NVIDIA explores the metaverse & AI in manufacturing
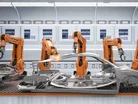
Accelerated computing company NVIDIA manufactures integrated circuits and graphics processing units, used across businesses, such as Amazon and Microsoft. The company has gone on to influence the manufacturing industry with its scientists, researchers and developers using NVIDIA technology to help businesses work together and with customers more efficiently.
NVIDIA has powered AI innovation for decades. Today, over 35,000 businesses are using NVIDIA AI technologies, and 15,000 global startups are part of the NVIDIA Inception programme. Since its founding by Jensen Huang, Chris Malachowsky and Curtis Priem in 1993, the company has continued to grow year-on-year. NVIDIA recently reported its revenue for the second quarter, US$13bn, an 101% increase from last year.
“A new computing era has begun. Companies worldwide are transitioning from general-purpose to accelerated computing and generative AI,” said Huang.
The company is based in Santa Clara, California, with more than 50 offices worldwide.
Ludwig von Reiche is the Managing Director of NVIDIA’s German companies. The German team is NVIDIA’s largest in Europe, covering a wide range of products and solutions for artificial intelligence, visual and high-performance computing, robotics and autonomous vehicles.
“Since its founding in 1993, NVIDIA has been a pioneer in accelerated computing,” explains von Reiche. “The company’s invention of the GPU in 1999 sparked the growth of the PC gaming market and redefined computer graphics. Later, it ignited the era of modern AI and is now fueling industrial digitalisation across many markets.”
Manufacturing businesses using the metaverse
The metaverse is a term for the 3D evolution of the internet and NVIDIA is focused on its industrial applications.
In an address at SIGGRAPH in 2022, Huang, NVIDIA’s CEO, called the metaverse the next evolution of the internet.
“The combination of AI and computer graphics will power the metaverse,” he said.
For von Reiche, this is an exciting opportunity for manufacturing.
“The industrial applications for the 3D internet, which include digitalisation – transforming traditionally physical processes into digitally-enabled processes – or, building virtual worlds to train the next wave of autonomous robots, vehicles and perception AIs.”
“Manufacturing businesses are using the metaverse to digitise difficult physical processes, such as designing and engineering physical products, or planning and operating physical factories and warehouses,” says von Reiche.
Many manufacturers are leveraging state-of-the-art simulation technology to create true-to-reality digital twins on a massive scale, including 3D replicas of entire factories.
“A true-to-reality digital twin means that everything in the physical world has an exact duplicate in the virtual world, all the way down to the literal nuts and bolts. A key aspect is that users can run simulations to test possible scenarios so as to pick the most optimal option. Furthermore, data from the real world captured through sensors can be fed into the digital version to synchronise the digital twin in real time.”
NVIDIA is working with many industrial companies and manufacturers to build digital twins of warehouses and factories to optimise their layout and logistics.
“We’re seeing customers across different industries digitising their industrial datasets, processes and systems.”
AI’s impact extends beyond industrial use cases. At the time of writing, US$235m has just been raised for an AI startup, Hugging Face. Founded in 2016, the company builds tools for AI developers to test their work. Backers included Google, Amazon, Intel, IBM and Nvidia.
“We are collaborating also with Hugging Face to simplify the creation of new and custom AI models for enterprises,” said Colette Kress, NVIDIA CFO, on the company’s latest earnings call. “Hugging Face will offer a new service for enterprises to train and tune advanced AI models powered by NVIDIA DGX Cloud.”
The evolution of the 3D internet
The evolution of the 3D internet is giving businesses various new opportunities, but there’s still a lot to learn.
“The ability to simulate and test thousands of scenarios and variations virtually, before and during physical production, saves cost and minimises waste, while increasing operational efficiency and accuracy – and in the end, a company’s competitiveness and bottom line.”
Several of the world’s leading manufacturers use NVIDIA Omniverse, a platform for developing metaverse applications and a compute engine for building and operating custom 3D pipelines, applications and virtual worlds.
“BMW has adopted a digital-first approach to its manufacturing process. In the past, reconfiguring production lines was an expensive endeavour, not least because of the production downtime,” explains von Reiche.
Moving valuable machinery and robotics is not a quick task, so BMW uses Omniverse to ensure decisions made in the physical world are supported by insights gathered in the virtual one.
“The digital twin facilitates hands-on problem-solving between numerous teams across different countries. In the metaverse, they can all interact with the same digital asset in real time. As a result, BMW has seen 30% more efficient planning processes, with reduced planning times and improved flexibility and precision.”
To maximise these benefits, the automaker is opening its newest electric vehicle factory in a virtual world two years before the real-world counterpart is due to be operational. BMW’s virtual factory is a physically-accurate digital replica, wherein logistics and production planners are able to virtually collaborate, visualise and decide on optimal production line design.
“This will enable BMW to reduce the risks and teething problems usually associated with new factories opening, and ensure success before committing to massive construction projects and capital expenditures.”
Manufacturers get more value from interoperable tools today because users are no longer limited to working within only one application.
“Planners, engineers and facility managers can view extremely large, complex datasets and workflows in context – seeing their massive factories, thousands of pieces of equipment and even simulated virtual workers all in one environment,” says von Reiche.