graphics on a wide range of fabrics: roll-to-roll, garment, home décor and signage.”
As the fashion industry shifts further towards servitisation, the adoption of the PDF Print Engine and by association additive manufacturing is more than just the embrace of new technology: it is an act of preparation for the future of industry, where supply chain resiliency and circularity will determine competitiveness and success.
This fact is intimately understood by Nikon, the leading Japanese photographic and optics equipment manufacturer. With a legacy of precision and innovation, Nikon is on a quest to help manufacturers embrace additive manufacturing to prepare for the future.
Vision 2030
Hamid Zarringhalam is CEO of Nikon’s Advanced Manufacturing Business Unit, which seeks to create the future of manufacturing through its Vision 2030 strategy.
“It broadly reflects our plan to be a key technology solutions company in a global society where humans and machines co-create seamlessly,” says Hamid.
“Nikon has century-old DNA that is deeply rooted in technology and manufacturing, and throughout the company’s history it has had profound impacts in these critical areas.”
The site of Nikon’s additive manufacturing innovation is its AM Technology Center, which opened earlier this year in July and is located in Long Beach, California.
The advanced, 90,000sq ft facility is already operational, setting new benchmarks in advanced manufacturing by providing specialised secure facilities, focusing on application development and benchmark testing.
“At the AM Technology Centre, we’re providing a holistic and customer-centric approach, with comprehensive Design for Additive Manufacturing (DfAM) services, engineering and manufacturing solutions, as well as prototyping and production capabilities,” Hamid explains.
“These services are designed to meet critical customer needs for adoption, scaling and supply chain capacity. The facility also includes Nikon SLM Solutions Studios as well as Nikon’s organically developed products. We will further use this facility for R&D and next-generation development.”
The centre consolidates a diverse and specialised global team, which includes Nikon AM Synergy, Nikon SLM Solutions Studios and Nikon Research & Development. Together, they focus on developing proprietary Nikon technologies.
“These include directed energy deposition (DED) solutions, as well as engineering innovations, demonstrations and next-generation system development,” Hamid says.
Nikon is a historic innovator in the field of applied optics application technologies. These technologies focus on harnessing light for practical purposes and include solar technologies, opto-mechatronics, semiconductor lasers, precision equipment, optical-electronic circuits and of course, cameras.
According to Hamid, these technologies, combined with their subsidiary investments and capacity to scale, will enable Nikon to “contribute to acceleration of technology and adoption of metal additive manufacturing at scale”.
Why is accelerating this adoption and scalability so important? It is because metal additive manufacturing is critical to not just the future of the sector, but specifically to Nikon AM’s aviation, aerospace and defence clients – clients that the AM Technology Center is strategically located to serve.
AM: the future of aerospace, aviation, maritime & defence
Aerospace, aviation, maritime and defence. Industries where people face myriad risks and are under intense pressure. In the maritime sector, this pressure is literalised, pressing down mercilessly on the hull of vessels and submarines. Additive manufacturing helps alleviate it.
The US Navy has adopted the method to keep its submarine plans on track, and Thyssenkrupp Marine Systems, the leading maritime manufacturer, has established its TechCenter Additive Manufacturing facility in Mülheim an der Ruhr, Germany.
At this facility, additive manufacturing is used to create spare metal parts. These parts are complex and expensive to source and create through traditional means, leading to long lead times. This is not the case with additive manufacturing, which also removes the need to secure high stock levels and navigate supply chains.
“It’s certainly still pioneering work, but the breakthrough has been achieved,” Stefan Lengowski, Senior Project Engineer (PLF) at ThyssenKrupp Marine Systems, says.
“Digitalisation can be experienced here and now. For me, the question about possibility no longer arises. Instead, I ask: ‘Where else is it possible and applicable?’”
Nikon AM has been asking this question, too. As the US Navy turned to additive manufacturing, the company has brought Admiral Mike Mullen, former Chairman of the Joint Chiefs of Staff, in as a Strategic Advisor. With his insights, the company can focus further on helping these high-risk sectors unlock the full potential of additive manufacturing.
“Only a very small percentage of all possible parts that could be produced using AM are using it today,” he says.
“Nikon expertise leverages decades of experience in rapid development and precision in optics technology and we believe we can help solve key manufacturing problems for these industries at the industrial scale.
“We need to accelerate and catalyse the customers’ AM journey for adoption.”
Catalysing the journey for adoption is a conversation about scalability. Despite AM’s capacity to solve manufacturing challenges and large R&D investments in the method by industry leaders like Nikon, its adoption is still stalling at 2.5%.
Additive manufacturing is notoriously difficult to scale for several key reasons. The production speed is slower than injection moulding or machining, making it less geared towards high-volume production. Quality control is also an issue due to the rigorous testing and certification needed.
Then you add metal into the mix, and these issues are exacerbated. Material costs for composites and advanced alloys are high, and to scale you need a reliable inventory across sites. Nikon AM recognises all these challenges and is working to combat them through research and innovation.
“Our substantial investments in R&D for next-generation solutions are focused on not only removing geometric and alloy limitations but also continuing to increase productivity to reduce production costs at an aggressive pace,” Hamid explains.
“Nikon is also aggressively developing AM solutions – not only focused on new build applications, but also on leveraging AM for a variety of precision repair applications as well.
“There are tremendous capabilities for reducing lead time and waste using AM repair instead of part or manufacturing mould replacement.”
Another challenge with scaling additive manufacturing is a lack of standardisation across printers and materials. The specialised software, hardware and processes used in additive manufacturing tend to differ from site to company. Aligning all this to scale is therefore a complex and costly process, limiting scalability.
Hamid notes this industry fragmentation, explaining how many believe it needs wider consolidation. In order to achieve this, he recommends manufacturers towards another industry that went under rapid consolidation: the semiconductor industry.
“AM equipment is a dual-purpose technology and can be used globally beyond civilian applications, so strategies similar to those used for other dual-purpose technologies need to be applied here,” he says.
“Accelerating adoption will require initiatives, approaches and scaling strategies similar to what the semiconductor industry has experienced, particularly in the last few years.
“These strategies are a key reason that semiconductors are not only ubiquitous but are also able to be manufactured at scale by several companies around the world and the majority of the time, are able to satisfy demand for ever-increasing applications, including extremely strategic ones.”
To read the full story in the magazine click HERE
Explore the latest edition of Manufacturing Digital and be part of the conversation at our global conference series, Manufacturing LIVE.
Discover all our upcoming events and secure your tickets today.
Manufacturing Digital is a BizClik brand.
- Thyssenkrupp Marine Systems: The Digital ShipyardDigital Factory
- The Manufacturers Leading Globally on AM Maritime SolutionsTechnology
- GKN Aerospace’s Additive Manufacturing Technology ExpansionTechnology
- Replique, the secure 3D printing platform for manufacturersProcurement & Supply Chain