Q&A: Tackling the Labour Shortage with Digital Adoption
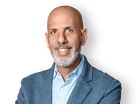
In the mid-90s, Adam Beckerman began his career in public accounting, with his first assignment at Croscill, a bedding manufacturer.
During this project, he toured the facilities and was captivated by the intricate processes behind something as seemingly simple as bedding production. This experience ignited a lifelong passion for the manufacturing industry.
Adam thrived on visiting manufacturers, exploring how things are made and understanding the processes behind them. For the past two decades, he has dedicated himself to advancing the business goals of manufacturers, whether they are start-ups, growing businesses, or preparing for an equity event.
In his current role as Aprio’s Manufacturing & Distribution Group Leader, Adam advises C-level executives and finance managers from mid-market companies across various sectors, including hardware, medical devices, chemicals, plastics and flooring.
Always on the lookout for new ways to innovate, he remains committed to supporting both clients and prospects with expertise and enthusiasm.
Here, Manufacturing Digital discusses his thoughts on how to tackle the labour shortage with digital adoption.
Manufacturing is facing a staffing challenge- how do you think the industry can work to overcome this?
There is still a big misconception that the manufacturing industry doesn’t offer much career growth when, in fact, it is very advanced and offers a wealth of opportunities.
To overcome this challenge, the industry must figure out how to amplify this message and introduce the career path to younger generations. College students and even high schoolers, should be educated on what kind of career they can have in manufacturing.
This could be implemented through after school activities or even as a part of the curriculum itself. As for digitisation, automation and process improvement, they are an integral part of overcoming staffing challenges as well.
Manufacturers must figure out how to do more with less, but adopting technology that enables this is not the complete answer.
Organisations should also strive to think outside the box and consider non-traditional hiring programs such as partnering with technical or trade schools, integration with high school programs, or other less traditional hiring approaches. These can serve to build awareness of opportunities in manufacturing and attract new employees to the industry - while also increasing retention of the current workforce.
How should industry leaders appeal to a new generation of manufacturing workers?
Education is one of the most important routes that industry leaders should take to introduce manufacturing to younger generations whether that comes in the form of educating high school students on the field, attending career days at college campuses or even hosting “bring your kids to work” days.
Presenting special educational options will give these students more options to enter the workforce and increase general awareness of the opportunities a career in manufacturing can provide.
Once these generations actually reach the industry, I would suggest that organisations strive to create a wonderful working environment – one in which employees look forward to working with every day.
For instance, companies with a strong workplace culture have 72% higher employee engagement and experience 40% lower turnover.
Additionally, manufacturers should make their employees part of the decision process as much as possible. When employees are involved, they essentially are given true authority to make an even better environment for themselves and their coworkers and it will help increase retention rates.
Have you seen any specific examples of hiring success in the sector? What strategies were implemented?
In my role at Aprio, I’ve seen how consultative, advisory services are a successful avenue to helping manufacturers address issues with labour shortages, among other things.
Services as such can help manufacturers assess factors like current staffing needs, in which departments they can ramp up quickly, what roles they can automate and more.
In terms of specific examples, back in the late 2000s, Southwire, a wire and cable manufacturer located in Carrollton, GA was having a hard time finding staff. Concurrently, the public school system in the area only had a graduation rate of about 60%. Because of this, representatives from Southwire and the schools got together to discuss and develop a win-win situation – a program called 12 for Life that is still active to this day.
The program allows high school students to split their days by taking classes in the morning and working in the Southwire facility for the remainder. By the time graduation rolls around, students are offered a full-time position at Southwire. This is a perfect example of how education from an early age can benefit future employees, employers and the industry as a whole.
Please tell us about your outlook for the latter half of 2024- what’s in store for the industry?
It’s going to continue to be a little choppy, especially with the election coming up.
We’ve had mixed signals within the industry with the latest PMI in July showing 46.5 which is a decrease from June, indicating that there is contracting in the industry. While manufacturers are still growing, they aren’t at the same level as they have been the past few years.
Organisations will continue to look for ways to increase the bottom line and look towards operational improvements. With the technological advances we’ve seen and will see, these manufacturers will need to make some moves and invest or be left behind.
Make sure you check out the latest edition of Manufacturing Digital and also sign up to our global conference series - Procurement & Supply Chain 2024 & Sustainability LIVE 2024.
Manufacturing Digital is a BizClik brand.