Digital Twins: What Do You Mean by That?
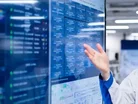
For example, this spring, the 36th America’s Cup is scheduled to showcase the space-age, super-fast AC75 mono-hull yacht. In trials, digital twin technology was used by one team to emulate the performance of sailors in a new AC75 boat; a feat that radically accelerated prototype development compared with previous testing methods.
Now deployed in areas such as city planning, healthcare and automotive design, digital twinning also holds immense potential for the manufacturing sector – helping in its ongoing quest for enhanced safety, improved productivity and greater efficiency.
The Detail is in the Data
Given its newfound status, the term ‘digital twins’ has become somewhat of a catch-all for various associated strains of technical innovation. Augmented reality, enhanced user interfaces and 3D-modelling – to name a few.
In addition, we also have the idea of the ‘digital thread.’ This refers to the communication framework that enables a connected data flow and integrated view of an asset’s data throughout its lifecycle. As a record of a product or system’s lifetime, from creation to removal, the digital thread enables insight across traditionally siloed functions.
And while it is true that these innovations may all involve associated functionality, the core of true digital twinning lies in data – pure and simple. A digital twin, in essence, is the generation or collection of digital data representing a physical object in real time.
Relate this to manufacturing, and if we were to hypothetically associate its core components with human characteristics: operational equipment would be muscle, connectivity the nervous system – and, the digital twin – that’s the brain.
And, as we intuitively use our brains’ capability to remember, record, analyze, process and predict in the real world, so can digital twinning analyze collected data to do the same in the digital one. In the manufacturing world, the data inputs that contribute to digital threading and digital twinning optimize operational functions, which help to increase throughput and improve efficiency.
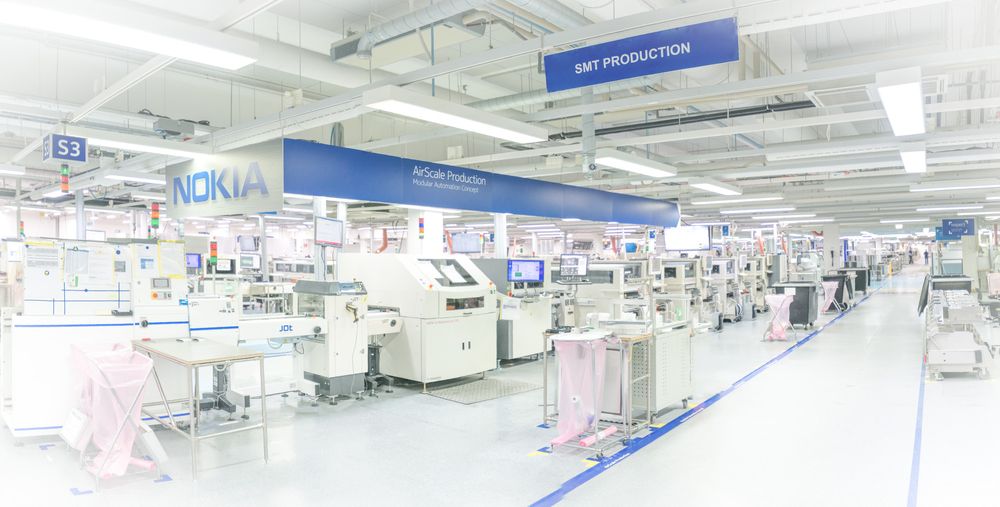
Conscious Factory
In manufacturing, where as much as 90% of real-time factory data goes unused, digital twinning provides a strong foundation for better utilization of that information for process insights.
From experience in our Oulu ‘conscious factory’, we have first-hand knowledge of leveraging the intelligence embedded in operational equipment to assess these insights via digital twinning.
For example, monitoring of the production environment. Here, utilizing a variety of data sources, deviations in humidity and temperature can be observed with automated alarms triggered to identify where adjustments or maintenance may be necessary.
Digital twinning also provides automated real-time process analytics across connected machines and data sources, which speeds up error detection and correction. And, with monitoring of the assembly process, also in real-time, the status and progress of each robot cell can be viewed at any time from a central user interface, with a level of visibility right down to the individual product.
Infrastructure Matters
Of course, there are infrastructure requirements necessary to make this level of insight a reality.
Embedded intelligence is the first requisite for digital twins. The internet of things (IoT) is quite literally exploding the number of sensors in manufacturing facilities. And this increase in data-generating capability is more and more being built into production equipment at its design phase. The ability to process and standardize data also has to be matched by analytics know-how over the top that can make sense of what is being generated.
The correct kind of flexible, robust connectivity is also crucial. This usually means connectivity at an industrial grade that exceeds Wi-Fi performance. Increasingly, manufacturers are moving to 4G/LTE and 5G private wireless networking to deliver the levels of reliability, security and high bandwidth necessary for data-hungry operational technology.
As part of their digitalization and Industry 4.0 journey, manufacturers are also looking at artificial intelligence (AI), machine learning, automation and augmented intelligence. However, all these eye-catching capabilities require one stand-out connectivity essential: low latency.
Real-time and Interconnected
In this respect, 4G/LTE is the minimum standard of wireless connectivity required to deliver the kind of low latency and fast response time that makes digital twins effective – delivering data instantaneously and enabling immediate operator response. This highlights the need to process data at lightning-fast speed, which makes edge computing a must-have.
5G holds an even greater promise for manufacturing, as the standard evolves and supporting ecosystem develops. With the 5G standard in ongoing development, subsequent releases will feature new capabilities such as time-sensitive communication. This will deliver tighter synchronization of communication and control between devices as well as improved positioning and localization.
Additionally, system interconnection has to be considered; highlighting the need to communicate and integrate across various standards and protocols at use in production facilities. Here, networking connectivity needs to provide a kind of simple, streamlined ‘data exchange,’ with industrial connectors operating as an important part of the equation that gets systems to talk to each other effectively.
Upsides
With vendors now fast addressing these infrastructure requisites, the potential upsides for manufacturers are substantial. Automation of supporting processes, real-time reporting, improved factory performance, superior quality assurance and fast response times are all made possible by digital twinning what is happening on the factory floor.
The digital twin approach provides an excellent way for manufacturers to flexibly model how to configure workflows and resources in response to changing product demands and order pipeline.
And while digital twins can enable us to do so much more, they do not replace the human touch. The goal of Industry 4.0 should be to augment human intelligence, rather than replace it. Digital twins augment human insights into manufacturing processes, and arguably, they can make ‘plain sailing’ not only of the America’s Cup, but also for the use of data to identify where industries can make safety, productivity and efficiency gains.
- Digitalisation as a Strategy to Attract and Retain WorkersDigital Factory
- UPDATED VENUE & DATE – Manufacturing LIVE Chicago 2025Sustainability & ESG
- ABB Cuts Industrial E-Waste in Quest for CircularitySustainability & ESG
- Why Are Manufacturers Doubling Down On Digital Twins?Digital Factory