Private 5G: How is NTT DATA Future-Proofing Manufacturing?
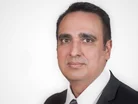
Parm Sandhu spearheads NTT DATA’s mission to develop cutting-edge digital offerings, such as Private 5G and Edge Computing fuel growth, to instigate transformative change for the company's enterprise clients.
His background in wireless IoT connectivity, industrial AI and 5G networks has enabled him to take the lead on this mission and future-proof the company's clients.
NTT DATA, a multi-national information technology service and consulting company, helps its clients transform their manufacturing operations through consulting, industry solutions, business process services, IT modernisation and managed services.
It serves clients such as Greene Tweed and TERNIUM, as well as over 10,000 other world-leaders across 50 countries.
Here, we chat to Parm about how critical smart factories and Private 5G could be for companies’ manufacturing operations.
How are smart factories and their associated data changing manufacturing operations?
While these technologies are enhancing the manufacturing process, in many ways, their proliferation means that the bar for manufacturers has never been higher.
Smart factories are optimising operations by fostering a hyper-connected environment, seamlessly linking people, machines, devices, and physical locations.
Advanced technologies like edge computing, industrial IoT, private 5G networks, and EDGE AI unlock a new level of control under which production output and quality soar.
Not only that, but costs shrink through improved resource allocation and minimised downtime, and customer satisfaction skyrockets thanks to faster response times and personalisation.
A real-time data stream, delivering operational and business insights, empowers smarter decision-making. Smart factories with digital twins are setting a new performance benchmark for the future of manufacturing.
Why are traditional cellular networks hindering the potential of smart factories?
While traditional cellular networks were key to the early days of industrial connectivity, they're falling short in the increasingly data-hungry world of smart factories.
The enterprise security requirements and sheer volume of data streaming from sensors, machines, and devices can overwhelm cellular network bandwidth, causing sluggish data transfer and bottlenecks in operations. But bandwidth isn't the only concern.
Latency and reliability are equally critical for real-time decision-making and precise control. Traditional cellular networks are susceptible to lags, dropouts or connectivity issues, which can introduce delays that can disrupt crucial processes and potentially compromise production safety.
In addition, the operations teams inside factories require service level agreements which traditional cellular networks are not accustomed to commit towards.
What is Private 5G (P5G) and why is it so critical manufacturers invest in it now?
Private 5G offers a bespoke, secure wireless network solution dedicated solely to a single factory's needs and giving full control to the factory operations team.
It provides a robust and secure infrastructure for connecting IoT devices, ensuring seamless communication between edge devices and central systems.
This translates to several benefits, including high bandwidth for data transfer, ultra-low latency for near-instantaneous communication crucial for real-time decision-making, and enhanced reliability thanks to a dedicated network free from competition and interference.
Private 5G boasts scalability and flexibility, allowing manufacturers to tailor it to their specific needs and adapt it as production demands evolve.
Investing in Private 5G now positions manufacturers at the forefront of innovation, securing a competitive edge for a future-proofed operation.
What are the compelling use cases for P5G and how can it be integrated with edge computing?
We’re seeing early Private 5G adopters in the manufacturing space focusing on applications that improve employee safety, customer experience, and operational efficiency.
The high bandwidth and ultra-low latency of Private 5G networks make them ideal for applications that rely on real-time data.
It also facilitates predictive maintenance through the analysis of sensor data to anticipate equipment failures and schedule maintenance proactively.
Similarly, real-time quality control with Private 5G allows teams to catch and address any issues on the production line as they happen.
These technologies are the cornerstones of Industry 4.0. Edge computing complements Private 5G by processing data locally on factory devices instead of relying on a central cloud.
- Enhanced security by minimising the attack surface through local data processing.
- Reduced latency for real-time decision-making with data processing conducted closer to its source to cut down on transfer times.
- Increased reliability with edge systems less susceptible to network outages that can cripple traditional centralised systems.
- Improved bandwidth by reducing the data load on your Private 5G network.
The synergy between Private 5G and edge computing is unlocking a new era of efficiency, agility, and resilience for smart factories.
What are the challenges in implementing edge and P5G and how can they be mitigated?
The sheer variety of devices and platforms in the IoT landscape creates a compatibility hurdle. A key concern companies have is that edge solutions won't integrate seamlessly, hindering investment.
To truly realise the promise of Private 5G and edge computing, enterprises need to modernise their networks.
A legacy network simply won't suffice for the real-time data demands of edge AI.
Consistent and secure edge application performance relies on robust network connectivity, which means that future edge deployments will strongly correlate to a complete campus network overhaul, for which Private 5G will be an important enabler.
Luckily, enterprises are catching on, with almost 40% acknowledging the need to upgrade their network to support the expected spike in connected devices and the demands of new applications.
What solutions has NTT introduced in collaboration with Schneider Electric?
In collaboration with Schneider Electric, we introduced a first-of-a-kind co-innovation that empowers enterprises to harness the power of edge computing.
This offering combines NTT DATA's Edge-as-a-Service with Schneider's EcoStruxure modular data centres, allowing companies to leverage edge computing with unmatched connectivity and efficiency.
The solution tackles compute-intensive tasks like AI inferencing and machine vision at the edge, while maximising energy efficiency with EcoStruxure's advanced data centre technology.
Our collaboration has already seen successful deployment at Schneider's Lexington Smart Factory.
Together, we're addressing Industry 4.0 challenges head-on, providing seamless connectivity, high bandwidth, and secure, low-latency connections through edge data centres.
If there was one thing you could say to the manufacturing sector about P5G, what would it be?
Private 5G translates to a smarter, more agile factory floor with optimised operations, improved product quality, and a significant competitive edge; a single machine vision industrial camera can replace thousands of sensors.
******
Make sure you check out the latest edition of Manufacturing Digital and also sign up to our global conference series - Procurement & Supply Chain 2024 & Sustainability LIVE 2024
******
Manufacturing Digital is a BizClik brand.