Preddio Technologies: Making Industry 4.0 a Reality
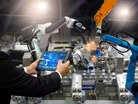
As themes of digital transformation continue to top boardroom agendas as we come out of the pandemic, manufacturing enterprises have been looking to IoT technology to pave the path toward Industry 4.0. The fourth industrial revolution driven by IoT technology has illustrated the initial ability to improve the productivity and reliability of physical assets. Furthermore, IoT ROI in the manufacturing industry as part of Industry 4.0 can be reasonably straightforward, as the value of product or manufacturing downtime easily justifies IoT investments.
However, despite IoT being broadly labeled as the door opener to Industry 4.0, the reality is that there’s no such thing as a one-size-fits-all approach for Industrial IoT (IIoT) that works. While the growing demand for more on-demand insights into manufacturing operations is undoubtedly a testament to IoT’s various capabilities, manufacturers need to have a clear understanding of what they hope to accomplish with transitioning into an Industry 4.0 environment. This means an application-specific mindset towards IoT is required to make Industry 4.0 a reality.
In the early years of IoT, many engagements failed due to a lack of experience, precise requirements or maintenance commitment. Therefore, enterprises must establish early on what they hope to get out of their IoT solution and create a plan of attack around their business’ specific needs. When enterprises fail to have clear objectives in mind, they’re not only paving an inefficient path towards Industry 4.0, but setting up their operational failure as well.
By implementing IoT programs through personalised and curated sensors embedded in assets that are specific to industrial applications, manufacturing enterprises can render ROI-driven implementations that create real business value and transition into Industry 4.0 with grace.
Here are some ways to harness this approach.
Manufacturing-Specific IoT Applications to Consider
IoT applications have common themes across a variety of industries, regardless of the segment. However, given the manufacturing industry’s unique set of needs and concerns, four consistent IoT applications have emerged for harnessing the automation and data enhancements that Industry 4.0 promises. These include predictive analysis, improved efficiency, increased safety, and optimised productivity.
Predictive Analysis: Applying IoT technology for predictive analysis is one of the most compelling use cases for IIoT systems today. These initiatives enable the performance of critical manufacturing equipment. Physical asset performance analysis, including condition monitoring and failure prediction, is the key to enhanced outcomes. This use case directly addresses a standard error in judgment within the industrial sector: if the asset is broken, then fix it; otherwise, check on it periodically.
Improved Efficiency: Improving the energy efficiency of physical assets is a common management objective that can be accomplished effectively today using IoT. In manufacturing especially, it’s critical to monitor and reduce energy consumption wherever possible. More broadly, OEM-designed physical assets, for example, consume substantial energy across many applications. However, because they are often mechanical or thermal, these assets are prone to degraded operation and failure over time.
Increased Safety: Amid the pandemic, addressing safety issues with IoT has become a major use case. However, even post-pandemic there are ongoing manufacturing hazards for equipment, people and surrounding communities that can be minimised with the usage of IoT. Measurement of high voltage, monitoring of refrigeration temperatures, volatile gas and liquid handling, effluent release of chemicals, nuclear radiation, construction site safety and unauthorised intrusions are only a few of the areas where IoT is increasingly deployed.
Optimised Productivity: Improving overall equipment effectiveness (OEE) is yet another critical consideration for manufacturing enterprises. By leveraging the power of cloud computing and IoT, it is possible to deliver exceptional returns. ITIF Research found that monitoring machine utilisation with IoT can improve manufacturing productivity by 10 to 25 percent.
While these four applications can be used separately or collaboratively to drive deployment in industrial applications, they share a commonality: visibility over physical assets. And all that data being extracted from physical assets paints a picture of what an enterprises’ future can become. What a company chooses to do with that data is entirely their decision. Therefore, starting with specific applications in mind puts enterprises in the best position to leverage IoT technology to transition into Industry 4.0.
New Innovation for Specific Use Cases: Digital Twin Technology
As Industry 4.0 works to bridge the gap between IT and OT to create a cyber-physical ecosystem, enterprises can now receive more insights into their most critical physical assets by visualising data in new and innovative ways through IoT technology.
