Vector Solutions Report Identifies Increased Safety Concerns
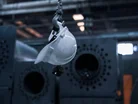
As June’s National Safety Month is well underway, Vector Solutions’ new State of Industrial Worker Safety and Well-Being Report has identified a growing number of US employees are facing manufacturing related dangers.
As the cost of living rises and the job market narrows, the blue-collar industry has seen an influx of employees.
However, Vector’s new data shows manufacturing employers’ safety measures are not ready to accommodate this surge.
The report surveyed 602 full-time industrial workers, who ranked safety as the second most valued aspect of an organisation.
The safety concerns found within the report, if left unaddressed, could steer employees away from manufacturers who do not update their safety measures.
Inadequate training proves the main culprit
An overwhelming 100% of workers surveyed identified the importance of safety training for a secure workplace.
However, Vector found that 47% of employees view their provided workplace training as reactive, meaning they were only informed of new safety measures when changes to law were made.
The study also found that in order to maintain employee retention rates, safety training should remain up-to-date and engaging.
50% of workers found their training lacking in engagement, whilst 57% say that safety issues make more seasoned workers leave, showing the drastic impact of training on employee retention and loyalty.
Of those satisfied with their training, 95% say it makes them more confident, 72% say it motivates them and 81% say it makes them feel more inclined to stay working for the company.
This indicates a need for manufacturing employers to prioritise their safety training, both to improve staff retention rates and company image.
81% of those surveyed expressed that serious safety concerns have a negative impact on their employer’s reputation.
Meanwhile, half of non-native English speakers say their company did not offer training in their native language- meaning vital safety information could be missed and putting non-native speakers at a higher risk than their peers.
What can manufacturers do to improve safety?
When 43% of employees report their workplace experienced a safety incident in the past 12 months and 46% of workers believe their employer could do more to reduce safety incidents, it is clear the industry needs to improve- but how?
- Update and maintain equipment: 30% surveyed by Vector Solutions report outdated equipment, whilst 26% report that it is not maintained.
- Offer more languages for training courses: 45% voted this would improve safety in their workplace.
- Deliver training to mobile devices: 44% voted for training to be delivered to their mobile phones, whilst 41% voted for it to be delivered online.
- Refresh training frequently: 30% of those surveyed think refresher microlearning training courses of 3-5 mins, delivered on their mobile phones, would improve safety. 16% voted for a higher frequency of standard training sessions.
- Make training content engaging to improve retention: 20% voted that the training should have more videos to make it more engaging.
- Update training regularly: Finally, 11% voted for more regular updates to content. This would mean the newest safety guidance could be included at the earliest point possible, not just when safety concerns become law.
Vector's research offers industry leaders the insight to make manufacturing workplaces safer, improve employee retention, and improve brand image.
Employees currently believe that safety incidents could have been prevented at rates of 88% (some incidents) and 27% (all incidents).
By prioritising these factors, businesses may prevent these incidents, decrease wider safety concerns and improve economic efficiency in the long-term.
******
Make sure you check out the latest edition of Manufacturing Digital and also sign up to our global conference series - Procurement & Supply Chain 2024 & Sustainability LIVE 2024
******
Manufacturing Digital is a BizClik brand.