Three Key Panasonic Automotive Systems's Plants Turn Fifty
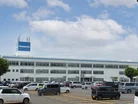
Panasonic Automotive Systems has announced that three of its primary plants in Japan, located in Tsuruga, Shirakawa and Matsumoto, are celebrating fifty years of operation.
“This 50th-anniversary celebration at the Matsumoto, Tsuruga, and Shirakawa plants was only possible thanks to the understanding and support of our customers, car manufacturers, suppliers of parts and materials, and the local communities where our plants are located,” says Masanori Minamio, Executive Officer of Panasonic Automotive Systems Co., Ltd.
“We would like to express our deepest gratitude.”
Panasonic, driven by its corporate ambition to become the “ Joy in Motion” design company, is leveraging its technologies and expertise in home appliances and digital AV to deliver superior customer experience.
The company wants all whose lives are touched by mobility- from pedestrians to drivers to cyclists- to be able to move peacefully, comfortably and sustainably through the world.
Sustainability in particular is something Panasonic Automotive is leading on, as the first company in the Panasonic Group to reach a major ESG milestone.
“ We are the first company in the Panasonic Group to achieve virtually zero CO2 emissions at all of our sites,” adds Mr Minamio.
“Our energy conservation activities have further evolved, and our energy consumption reductions have exceeded 3% per year.
“We were also able to halve the supply chain lead time at all of our plants in Japan.
“These initiatives have strengthened our ability to deliver necessary goods to customers when and as needed and have also made a significant contribution to the company’s management by optimising inventories and improving cash flow.”
This is an important contribution by Panasonic Automotive to the wider sustainability initiatives of the Panasonic group.
These initiatives have included the company’s drive to put recyclability at the core of its manufacturing processes and the PFS project to cultivate crops in extreme weather conditions.
Modern sustainability is driven by innovation, and there’s so much of it happening at the
Tsuruga, Shirakawa and Matsumoto plants which have contributed to their phenomenal longevity.
Each plant has its unique strengths and focus, contributing to the success of the Panasonic Group as a whole.
The Tsuruga Plant
The Tsuruga Plant first started operation in the 1970s. A sizable complex at 49,1910 square feet, the plant handles the manufacturing of in-vehicle sensors and switches.
Vehicle interiors have a massive influence on user experience, capable of enhancing comfort and ease or creating confusion and disarray.
Nobody wants to drive a car with a confusing, overengineered dashboard and interface that isn’t geared towards human comfort and safety.
Panasonic Automotive therefore pays close attention to its in-vehicle sensors and switches, seeking to continually elevate user and vehicle connectivity.
One way it achieves this is through digital transformation.
The Tsuruga site uses AI to analyse videos captured by 360-degree cameras, to continuously improve safety, and productivity and reduce waste.
The Shirakawa plant
Panasonic Automotive’s plant in Shirakawa has an important purpose: product evolution.
Established in 1974, it handles the mass development, production and manufacturing of in-vehicle cameras and in-vehicle equipment.
These systems drastically reduce the number of traffic accidents and better protect drivers when involved in accidents.
Subsequently, the Shirakawa plant plays a critical role in fostering safer and more secure mobility.
The Shirakawa plant manufactures these in-vehicle features in collaboration with the company’s China and Mexico bases.
“These three plants celebrating their 50th-anniversary play leading roles in manufacturing, each with its own unique strengths,” Mr Minamio adds, expanding on the unique features of each facility:
“Matsumoto’s adaptability allows for concurrent development. Tsuruga’s upstream processes connect devices and technologies. Shirakawa’s semiconductor technology capabilities can carry out manufacturing that no other company can match”
“We will continue our efforts to create even greater value and contribute to society by further developing and integrating the technological capabilities we have cultivated through our diverse manufacturing.
“The three plants are practising cutting-edge manufacturing in their respective production items and are also playing the role of mother plants*2 for our overseas plants around the world.
“Aiming to celebrate our 100th anniversary in operation, the three plants will continue to evolve through friendly competition in technology and skills.”
******
Make sure you check out the latest edition of Manufacturing Digital and also sign up to our global conference series - Procurement & Supply Chain 2024 & Sustainability LIVE 2024
******
Manufacturing Digital is a BizClik brand.
- Tata & JLR: Supercharging Next Gen Automotive ConnectivityTechnology
- Lenovo & Saudi Alat Building Green Manufacturing FacilitySustainability & ESG
- Rolls-Royce Invests Millions to Expand Goodwood FacilityProduction & Operations
- RIKEN & University of Tokyo Continue Fight Against PlasticSustainability & ESG