An up-and-coming innovation with IoT is the concept of digital twins. Essentially this means digital replicas of physical assets. Successful IoT programs deploy digital twin concepts as a way to make sense of complex data. Data without relevant context is redundant to existing legacy systems, expensive and provides limited value. Alternatively, multi-dimensional data represented successfully by a digital twin adds tremendous value to enterprises. Compared to traditional industrial control systems, IoT is relatively young and the digital twin concept is still maturing.
However, enough successful examples are operating in the world that these principles cannot be ignored. IoT solutions have leveraged digital twins in various ways, from simple (but eye-catching!) robotic arm images with sensor data superimposed to extremely complicated algorithms and visualisations that generally require a PhD to comprehend. Although the applications for digital twin technology are robust, their impact on the manufacturing sector cannot be understated.
When starting with a well-thought-out data object, the digital twin analytics transforms each maintenance and management team’s unique ways of work, providing a valuable tool for comparisons, analytics, what-if scenarios and meaningful traceability within the manufacturing process. Unlike real-world devices, implementation of the digital twin enables real-world machine learning algorithms to aggregate operational and performance data, learn from it and predict the future.
Additionally, the digital data from the digital twin allows traceability, history and data analytics of the real-world device, making decision-making less obscure and more data-driven. And with more (organised) data comes more opportunities to enhance the surrounding manufacturing process where the digital twin is installed, enabling previously hidden optimisations.
The Right Gateway for the Right Application -- Connecting the “I” with the “oT”
Although IoT technology and cloud technology have a strong, complementary relationship, there are times when a lack of persistent internet connection can pose as a barrier to operational success. As such, gateways are being used in many IoT installations today. An IoT-focused gateway's primary purpose is to provide remote access to sensors that need a constant connection to the internet. These sensors are typically numerous in quantity, have limited battery life and do not contain enough computing power to operate independently.
Correctly designed and installed gateways can make all the difference between success and catastrophic failure for many business initiatives, both in cost and performance. Think about it; not all applications have the luxury to wait for data to be sent to the cloud, processed and have instructions sent back. What happens if power is lost, a cell tower goes down or someone makes a mistake at a data center? Manufacturers know full well that the financial implications of unplanned downtime can render devastating results, so gateways are crucial to any IIoT environment.
This is where the “edge” comes in and gateways can play a critical role in mitigating disaster. In some cases, the sensor information is processed and acted upon on-site without needing a persistent connection to the internet. This is incredibly important when massive amounts of data should not or cannot be sent to the cloud or when an immediate response is needed (think life or death safety situations). In these applications, gateways that sit at the “edge” of the network can have the intelligence to make decisions locally when a connection to the internet is neither available nor needed, making edge computing extremely attractive to the manufacturing industry.
Another requirement to consider when designing or selecting a gateway for specific applications is how fast the data needs to be updated. This depends on what “real time” means to the application and what a tolerable delay is. The data update frequency from the sensor to the cloud can range from days to only a few milliseconds.
Costs are directly linked to the amount of data and frequency that it is uploaded to the internet. This can affect the profitability or feasibility of an IoT platform. All in all, gateways can translate and collect information from numerous sensors, selectively deciding what information to send to the cloud and when to send it. This level of intelligence and sophistication is usually not found or needed directly in each sensor. It would be redundant, costly and challenging to maintain for operators. Successful IoT implementations provide the right balance of sensor complexity, gateways and intelligent decision-making capabilities when time is essential or the internet is not available.
Although manufacturing organisations must allow the business to drive any technological implementation, instead of allowing technology to conduct business, evolving applications to meet personalised needs is an inherent benefit of implementing IoT solutions. As Industry 4.0 continues to make its way into manufacturing floors across the globe, the manufacturing companies that successfully transition to Industry 4.0 will be those that use IoT solutions effectively to meet their own unique needs.
Aaron Ganick, CEO of Preddio Technologies Inc.